|
К ВОПРОСУ ВОРОНЕНИЯ ОРУЖИЯ
Канд. тех. наук Голик М. А.
(Журнал охотник, №36/3/2010 год)
Наиболее распространенным материалом, используемым для изготовления оружия и амуниции, есть железо.
С течением времени менялись как формы железного оружия, так и методы обязательного ухода ним. Причины такого ухода кроются в природных свойствах этого металла. Наиболее важным из этих свойств является склонность железа к коррозии - необратимому процессу разрушения с потерей полезных свойств под действием коррозионных факторов окружающей среды.
В эпоху рыцарства было принято содержать доспехи в состоянии блеска, что с одной стороны предупреждало скопление на их поверхности коррозионно-активных влаги и солей, а с другой подчеркивало доблесть и отвагу война.
С появлением дальнобойного точного оружия психологическое действие блеска и шума армий уступило место более эффективной тактике скрытности и внезапности. Изменения в тактике ведения боевых действий вызвало необходимость использования таких покрытий металлического оружия, которые кроме уменьшения демаскирующего эффекта также гарантировали высокую защитную эффективность. Среди таких покрытий с начала XVI века существенное распространение получило воронение.
Вопросу воронения оружия, в том числе охотничьих ружей, посвящены работы многих исследователей, среди которых С. Бутурлин, Л. Ямпольский, П. Лаворко, Дж. Бертольд, В Лайнер, Х. Клевер.
Разработано несколько сотен оригинальных методик, с помощью которых можно получать защитные покрытия разных цветов и оттенков - от розового до бархатно- черного.
В зависимости от способа нанесения защитного слоя на металл воронение можно отнести к одному из следующих типов:
- Термическое — характеризуется окислением стали при высоких температурах ( в атмосфере перегретого водяного пара при 200—480 °C, а также в воздушной атмосфере при 310—450 °C с предварительным покрытием поверхности деталей тонким слоем растительных или минеральных масел).
- Реагентное (Химическое) — образование защитных пленок окислением металла под действием химических реагентов (паст, растворов кислот, солей, щелочей).
- Термо – реагентное — характеризуется образованием защитных пленок под действием повышенной температуры и химических реагентов (расплавов солей при 400—600 °C, в парах аммиачно-спиртовой смеси при 520—880 °C).
- Электрохимическое — нанесение защитных пленок в среде электролита под действием электрического тока.
Можно заметить, что в основе большинства методик воронения лежит процесс окисления металла. Эффективность этого процесса тем более высока, чем выше склонность металла к коррозии. Другими словами с повышением антикоррозионной способности сталей (увеличением содержания легирующих добавок) уменьшается восприятие к воронению. Разница между процессом воронения и коррозии в том, что при воронении образуются продукты окисления железа, характеризующиеся низкой пористостью, а также высокой адгезией к металлу. Продукты коррозионных процессов пористы, пропускают через себя к металлу коррозионные агенты (воду, кислые газы, растворы солей), имеют низкую адгезию и легко удаляются, оголяя чистый металл.
До первой половины ХІХ века наиболее распространенным был коричневый оттенок защитных пленок, который со временем потеснился зарекомендовавшим черным воронением (из-за большей защитной эффективности черного оксида железа FeO над коричневой Fe2O3). Поэтому в наше время очень редко встречаются коричневые вороненые изделия, а на прилавках красуются классически черные ИЖы, ТОЗы, САЙГи, Бамы, Алтайи, Береты, Бенелли и Браунинги.
Некоторые дорогие ружья, например Алтай, покрываются черным хромом, часто более стойким, чем оксид железа (ІІ) покрытием.
В тоже время большинство оружия имеет классическое заводское воронение, которое со временем может стираться, открывая чистый металл. В этой ситуации необходимо как можно быстрее восстановить или обновить защитное покрытие, так как оголенный металл с внешней стороны ружья может корродировать сам, а также (образуя гальваническую пару) способствовать коррозии внутренней стальной поверхности ствола.
В современных информационных источниках содержится довольно много способов воронения, которые отличаются сложностью исполнения, защитным эффектом, долговечностью и цветом покрытия. Однако не приводится сравнительная информация о их особенностях, а также противокоррозионных свойствах защитных пленок, нанесенных с их помощью.
С целью сравнения эффективности защитных пленок, полученных доступными методами воронения, исследовали процесс их образования, а также противокоррозионную способность.
В качестве материала для воронения использовались пластины, изготовленные из стали 50. Для большей адгезии пленки к металлу поверхность пластин непосредственно перед воронением зачищалась, полировалась и обезжиривалась ацетоном. Завороненные пластины промывались дистиллированной водой, сушились и не менее суток вымачивались в масле И-20А. Защищенные пластины испытывались на противокоррозионную (защитную) способность в условиях камеры солевого тумана (метод 4, ГОСТ 9.054). Оценивали степень поражения коррозией (ржавые пятна) вороненой поверхности пластин.
Ниже описаны методики, по которым проводили воронение стальных пластин.
№1. Ржавый лак.
Этот метод воронения известен довольно давно. Суть его сводится к обработке металла коррозионно-активной средой в результате чего на поверхности образуются черная и рыжая окиси железа. Рыжая ржавчина легко удаляется щеткой, а черная окись железа остается. Операции ржавления металла и удаления рыжей ржавчины повторяются до тех пор, пока вся металлическая поверхность не покроется исключительно черной окисью.
Оржавляющий состав готовили следующим образом:
В фарфоровую чашку, под тягой, наливали около 12 грамм соляной кислоты (удельный вес 1,19). Туда же небольшими порциями высыпали 32 грамма размельченной железной ржавчины, потом по каплям добавляли 22 грамма азотной кислоты (удельный вес 1,35). К образовавшейся смеси досыпали железный порошок (опилки) – 8 г, при этом начиналась реакция с выделением бурого газа. После прекращения реакции (через сутки) смесь разбавлялась водой (50 мл) и водкой (50 мл). Раствор отстаивали и сливали, отделив от выпавших солей и не прореагировавшей окалины.
Образовавшийся раствор на металлические пластины наносили при помощи ватного тампона, повторяя нанесение 3 раза (через 30-40 минут). Для ржавления пластину размещали во влажном месте на сутки. После ржавления пластину чистили от коричневой ржавчины металлической щеткой. После чего пластину опускали в кипящую воду на 5 минут (оставшаяся после чистки коричневая окалина превращается в черную). Операции нанесения ржавого лака, чистки, и промывки горячей водой повторяли 9 раз, в результате чего образующаяся черная пленка перестала удаляться металлической щеткой, а пластина приобрела насыщенный черный цвет. После этого черную поверхность пластины полировали грубой тканью, и сутки пропитывали маслом. На рис.1.а приведено фото пластины завороненной по этому методу.
Этот метод, дающий прекрасные результаты в части прочности покрытия имеет несколько недостатков, главный среди которых – длительный срок нанесения, поэтому в промышленных масштабах чаще используют другие способы воронения деталей, среди которых химическое щелочное оксидирование.
№2. Химическое оксидирование в щелочной среде.
В основе щелочного оксидирования лежит тот же процесс окисления железа.
Используя фарфоровую чашку, в 100 мл воды, полностью (до исчезновения твердого остатка) растворяли 120 грамм каустической соды и 30 грамм азотнокислого натрия. Смесь нагревали до кипения (130-140оС) и погружали пластину. Через 20 минут почерневшую пластину вынимали, многократно промывали дистиллированной водой, сушили и обрабатывали маслом (Рис. 2а ).
№3. Обработка гипосульфитом натрия
Основное действующее вещество этого состава – гипосульфит натрия (используется в фотографии). Готовили раствор 50 грамм гипосульфита натрия в 500 миллилитрах воды. Добавляли 3 грамма фосфорной кислоты, 1 грамм азотной кислоты и 30 грамм хлористого аммония. Смесь перемешивали до полного растворения. Обработку пластинки проводили кистью, после чего выдерживали 1 час при комнатной температуре, наблюдая при этом постепенное чернение. После водной промывки и обработки маслом цвет пластинки несколько терял глубину, хотя все же оставался черным (Рис. 3а ).
№ 4. Покрытие сульфидом меди.
Растворяли медный купорос до отказа в воде, и на стакан раствора прибавляли 5 капель концентрированной серной кислоты. В образовавшийся раствор погружали нашу пластинку, пока она не получит цвет красной меди (около 10-15 мин) после этого ополаскивали водой. Далее пластинку на 20 минут полностью опускали в раствор гипосульфита натрия, полученный как это описано в предыдущем методе (№3). Затем следовали промывка водой, просушка и обработка маслом (Рис. 4а ).
№ 5. Обработка электролитом.
По этому методу раствор для воронения готовили, поочередно растворяя в 100 миллилитрах воды 3 грамма хлористого цинка, 6 грамм медного купороса. Этот раствор многократно (14 раз) наносили на пластину, причем после каждого смазывания протирали мягкой тряпочкой. После полной обработки промасленная пластинка имела темно- коричневый, почти черный оттенок (Рис. 5а ).
№6. С использованием растительных масел и печи.
Этот метод является чуть ли не самым древним, воспроизводимым на кухне чуть ли не каждой хозяйкой относительно своей сковороды.
На пластину очень тонким слоем наносили растительное масло (обычно, для получения более глубокого черного цвета рекомендуется конопляное, но мы брали подсолнечное). Обработанную маслом пластину, используя муфельную печь, подогревали до 200-250 оС и выдерживали при этой температуре 10-15 мин, после чего остужали и повторно наносили масло. Для получения более - менее устойчивого цвета таких циклов «намазывания и нагрева» пришлось провести 3 (Рис. 6а ).
В продаже имеются составы быстрого чернения «NU-BLACK: Blacking cream № 82» в виде пасты, и KLEVER Schnellbrunierung жидкость синего цвета, которые в считанные минуты дают возможность нанести воронение на нелегированные стали. Легированная сталь, содержащая 3% хрома и более, этим средствам не поддается. Воронение этими составами были обозначены как методы №7 и №8 соответственно (Рис. 7а и 8а).
Также довольно известным способом борьбы с коррозионным поражением является использование преобразователей ржавчины, которые кроме как снятия ржавчины модифицируют металлическую поверхность, придавая ей повышенную антикоррозионную стойкость. Поэтому интересно было также определить антикоррозионную стойкость металлической поверхности обработанной преобразователем ржавчины. Как преобразователь ржавчины нами было использовано средство INFINIUM (Рис.10) .Оно не только эффективно удаляет ржавчину и старое воронение, но также восстанавливает зеркальный блеск алюминиевых, хромированных и никелированных изделий. Метод обработки металлических пластин преобразователем ржавчины INFINIUM был обозначен как №9.
Итак, рассматривая технологию выполнения воронения в приведенных методах, можно сделать выводы об их относительной сложности.
Наиболее простыми по технике исполнения являются методы №8, №9 (нанесение на металлическую поверхность составов «NU-BLACK: Blacking cream № 82» и KLEVER Schnellbrunierung). При использовании этих средств чернение наших пластин происходило довольно быстро. Также довольно быстро (без подогрева в течение часа) можно зачернить деталь, используя методику №3. Способ №4 несколько более сложен: требует и приготовления использования нескольких растворов, и промежуточной промывки. Несколько более сложными являются методики №6, и №2. Однако, если попрактиковаться (и найти необходимую посуду из фарфора или нержавейки), то методика №2 не будет казаться такой уж сложной, так как сам процесс чернения детали обычно длится не больше 30 минут. Наибольшим же терпением мастер должен запастись, берясь за воронение с использованием ржавого лака (метод №1) или раствора солей цинка и меди (метод 5). Сложность этих способов заключается в многократном повторении циклов нанесения составов воронения, механической обработки и промывки.
Теперь перейдем к описанию характера защитных пленок, получаемых с помощью приведенных методик.
Пластина, обработанная по методу №1 (ржавый лак), имеет легкий коричневый оттенок. Распределение цвета по поверхности равномерное, но в некоторых местах имеется легкий питтинг (серые пятнышки на фото), которого можно избежать, разбавив раствор воронения водой. Неоспоримым плюсом покрытия, полученного этим методом, является его стойкость к механическому износу.
Покрытие, полученное методом №2 (Оксидирование в щелочной среде), имеет глубокий черный цвет с синеватым отливом. Поверхность пластины гладкая, стойкая к износу и не требует последующей полировки.
Глубокий черный цвет и высокую однородность имеет пленка, полученная по методу №3 (Обработка гипосульфитом натрия). Однако, это покрытие характеризуется наибольшей склонностью к истирании и скорее всего не годится для обработки ружей и ножей.
В отличии от метода №3 метод №4 приводит к образованию более износостойких пленок, которые тем не менее характеризуются высокой шероховатостью и низкой однородностью цвета. Так, например пластина, завороненная этим способом, содержит выступающие пятна (Рис. 4а, правая сторона) и пупырышки (левый нижний угол).
Покрытие, полученное методом №5, имеет коричневый цвет и также содержит элементы неоднородности поверхности, причем еще в большем количестве, чем покрытие, полученное методом №4.
Что касается метода №6 то, как можно убедиться (Рис. 6а), поверхность металла, обработанная с его применением, приобрела синевато- черный цвет. Сама же пленка оказалась довольно стойкой к истиранию.
Методы №7, №8, в которых были использованы средства холодного оксидирования, дали внешне одинаковый результат - черные пленки с коричневым оттенком. Причем защитная пленка, полученная с помощью состава KLEVER Schnellbrunierung характеризуется более высокой стойкостью к истиранию чем пленка, наведенная составом «NU-BLACK: Blacking cream № 82».
Метод испытания защитных свойств пленок, применяемый в наших испытаниях, дает возможность узнать каким же будет завороненный предмет (ружье, пистолет, нож ) через пол года при его хранении в гараже или в сарае без ухода, а также без специальной тары и промасленной бумаги, но с использованием масла И-20А (не содержащего присадок) в качестве консерванта. Результаты наших испытаний приведены в таблице и на соответствующих рисунках (Рис. 1-9 (б) ).
а б
Рис. 1. Фото стальной пластины завороненной по методу №1 (Ржавый лак); а- до, и б- после испытания на коррозионную стойкость.
а б
Рис. 2. Фото стальной пластины, завороненной по методу №2 (Оксидирование в щелочной среде); а - до и б- после испытания на коррозионную стойкость.
а б
Рис. 3. Фото стальной пластины, завороненной по методу №3 (Обработка гипосульфитом натрия); а - до и б- после испытания на коррозионную стойкость.
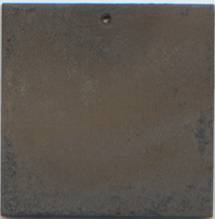
а б
Рис. 4. Фото стальной пластины, завороненной по методу №4 (Покрытие сульфидом меди ); а - до и б - после испытания на коррозионную стойкость.
а б
Рис. 5. Фото стальной пластины, завороненной по методу №5 (Обработка электролитом); а - до и б - после испытания на коррозионную стойкость.
а б
Рис. 6. Фото стальной пластины завороненной по методу №6 (С использованием подсолнечного масла); а – д о и б - после испытания на коррозионную стойкость.
а б
Рис. 7. Фото стальной пластины, завороненной составом быстрого чернения «NU-BLACK: Blacking cream № 82» (метод №7); а- до, и б- после испытания на коррозионную стойкость.
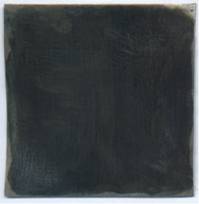 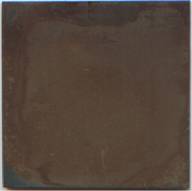
а б
Рис. 8. Фото стальной пластины, завороненной составом быстрого чернения KLEVER Schnellbrunierung (метод №8); а- до, и б- после испытания на коррозионную стойкость.
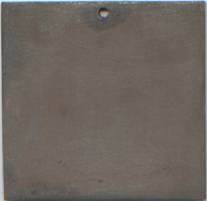
а б
Рис. 9. Фото стальной пластины, обработанной преобразователем ржавчины INFINIUM (метод №9); а- до и б- после испытания на коррозионную стойкость.
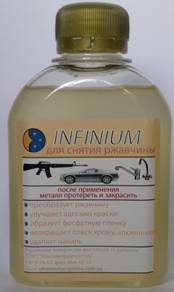
Рис. 10. Универсальное средство INFINIUM (для удаления ржавчины и воронения, а также восстановления блеска алюминия, хрома и никеля).
Как свидетельствуют данные испытаний (Рис. 1-9, Табл.), наилучшая антикоррозионная устойчивость характерна для пластины, обработанной по методике №2 (Оксидирование в щелочной среде). Поверхность этой пластины за 8 часов испытаний прокорродировала на 10%. Поверхности пластин, вороненых по методикам №1 и №6 через 6 часов пребывания в камере солевого тумана прокорродировали приблизительно на 65 и 45%
Пластины, обработанные по методикам №№ 3, 4, 5, а также методами №7, №8 с применением составов холодного оксидирования, уже через 4 часа пребывания в камере солевого тумана имели более чем 90% коррозионное разрушение поверхности, что свидетельствует о крайне низкой антикоррозионной эффективности этих методов воронения. Что касается метода №9 (обработка средством INFINIUM), то его антикоррозионная эффективность заняла промежуточное место между методами №1,№2,№6.
Учитывая практический опыт применения защитных средств, а также результаты испытаний противокоррозионной эффективности пластин, можно приблизительно указать термин хранения металлических предметов, вороненых указанными методами. Итак, железная амуниция вороненая методами №1, №6, №2 и не законсервированная должным образом в складских условиях способна сохранять внешний вид соответственно 2-2,5; 4-5; и 2-3 месяца. Оружие же, вороненое методами №№ 3, 5, 7, 8 без использования эффективных средств консервации, может находиться на складе около месяца. Методики №3 и №4 скорее уменьшают антикоррозионное сопротивление, чем прибавляют защитный эффект металлических предметов, которые в складских условиях могут храниться не более недели.
Таблица
Результаты испытаний защитной способности
Номер и наименование способа обработки |
РЕЗУЛЬТАТЫ ИСПЫТАНИЙ |
Время до появления ржавчины на вороненой поверхности Ст50 (с маслом И-20А) |
время до появления признаков коррозии, сутки |
площадь пластины Ст50 пораженная коррозией через 8 часов, % |
№1, Ржавый лак |
3 |
65,0 |
до 2,5 месяцев |
№2, Оксидирование в щелочной среде |
4-5 |
10,0 |
до 5 месяцев |
№3, Обработка гипосульфитом натрия |
0,5 |
100,0 |
- |
№4, Покрытие сульфидом меди |
1,0 |
95,0 |
до 0,5 месяцев |
№5, Обработка электролитом |
1,5 |
90,0 |
до 1 месяца |
№6, С использованием подсолнечного масла |
3,5 |
45,0 |
до 3 месяцев |
№7, Средством быстрого чернения «NU-BLACK: Blacking cream № 82» |
2,0 |
100,0 |
до 1 месяца |
№8, Средством быстрого чернения KLEVER Schnellbrunierung |
2,0 |
100,0 |
до 1 месяца |
№9 Средством INFINIUM |
2,5 |
85,0 |
до 1,5 месяцев |
Без обработки |
1,5 |
95,0 |
до 1 месяца |
Учитывая сложность методов воронения, а также защитную эффективность образуемых пленок, можно констатировать, что для воронения ножей, кортиков, сабель, мелких частей огнестрельного оружия наиболее приемлемым будет метод №2 – оксидирование в щелочной среде. Не смотря на то, что для этого метода характерны сложности в исполнении (поиск нержавеющей или керамической посуды, а также кипячение щелочи), качество покрытий, наносимых с его помощью, является наилучшим. Применение же щелочного оксидирования для стволов ружей усложняется поиском термостойких пробок (для затыкания ствола) и ванны соответствующего размера. Несколько более простым для воронения стволов является метод 6 (воронение с покрытием маслом). В этом случае, кроме растительного масла, необходимо иметь лишь нагревающую печь по длине ствола, либо газовую горелку необходимой мощности. При нежелании иметь дело с нагревом металлоизделий, можно прибегнуть к методу «ржавый лак» и получить стойкое к износу и также довольно эффективное защитное покрытие.
Что касается средств холодного воронения, то их нежелательно использовать для воронения изделий, находящихся в повседневном использовании, так как противокоррозионная эффективность покрытий, образуемых ими, является крайне низкой. А из-за того, что средства холодного оксидирования содержат тяжелые металлы и оксид селена, их использование для обработки предметов, контактирующих с пищей недопустимо.
Перечисленные выше средства и методики доступны современному охотнику, и только его выбор определяет, как и чем будут покрыты его железные спутники.
|
|