|
ВСТУП
Однією
з найважливіших проблем, що доводиться вирішувати нафтохімічному комплексу є
проблема виробництва засобів захисту металовиробів від корозії.
Метал і
досі залишається основним конструкційним матеріалом,
незамінним у ряді важливих галузей промисловості і сільського господарства.
Але, не дивлячись на ряд позитивних конструкційних
якостей, вироби з металу, під дією агресивних агентів
середовища, здатні незворотньо руйнуватись, та втрачати
корисні функціональні властивості.
Корозія завдає суттєвих збитків як світовій економіці так і
економіці окремих країн. Близько 20% всього металу, що виробляється у світі за
рік, втрачається внаслідок корозії [1]. За даними експертних оцінок, в Україні, від корозії, втрачається близько 10-15% усього виробленого чорного металу [2].
Збитки від корозії умовно поділяють на прямі і непрямі. Прямі
збитки полягають у втраті маси самого металу та змешенні собівартості
інженерних рішень на його основі. В світі
збитки від втрати металу, в наслідок корозії, оцінюються у міліардах дол. на
рік, і мають тенденцію до постійного підвищення.
Непрямим збиткам від корозії характерна більша масштабність, що
ускладнює проведення їх економічних підрахунків. До непрямих збитків відносять
збитки від зупинок виробництв, вибухів, пожеж, екологічних лих, аварій на
нафто та газогонах, руйнування резервуарів та транспорних комунікацій, наземних
і підземних споруд тощо [3].
З питанням захисту металів від корозії тісно пов'язане розв'язання таких
проблем, як, підвищення ефективності металоємних
виробництв, зростання ВВП та поліпшення екологічного становища [4].
Про значущість даної проблеми свідчить те, що в деяких країнах, з метою контроля та запобігання
корозійних втрат створено спеціальні ради, комітети та інститути. Зокрема, в
Україні у 1992 році засновано
Українську асоціацію
корозіоністів, президентом якої є член-кореспондент НАН України, д.т.н., професор Похмурський Василь Іванович.
Боротьбі
з корозією присвячені роботи багатьох вчених, економістів, інженерів, діячів
тощо. В свій час проблемою корозії металів займались:
М.
В. Ломоносов, А.Н. Фрумкін, Ю.Н.
Шехтер, В. М. Школьніков, И.Л. Розенфельд,
Л.И. Антропов, Я.М. Колотиркін, С.А.
Балезін, Є.С. Іванова, В.І. Похмурський, Н.І. Подобаєв, Ю.І. Кузнєцов, Ю.М.
Лошкарев, З.А Іофе, В.М. Ледовських, В.В. Кузнєцов, В.П. Григор’єв, В.В.
Екілік, І.С. Погребов, Ю.В. Федоров, Г.В. Халдєєв, А.С. Афанасьєв, С.М.
Решетніков, Г.Н. Бараннік, і ін.
Існує більше ніж 40 видів корозії серед яких
кислотна, підземна, контактна, воднева, пітінгова та ін.
Серед усіх видів корозії найбільших збитків завдає
атмосферна корозія [5].
Розроблено
велику кількість методів та засобів, що гальмують процеси атмосферної корозії металів та відповідно
знижують корозійні втрати.
Усі
рішення, що мають за мету захист металовиробів від атмосферної корозії умовно поділяють на заходи постійного і
тимчасового протикорозійного захисту.
Постійний
протикорозійний захист металовиробів передбачає використання корозійностійких
матеріалів (легованих сталей, полімерів, композитів, кераміки та ін.),
різноманітних покриттів, тощо.
У
деяких випадках економічно виправданим є застосування тимчасового
протикорозійного захисту [5, 6].
Під
тимчасовим протикорозійним захистом металовиробів розуміють комплекс заходів,
що поновлюються і мають на меті захист металовиробів від корозії під час
виготовлення, міжопераційного та довготривалого зберігання, транспортування та
експлуатації [5].
Найбільш розповсюдженими засобами тимчасового захисту
металовиробів від корозії (ЗТЗМ) є консерваційні
оливи, які характеризуються суттєвою захисною здатністтю, легкісттю нанесення
та розконсервації, тіксотропністтю захисних плівок, доступністтю компонентів,
відносною пожежобезпечністтю при використанні (наприклад, порівняно з ПІНЗ) [5].
На
даний час відома досить велика кількість засобів тимчасового захисту
металовиробів від корозії (ЗТЗМ). Але їх асортимент постійно розширюється, що
зумовлено змінами у виробничій та сировинній базах, корозійній активності
середовищ, у вимогах металоємних виробництв, а також постійною тенденцією
підвищення ефективності ЗТЗМ разом із зменшенням їх собівартості, токсичності
та навантаження на екологію середовища [7-12 ].
Обов´язковими компонентами консерваційних олив і
деяких інших ЗТЗМ, що визначають їх захисну
здатність та впливають на основні властивості, є оливорозчинні інгібітори
корозії (ОІК).
АКТУАЛЬНІСТЬ ТЕМИ
Україна є
одним з найбільших виробників експортників металовиробів у Європі. Продукція українських металоємних виробництв широко
представлена як на міжнародному так і на внутрішньому ринку.
Для попередження корозійного враження металовиробів під час
транспортування та зберігання застосовують засоби тимчасового захисту
металовиробів (ЗТЗМ), в тому числі консерваційні оливи.
Якість захисту металовиробів від корозії залежить, як від
технологій їх виготовлення, так і від рівня технологічності та ефективності
консерваційних олив (та ін. ЗТЗМ). З метою підвищення якості і
конкурентноспроможності продукції, сучасними металоємними виробництвами ставляться
нові вимоги до консерваційних олив та ЗТЗМ, серед таких вимог виділяють:
безпечність, легкість нанесення і розконсервації, високий рівень захисної
ефективності, поліфункціональнісь, технологічність та естетичний вигляд
захисного шару.
Важливим
завданням нафтохімічної промисловості є створення речовин та технологічних
засобів, що сприяють розвитку провідних галузей народного господарства.
Виробництво консерваційних олив, що відповідають вимогам
сучасних металоємних виробництв неможливе без застосування доступних
високоефективних оливорозчнних інгібіторів корозії.
З
даних аналізу асортименту консерваційних матеріалів встановлено, що на ринку
України присутні ОІК вітчизняного та закордонного виробництва причому
інгібітори корозії вітчизняного виробництва за рівнем захисної здатності значно
поступаються сучасним закордонним аналогам.
З
літературних даних відомо, що високоефективними та простими у виробництві є ОІК, створені на основі амідів.
Аналіз вітчизняної сировинної бази вказує на те, що вихідною сировиною для одержання таких ОІК може
карбамід та жирні кислоти рослинних олій.
Однак в літературі міститься обмежена інформація, щодо
особливостей процесу одержання, хімічного складу та властивостей таких інгібітрів,
промислове виробництво яких ОІК в Україні відсутнє.
Тому
розробка нових ефективних ОІК, з урахуванням вітчизняної сировинної бази та
сучасного стану виробництв є актуальною.
Мета і завдання дослідження Метою роботи є розробка ефективних оливорозчинних інгібіторів корозії
на основі похідних карбаміду.
Для досягнення мети досліджень були поставлені наступні завдання:
- Вивчити особливості синтезу інгібіторів корозії на
основі похідних карбаміду.
- Провести синтез
оливорозчинних інгібіторів корозії на основі похідних карбаміду;
- Дослідити вплив рецептурно-технологічних
факторів на основні властивості оливорозчинного інгібітору корозії;
- Встановити
закономірності впливу вуглеводневого складу та характеристик базових олив на
захисні властивості консерваційних олив на основі нового оливо розчинного
інгібітору корозії.
- Дослідити взаємний
вплив ІК та оливорозчинних додатків різної функціональної дії на основні
властивості консерваційних олив.
- Розробити рецептуру консерваційної
оливи на основі нового оливорозчинного інгібітору корозії.
- Порівняти основні
властивості нових та відомих змащуючих засобів тимчасового захисту
металовиробів від корозії, встановити рівень їх захисної здатності відносно
чорних металів для різних умов випробуваннь.
2. ЛІТЕРАТУРНИЙ ОГЛЯД
2.1 КОРОЗІЯ
Під корозією розуміють таку взаємодію між металом і
середовищем, що призводить до погіршення функціональних властивостей металу,
середовища або їхньої системи [5].
Більшість металів, від моменту виплавки піддаються дії корозійних
факторів оточуючого середовища. Вироби з чавуну та сталі кородують скрізь, де б
вони не знаходилися: у повітрі, в землі чи у воді [13].
В залежності від хімічного
складу середовища,
умов протікання та виду
корозійних руйнуваннь вирізняють близько 40 видів корозії: атмосферну, газову, контактну, біокорозію, щілинну, корозію при
тертті та ін.[10-16].
Вузли і деталі автомобілів,
сільскогосподарської,
будівельної і військової техніки, верстати, інші металовироби під час виготовлення, транспортування, збереження, періодичної або постійної
експлуатації піддаються практично усім видам корозії, з яких найбільш
пошириною є атмосферна корозія [5].
Атмосферна корозія, як умовний вид корозії, є сукупністтю корозійних процесів, що
відбуваються на поверхні металів при їх контакті з атмосферою. Під час
зберігання та транспортування металовиробів, поверхня останніх може
контактувати з частинками грунту, пилу, золем сольових розчинів тощо. В
результаті опадів або атмосферної вологи, на поверхні металу утворюються
адсорбційна або конденсаційна плівки вологи, які при взаємодії з кислотними
оксидами та солями атмосфери утворюють електроліти [13, 14, 17].
Крім того, наявність приповерхневої плівки вологи
сприяє розвитку мікроорганізмів – біологічних активаторів корозії [18].
Таким чином велика різноманітть чинників атмосферної
корозії здатна викливати всі різновиди пошкодженнь і призводить до перебігу
атмосферної корозії в найрізноманітніших умовах: при транспортуванні та
зберіганні металовиробів на відкритих площадках, під навісом, в опалюваних і неопалюваних
приміщеннях, при експлуатації [5].
Для успішної боротьби з
атмосферною корозією необхідно встановити природу, складові, характер,
механізм, умови та основні чинники перебігу процесів атмосферної корозії.
Природа та складові
атмосферної корозії. За
своєю природою корозія як взаємодія корозійних агентів середовища з металом, є
гетерогенним процесом [19].
Атмосферна корозії включає не менш трьох складових,
руйнівний цикл яких можна розглядати як його циклічні стадії в наступному
порядку[19]:
1)
Підвід корозійних агентів у зону
реакції до поверхні металу;
2)
Безпосереднє окиснення металу, що
призводить до утворення продуктів реакції;
3)
Відвід продуктів реакції з
поверхні металу.
Загальна швидкість корозійного
процесу визначається стадією з мінімальною інтенсивністтю. В свою чергу
швидкість корозійного процесу на кожній із стадій залежить від хімічної природи
металу, середовища, корозійних агентів, а також температури, тиску, освітлення,
механічного впливу тощо.
Інтенсивність підводу
реагентів до поверхні металу визначається швидкісттю дифузії та концентрацією
корозійних агентів у середовищі. Підведення корозійних агентів до поверхні
металу на початковому етапі тісно пов¢язане з інтенсивністтю руйнування первинних оксидних плівок на
металі, а також з інтенсивністтю відводу продуктів корозії.
Інтенсивність відводу
продуктів корозії визначається їх взаємодією із середовищем. У випадку активної
взаємодії продуктів корозії з середовищем швидкість відводу продуктів корозії є
максимальною [20].
Кінетичні особливості атмосферної
корозії. В залежності від
ефективності відводу продуктів корозії виділяють три періоди їх накопичення:
індукційний, перехідний, стаціонарний [13, 21]
В індукційному періоді йде руйнування первинної
оксидної плівки на металі, у перехідному - формування проміжних і кінцевих
продуктів. У стаціонарному періоді встановлюється така швидкість корозії, при
якій кількість продуктів, що утворюються, майже зрівнюється з кількістю
відведених (наприклад, внаслідок розчинення або змивання дощовою водою) [16].
В залежності від здатності
середовища розчиняти продукти корозії розрізняють три типи розвитку корозійних
процесів у часі (мал. 12.5) [13].
● Перший тип характеризується
швидким майже повним припиненням корозії за короткий час (мал. 2.1 крива 1),
внаслідок утворення на поверхні металу щільної, непроникної для корозійних
агентів середовища, пасиваційної плівки з продуктів корозії.
● Другому типу відповідає порівняно
швидкий початковий корозійний процес з наступним нарощуванням захисного шару
продуктів, що неруйнується або частково руйнується у середовищі або має пори
через які можливий доступ корозійних агентів до поверхні металу (мал. 2.1 крива
2).
● Третій тип характеризується утворенням продуктів корозії,
які майже не мають захисного ефекту і легко руйнуються. Окиснення цих металів
підкорюється лінійному законові (мал. 2.1 крива 3).
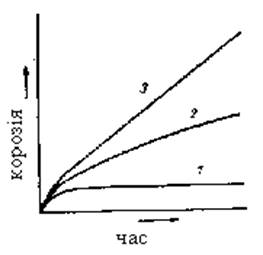
мал. 2.1
Швидкість корозії в залежності від характеру
утворюваних продуктів корозії.
1- група хрому; 2- група міді; 3-група цинку.
Механізми, чинники та умови
атмосферної корозії. Друга
стадія процесу корозії (безпосередня взаємодія корозійних агентів середовища)
може відбуватися лише за двома механізмами: хімічним та електрохімічним.
Хімічна корозія проходить за законами суто хімічної кінетики гетерогенних реакцій [5, 13-16]. Обов¢язковою
умовою проходження корозії за хімічним механізмом є зменшення енергії Гіббса
системи (ΔG<0) у результаті хімічної реакції [22]. Чинниками атмосферної корозії , що проходить за хімічним
механізмом можуть бути деякі гази: Н2S, SO2, SO3 , NO2 і ін. [13- 15]
Під час хімічної корозії
електрони атомів металу, долають відносно невелику відстань, переходячи до
структури атомів більш електронегативної речовини, що не призводить до виникненням
електричного струму. Така корозія може спостерігатись в неелектролітах чи в сухій атмосфері [14-16, 19]. Електрохімічна корозія характеризується
протіканням електричного струму і проходить за законами електрохімічної
кінетики. У випадку електрохімічної корозії електрони атомів металу долають
велику відстань, порівняно з розмірами самих атомів. Для перебігу
електрохімічної корозії необхідна наявність електропровідного середовища, що
містить речовину яка здатна відновлюватись [14, 15]. Речовина, яка
під час електрохімічного процесу корозії відновлюється, окислюючи при цьому
метал носить назву деполяризатора [23, 24]. Для
проходження електрохімічного процесу корозії рівноважний електродний потенціал
металу повинен бути меньшим за рівноважний електродний потенціал
деполяризатора.
Ед – Ем> 0
Загальна реакція електрохімічної корозії
ділиться на два процеси, що протікають самостійно: анодний (перехід металу в
розчин у вигляді гідратованих іонів) і катодний (асиміляція надлишкових
електронів, які з'явилися в металі в результаті анодного процесу, будь-якими
деполяризаторами — атомами, іонами чи молекулами розчину, які можуть відновлюватись
на катоді).
Dox + ne = Dredox n- катод
Me –ne = Men+ анод
Dox + Me = Dredox n- + Men+ сумарно
Збудниками
(деполяризаторами) в процесах атмосферної корозії є присутні в повітрі: кисень,
вуглекислий газ, сірководень, сірчистий газ, деякі неорганічні та органічні
кислоти (соляна, сірчана, сірчиста, мурашина і ін.) [5, 10, 14].
До умов, що визначають
механізм перебігу корозії належать: природа реагуючих речовин, температура та
її перепад, рівень вологості атмосфери, присутність легко дисоціюючих речовин
(кислот, солей, лугів, деяких газів), активність мікроорганізмів [7, 14-20]. Найважливішою умовою домінування електрохімічних процесів над
хімічними є наявність на поверхні металів електропровідної плівки вологи або
електроліту [10, 13-16].
Зазвичай, незахищені
металовироби, що зберігаються у приміщеннях, під навісами або на площадках
вкриті шаром вологи.
В залежності від ступеня зволоження
кородуючої поверхні атмосферну корозію поділяють на три види [19]:
- волога, коли волога плівка (від 1 мк до
1 мм) утворюється внаслідок краплинної конденсації (вона
спостерігається, коли волога безпосередньо потрапляє на поверхню металу від
дощу, бризок, снігу або при відносній вологості повітря близький 100%);
- конденсаційна, утворюється при відносній
вологості повітря нижче 100% і товщині плівки від 100А до 1 мк (якщо вологість
нижча 100%, можлива капілярна, хімічна і адсорбційна конденсація) ;
- суха, коли шар вологи зовсім відсутній
на поверхні металу при товщині плівки меншій 100А.
Волога і конденсаційна атмосферна корозія
відбуваються під видимою плівкою вологи, і при відносній вологості нижчій 100%
розглядаються як корозія під плівкою електроліту, оскільки у сконденсованій
волозі завжди є розчинені солі, кислоти, луги. Процеси, що розвиваються в цих
випадках, мають електрохімічну природу та високу інтенсивність [25, 26].
Як хімічні так і електрохімічні корозійні
процеси пришвидшуються при наявності в атмосфері сполук, що містять сірку (SO2, SО3, H2S), а також домішки NН3, NO2 і Сl2.
Реагуючи з водою, дані сполуки утворюють речовини, що пошкоджують оксидні
захисні плівки на металах, перетворюючи їх на розчинні у атмосферній волозі
солі [13].
Умови перебігу корозійних процесів
температура та її перепад, вологість, кількість опадів, присутність легко
дисоціюючих речовин, кислот, солей, лугів, наявність в атмосфері корозійно
активних газів, активність організмів багато в чому залежать від географічної
та кліматичної зони в яких проходить процес.
Розрізняють континентальну і морську
атмосферну корозію [13, 24–27]. В свою чергу в континентальній атмосфері
виділяють сільскі, промислові (індустріальні), міські, та тропічні умови
перебігу корозії. [13, 20]
Континентальна атмосферна корозія. Континентальна атмосферна корозія
металів підсилюється через присутність в атмосфері міст і промислових зон
сірковмісних сполук: сірчистого і сірчаного ангідридів, сірководню. При цьому в
присутності вологи утворюються кислоти, що руйнують наявні на металах природні
захисні плівки і прискорюють корозію, оскільки продукти корозії легкорозчинні у
воді [13, 28].
SO3+ H2O = H2SO4
SO2+H2O = H2SO3
MenOm + mH2SO3 =
n Me(SO3)m + m H2O
MenOm + mH2SO4 =
n Me(SO4)m + m H2O
MenOm+H2S = MenSm+
mH2O
Морська атмосферна корозія. У морській атмосфері корозія сильніша,
ніж у континентальній, так як в морській атмосфері міститься велика кількість
солей, які сприяють утворенню електроліту на поверхні металу, а в процесі
корозії руйнують захині оксидні прошарки [13].
Корозійні процеси на металах також
залежить і від пори року. Навесні корозія металів, як правило, посилюється у
зв'язку з таненням снігу, що концентрує за зиму велику кількість
корозійно-активних промислових домішок. Осіння погода теж сприяє інтенсифікації
корозії, так як дощова вода може містити суттєву кількість (до 200 мг/л) мінеральних
солей [19, 25–29].
Таким чином атмосферна корозія може проходити за хімічним
та електрохімічним механізмом, що визначається природою кородуючого металу та
умовами навколишнього середовища. У природних умовах домінуючим механізмом
атмосферної корозії є електрохімічний. Основною причиною домінантності, а
також фактором виникнення електрохімічної корозії є наявність на поверхні
металу конденсаційної або адсорбційної плівки вологи.
Забрудненість повітря корозійноактивними газами, парами
кислот, дустом солей, пилом, мікроорганізмами перетворює плівку вологи, на
поверхні металу, в електроліт, що пришвидшує корозію як за рахунок введення
деполяризаторів так і за рахунок зменшення пасиваційної властивості продуктів
окиснення металу. Волога в корозійних процесах відіграє роль електроліту, тобто
середовища, яке здатне підводити корозійні агенти до металевої поверхні та
розчиняти пасиваційні плівки на поверхні металу.
2.2.
ОСНОВНІ АСПЕКТИ ДІЇ КОНСЕРВАЦІЙНИХ ОЛИВ.
Серед засобів тимчасового протикорозійного захисту металовиробів
найбільше розповсюдження отримали консерваційні оливи, які мають, порівняно з
іншими засобами тимчасового захисту металів від корозії, низку переваг:
-
легкість нанесення та
розконсервації,
-
суттєвий захисний ефект,
-
тіксотропність захисної плівки,
-
відносно високе значення
температури спалаху, що робить застосування консерваційних пожежобезпечним.
Процес
здійснення захисту консерваційними оливами відбувається від моменту їх
нанесення (консервація) до моменту змивання (розконсервація). Виділяють
три етапи у застосуванні консерваційних олив при захисті металовиробів [14, 15]:
-
Консервація – (Утворення захисного
покриву)
-
Перебування металевої поверхні під
захистом (збереження, перевезення металовиробів)
-
Розконсервація – (видалення
консерваційної оливи)
Очевидно,
сумарна ефективність від застосування консерваційних олив залежить від прояву
“корисних” ефектів на кожному з цих етапів. В свою чергу результуюча
ефктивність на окремих стадіях захисту визначається взаємодією компонентів
оливи з металом та середовищем.
Встановлено,
що в більшості випадках домінуючим механізмом корозії є електрохімічний.
Основною умовою виникнення електрохімічних корозійних процесів на металевій
поверхні є наявність плівки вологи. В залежності від умов (перепад температур,
вологість, наявність опадів) поверхня металу майже завжди вкрита конденсаційною
або адсорбційною плівкою вологи різної товщини [30, 31]. Тому на першому етапі застосування - нанесенні консерваційна олива
повинна мати такий склад, що сприяв би нейтралізації корозійних агентів у
вологій плівці, або виштовхував би вологу (електроліт) з поверхні металу [30-34].
Вологовиштовхування, як властивість консерваційної
оливи виштовхувати конденсаційну та адсорбційну плівки вологи з поверхні
металу, є результатом динамічного процесу і залежить від комонентного складу
консерваційної оливи. Виштовхування вологи з поверхні металу може здійснюватись
за двома механізмами [14 - 16, 34]:
1)
Виштовхування води за рахунок
кращого змочування металевої поверхні оливою ніж водою. (Енергія взаємодії
метал-олива є більшою за енергію взаємодії вода-метал) [14].
2)
Поглинання консерваційною оливою
деякої кількості вологи з поверхні металу за рахунок гідрофільності та (або)
гігрскопічності окремих компонентів оливи [14].
Виштовхування вологи консерваційними оливами, за
першим механізмом, пов’язане з поверхневою активністю оливи на межі фаз
олива-метал-вода, і можливе коли справджується нерівність (2.1), мал. 2.2.
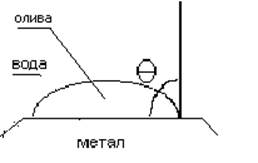
мал.2.2
(σ’мев
– σмев) < (σ’ов – σов) (2.1)
Де σмев-поверхневий натяг на границі
метал-вода
σ’мев-поверхневий натяг на границі метал
(із плівкою води)-олива
σво-поверхневий
натяг на границі олива-вода
σ’ов-поверхневий натяг
на границі адсорбована вода- олива
Вологовідштовхуючу властивість оливи, за першим
механізмом, можна поліпшити шляхом зменшення її в¢язкості,
включенням до її складу оливорозчинних ПАР , що здатні хемосорбуватись на
металевій поверхні [14, 34].
Для збільшення долі механізму “вбирання
вологи” бажано застосовувати “сухі” оливи до яких додають деяку кількість
гігроскопічної речовини (моноетаноламін, триетаноламін, дисперговані оксиди та
карбонати металів Al2O3, ZnO, CaCO3 і ін. [14-16].
Наступним
етапом дії консерваційних олив є утворення на металевій поверхні первинних
сорбційних – хемосорбційних плівок та основних захисних прошарків [14, 15, 33].
Більшість
нафтових олив, після нанесення на металеву поверхню, не здатні утворювати
стійкі захисні плівки. Оскільки їх дія зводиться тільки до механічної ізоляції
металевої поверхні та зародків корозії. [35, 36].
Для
підвищення захисних властивостей в нафтові оливи вводяться речовини, що здатні
утворювати або сприяють утворенню на металевій поверхні стійких, у відповідних
умовах, адсорбційних захисних плівок.
Речовини
які, з оливної фази, на поверхні металів здатні утворювати адсорбційні захисні
плівки і гальмувати корозійні процеси на металі називаються оливорозчинними
інгібіторами корозії [14-16].
Оливорозчинні
інгбітори корозії (ОІК), у своїй
більшості, є поверхневоактивними речовинами (ПАР) із значенням гідрофільно –
ліофільного балансу (ГЛБ) 6-10 [14- 16].
Оливорозчинні
інгібітори корозії класифікують за механізмом уповільнення корозійного процесу,
особливостями одержання та хімічною будовою.
Поверхня
металу, в наслідок неоднорідності, включає ділянки з різною електронною
густиною. Стійке положення молекули ПАР на металі
може досягатися у випадку її адсорбції активною групою, що несе заряд,
зворотній за знаком зарядові ділянки поверхні металу [37, 38].
Тому при
формуванні на поверхні металів захисних плівок велике значення має розподілення
електронних зарядів в молекулі ПАР, яке в свою чергу залежить від полярності та
поляризованності наявних функціональних груп .
В
залежності від електронодонної взаємодії між металлом і ОІК, останні умовно
поділяють на донори електронів, акцептори електронів та інгібітори екрануючої
дії. [39-54]
Такий
розподіл досить умовний, так як одна й таж сама сполука, будучи донором
електронів для одного металу, може бути акцептором для іншого [55, 56].
Характер електроно
донорно-акцепторної (ЕДА) взаємодії багато в чому
обумовлюється структурними особливостями речовин [46-49, 56-61].
Інгібітори корозії донорного типу містять у своїй структурі групи із сильним
негативним сумарним електронним ефектом: NO2, С=О, SO3Н і
ін. Електрони цих груп, переходячи до металу, стають частиною його електронного
газу. На поверхні металу, відповідно до уявлень Б. Трепнела [62] і Р. Зурмана [63],
утворюється позитивний шар диполів.
У випадку якщо на металі присутні позитивно і
негативно заряджені ділянки, такі сполуки будуть адсорбуватись на позитивно
заряджених, електроноакцепторних ділянках, тобто стосовно до процесів
електрохімічної корозії — на анодних ділянках кородуючого металу.
Інгібітори, корозії акцепторного типу містять у своїй структурі групи з позитивним сумарним
електронним ефектом: NH2, NH, MeО, ОН і т.д. Для кращої адсорбції
таких сполук, поверхня металів повинна мати меншу спорідненість до електрона
чим ПАР. Електрони металу переходять на електронні оболонки молекули
інгібітору, електронна щільність на їх поверхні зростає, утворюється
електронегативний шар, що збільшує енергію виходу електрону з металу.
Электронографічними дослідженнями встановлено, що в багатьох випадках атоми
азоту, які містяться у більшості інгібіторів цього типу, вступають у
координаційний зв'язок не безпосередньо з атомами металу, а через атоми кисню,
що входять до складу окисних плівок [64].
Інгібітори акцепторної дії адсорбируются на поверхнях
з відносно високою електронною густиною, тобто на катодних ділянках металів.
Інгібітори корозії екрануючого типу - найменш полярні за даних умов сполуки (ВПІ=2-10%).
Дані інгібітори утворюють адсорбційні плівки, що не дають «ефекту післядії» і
добре видаляються розчинниками.
Насамперед ці інгібітори мають необхідну швидкодію,
добрі водовитісняючі та водоутримуючі властивості. Крім того, інгібітори
екрануючого типу, синергетично підсилюють захисні властивості при сполученні їх
з донорними або акцепторними інгібіторами.
До оливорозчинних інгібіторів екрануючого типу
відносяться: окисленний петролатум, сіль СЖК фракцій С10-12 і
карбаміду, ланолін, полібутен мол. маси 370-1000, алкенілянтарний ангідрид,
ефіри: дибутилфталат, діоктилсебацинат, пентаеритриту і жирних кислот,
дідециловий бензилянтарної к-ти, діетиловий адіпінової к-ти та ін.
Більшість
товарних ОІК складається з декількох компонентів, або одного компоненту, що
мають різні функціональні групи, здатні до внутрішньомолекулярного або
міжмолекулярного сінергізму [65, 66].
Оливорозчинні
інгібітори корозії, як додатки до консерваційних олив, можуть містити одну або
більше індивідуальних речовин, які сприяють :
-
універсальності застосування, щодо різних металів та умов;
-
виникненню синергетичних ефектів;
-
розширенню функцінальності оливи.
При створенні ефективних ОІК необхідно керуватися
принципами одержання комбінованих оливорозчинних
додатків до консерваційних і робоче-консерваційних олив [14-16, 46-49, 55, 56, 67,
68]. Які полягають в сполученні оливорозчинних ПАР — інгібіторів корозії донорного,
акцепторного і екрануючого типів. У цьому випадку інгібітори корозії екрануючої
дії, забезпечують швидке первісне зневоднення поверхні — видалення води з
поверхні металу за рахунок Н-св¢язків, солюбілізацій та ін.
і втриманні її в об¢ємі продукту. На звільненій від води поверхні металу
відбувається сорбція інгібіторів хемосорбційоного типу, причому при поєднанні
донорних та акцепторних інгібіторів створюються найбільш сприятливі умови для
формування міцних хемосорбционих плівок, як на негативних ділянках металевої
поверхні (катодах), так і на позитивних (анодах), з наступним захистом
хемосорбційних плівок і незаряджених ділянок металу шарами інгібіторів
адсорбційного типу з утворенням «структури сендвича» [39].
Консерваційні оливи, для отримання максимального
захисного ефекту, повинні містити речовини з декількома функцональними групами.
Це досягається або шляхом введення декількох різних
додатків, або пакету оливорозчинних додатків, які готуються на основі речовин з
різними функціональними групами.
За
шляхом одержання інгібітори корозії поділяють:
–
Інгібітори корозії добуті із природної сировини (нафти, рослин).
–
Інгібітори корозії отримані з відходів вирбництв та відпрацьованих олив.
–
Синтетичні оливорозчинні інгібітори корозії [14- 16].
До
природних оливорозчинних інгібіторів корозії (ОІК) відносяться кисне-, сірко-,
азотвмісні речовини та поліциклічні сполуки, що містятся у нафті та
нафтопродуктах.
Природні
сірковмісні ОІК це перш за все сульфіди, дисульфіди, тіоефіри, тіопарафіни,
циклічні сульфіди, які містяться у сирій нафті або утворюються при її переробці
[14, 15, 69-73].
Серед
природних азотвмісних ОІК відомі: гомологи піридину, хіноліну, ізохіноліну,
акрідину, та нейтральні гомологи індолу, карбазолу, тіазолу, а також досить
цінні бензтіазол, меркаптобензтіазол, асфальтени та ін. [70-73]. До
кисневмісних ОІК, що містяться у нафті відносяться нафтенові кислоти С6-12 ,С13-15 , [74 - 76].
З погляду економії матеріальних ресурсів доцільними є
використання інгібіторів корозії на основі відходів виробництв та вторинної
сировини [77]. Основними
складовими таких інгібіторів є відходів виробництв: жирних кислот,
капролактаму, кам’яновугільної смоли, оливи ПОД і ін [77-81]. Однак враховуючи те що відходи виробництв
характеризуються непостійністю хімічного складу, а іноді низьким вмістом діючих
речовин, інгібітори, створені на їх основі, часто є малоефективними.
Порівняно
з природними ОІК та ОІК виготовленними на основі відходів виробництв,
синтетичні ОІК зазвичай володіють кращими функціональними та експлуатаційними
властивостями (захисною здатністю, стабільністю оливних систем і ін.), адже
розробка синтетичних ОІК максимально враховує вимоги, що ставляться до
інгібіторів та засосбів тимчасового захисту металовиробів на їх основі [13- 16].
Серед оливорозчинних
інгібіторів корозії перш за все відомі насичені та ненасичені жирні кислоти їх
солі, естери.
Як ОІК
можуть бути використані насичені та ненасичені жирні кислоти різних фракцій, що
одержуютсь окисненням вуглеводнів [82-85], а також гідролізом рослинних олій [86, 87].
Солі
жирних кислот можуть бути отримані з самих кислот або інших солей в результаті
реакції нейтралізації або обміну. Як ОІК найбільш широко досліджені солі лужних
та лужноземельних металів стеаринової кислоти. [88-90].
В якості швидкодіючих
ОІК (а також як синергетичні добавки) застосовують оксиетильовані або
оксипропільовані спирти, феноли, кислоти, аміни, що містять –2 оксиетильні
групи, або 3 – 4 оксипропільні. Сполуки з більшою кількісттю гідрофільних груп
не підвищують захисну здатність оливних композицій, а в деяких випадках
погіршують [16].
Захисною
здатністю, що до металів, володіють оливні розчини модифікованих алкілфенолів
і алкілсаліцилатів [91, 92].
Як
ефективні ОІК відомі ангідриди кислот серед яких алкеніл- янтарні та
піромелітовий ангідриди [93-96].
Серед сірковмісних
ОІК в першу чергу відомі аліл-, алкіл арилсульфонати їх модифікації, осірковані
жири та олії. Одними з набільш вживаних оливорозчинних додатків є сульфонати
металів, які в залежності від хімічного складу, домішок та ступеня поляризації
можуть бути використані як детергентно диспергуючі оливорозчинні додатки так і
як ОІК [97, 98]. Встановлено, що найвищою захисною здатністтю володіють
найбільш полярні оливорозчинні сульфонати, що були одержані з фракцій алкіл
бензолів (tкип= 340-500 оС) [99 – 102]
Алкіл
сульфонати, алкілариларил сульфонати, діалкіларилсульфонати, що їх отримують
сульфатуванням відповідної сировини сірчаним ангідридом, з наступною
нейтралізацією.
Встановлено,
що найвищу захисну ефективність мають моно алкіл арил сульфонати алюмінію,
кальцію, цинку, магнію, амонію [14-16, 103-105]
Серед
азотвмісних ОІК відомі аміни, аміди, аміноаміди, іміди, аміноспирти та їх солі,
імідазоліни, продукти реакції амінометилювання (Основи Манніха) [14, 105 - 108],
оксиетильовані аміни [109].
Відомими
синтетичними ОІК є аміноаміди, зокрема похідні поліетиленполіаміну і СЖК
(ТВК-1, КОСЖК), які є поліфункціональними додатками, що покращують захисну
здатність олив, а також володіють загущуючою властивістю [110, 111].
Ефективними
ОІК є імідазоліни [112-114], які одержують із поліетиленполіамінів та
моноестерів дикарбонових кислот у присутності катіонообмінної смоли КУ-2. Так,
відомий оливорозчинний інгібітор ИКБ-2 отримують із СЖК, єтилендіаміну та окису
етилену [115].
Мають
застосування ОІК на основі морфоліну, оксохіноліну, гуанідину та піридину [113-117].
Як ОІК можуть застосовуватись продукти конденсації амінів, формальдегіду та сполук з рухливим атомом водню (спиртів, фенолів, альдегідів, кетонів і ін.) [118-121].
Одними із
найефективніших класів сполук щодо захисту металевих поверхонь від корозії є
аміни та їх солі [14, 87, 122 - 124].
Високими
захисними властивостями володіє ізобутилдифеніламін [125, 126] похідні
циклогексиламіну, та діциклогексиламіну і ін. [5,
10, 14]. У випадку необхідності
пидвищення захисної здатності амінів проводять їх модифікування сіркою,
фосфором, бромом, іодом [127, 128].
Окрім
загальної антикорозійної дії, аміни проявляють протибактеріальні властивості,
що може бути використано для попередження біокорозії [129].
Аміноспирти
та їх похідні впливають як на захисну здатність так і на деякі інші
функціональні властивості олив. Встановлено, що аміноспирти фракцій С8-С12 та С18-С20 є ефективними інгібіторами корозії і
проявляють біостатичний ефект [130].
В якості
ОІК та інших функціональних додатків до олив вивчено естери олеїнової,
стеаринової, янтарної, глутарової, адипінової, бензойної кислоти, та спиртів:
пентоерітриту, ізопропанолу [131-137], аміноспиртів, 2-етилгексанолу,
етиленгліколю, алілового і бензилового, спиртів [138-145],
Як ОІК
можуть бути використані естери аміноспиртів та жирних кислот, серед них
найбільшого застосування набули естери триетаноламіну (ТЕА). Естери
триетаноламіну синтезують при їх етерифікації жирними кислотами або термолізм
відповідних солей. (схема 4.2.1)
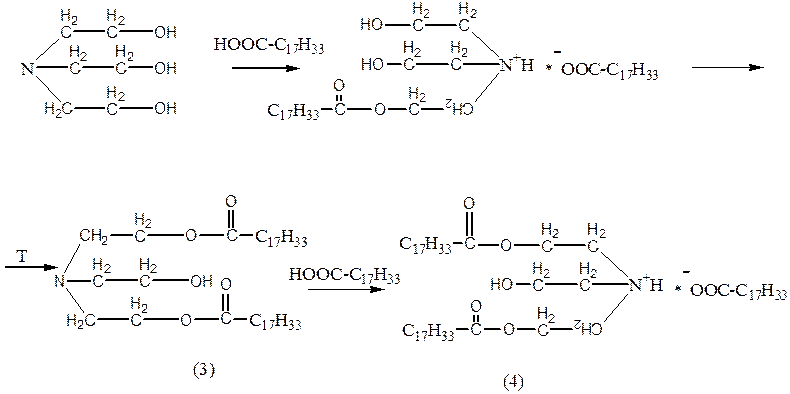 Схема 4.2.1
В промисловості естери триетаноламіну
можуть бути одержані методом «кипятіння» і методом
«відгонки води з азеотропом» [146,
147].
Метод «кип'ятіння» полягає у витримці триетаноламіну з
жирною кислотою при температурі 180°С на протязі 6 годин в результаті чого
отримують суміш продуктів естерифікації триетаноламіну.
За методом відгонки води з азеотропом [146, 147 ], реакція
між триетаноламіном та жирною кислотою проводиться
в бензол-толуольному середовищі. Реакція протікає при t = 110-125°C. У результаті отримують однорідний продукт із чистотою вище 96,5%.
Захисна
здатність естерів триетаноламіну комплексно залежить як від ступеня
етерифікації так і від молекулярної маси карбонової кислоти.
У випадку застосування С17-С22 жирних кислот найвищою захисною здатністю володіють діестери
триетаноламіну[148-151].
Однак захисна здатність естерів
триетаноламіну та жирних кислот є низькою, що, вимагає комбінованого їх
застосування з іншими інгібіторами [152].
Як ОІК відомі
речовини, що отримуються конденсацією алкенілянтарного або малеінового
ангідриду із сполуками у структурі яких присутня аміногрупа (етилендіаміну,
тетраетиленпентаміну, гідразину, тіосечовини, карбаміду) [153-168].
Серед таких інгібіторів найбільш широко відомими є похідні карбаміду : СИМ,
Карбин 1, 2, ИНГА-1 та ін.
Застосування
карбаміду та його похідних у захисті металів від корозії є досить
різноплановим. Карбамід може бути застосований як окрема добавка до
водорозчинних композицій [168] або бути реагентом
у синтезах інгібіторів.
В
синтезах ОІК на основі карбаміду, останній в основному виступає
в якості амідуючого агенту. Так, шляхом амідування алкенілянтарного ангідриду
(1) карбамідом (2) одержують оливорозчинний додаток - СИМ, основними діючими
сполуками якого є алкенілсукциніміди (3) (схема 2.3.7).
де R-
полібутен Мrсер= 1000 г/моль
схема 2.3.7
Похідні
карбаміду, що входять до складу оливорозчинних інгібіторів корозії серії
“Карбин”, отримуються взаємодією алкілсульфокислоти (1) з карбамідом (2). В
залежності від початкової сировини, в основному одержують алкіл, -
алкіларилсулфоуреїди (схема 2.3.8).
де R = akyl (С16-26), akyl(C10-C16)Aryl.
схема 2.3.8
Взаємодією
карбаміду з продуктами нітрування алкенілянтарного ангідриду (2) отримують
нітро-гідрокси-алкіл-сукцинуриїліміди (3), на основі яких створено ОІК ИНГА-1 (схема 2.3.9).
де R- алкіл Мrсер= 960 г/моль
схема 2.3.9
Високу
захисну здатність, а також термостабільність проявляють продукти (3) взаємодії
карбаміду (2) з сульфоксиалкілянтарним ангідридом (1) (схема 2.3.10) [153-159, 168].
де R- полібутен Мr = 1000 г/моль
схема 2.3.10
Взаємодією
карбаміду з карбоновими кислотами можливо отримати відповідні уреїди (схема
2.3.11) [169] та прості аміди карбонових кислот [170, 171] (схема 2.3.12).

Де R- алкіл, алкеніл
схема 2.3.11
Де R- алкіл, алкеніл
схема 2.3.12
Аміди
кислот можуть бути одержані термолізом відповідної карбонової кислоти з аміном,
атом азоту якого зв’язаний не менш ніж з одним атомом водню (схема 2.3.13) [172].
Де R, R/ , R// - H, алкіл, алкеніл.
схема 2.3.13
В якості
ОІК, використовують також аміди вищих карбонових кислот [173].
Відомо [174, 175], що аміди вищих карбонових кислот (АВКК):
СЖК (С10-13Н21-27СОNH2),
лауринової, маргарінової, олеїнової та стеаринової, у невеликих кількостях,
можуть використовуватись як поліфункціональні присадки до індустріальних олив
покращуючи їх захисні, протизношувальні, та реологічні властивості.
Захисна
здатність і інші властивості амідів жирних кислот багато в чому визначаються
будовою органічного радикалу кислоти [176]. Введення
кратних зв’язків в молекулу аміду призводить до деякого підвищення захисного
ефекту, однак захисна здатність інгібітору є недостатньою [177, 178].
При
виготовленні консерваційних олив аміди використовуються у композиціях з іншими
оливорозчинними інгібіторами корозії амінами, жирними кислотами, солями амінів
жирних кислот, естерами і ін.[177,
178, 179].
В той же
час, в роботах не наводяться дані щодо розробки та
принципів створення інгібіторів на
основі продуктів амідування жирних кислот карбамідом. Відсутня інформація про
особливості та оптимізацію технологічного процесу одержання таких інгібіторів.
Згідно даних [178] для підвищення захисної здатності
амідів, їх одержання доцільно проводити так, щоб в результаті утворювалась суміш
амідів з іншими сполуками, які підсилюють їх захисну здатність. При направленому
одержанні сумішей амідів жирних кислот із застосуванням карбаміду, в деяких
випадках, мають місце паралельні реакції з участтю карбаміду, продукти яких
можуть вирішально впливати на властивості, отриманих, таким чином, інгібіторів
корозії. Однак, роль та значення паралельних реакцій, а також їх продуктів, при
одержанні ОІК на основі похідних карбаміду досліджено не було. Так,
враховуючи те, що карбамід є поліфункціональною речовиною при одночасному
введенні з ним в реакцію жирної кислоти та аміноспирту можна очікувати
утворення продуктів з високою захисною здатністю. Процес та продукти взаємодії
карбаміду, аміноспиртів та жирних кислот на сьогодні вивчені недостатньо.
Інформація щодо консерваційних олив створених на основі зазначених інгібіторів
корозії також є обмеженою.
При
розробці консерваційних олив необхідно, окрім високої захисної здатності, враховувати
такі вимоги :
-
технологічність виготовлення;
-
низька вартість;
-
екологічність
-
легкість застосування (простота
консервації та розконсервації).
-
малокомпонентність складу [180, 181].
Щоб відповідати наведеним вимогам, в залежності від
умов застосування, консерваційні оливи повинні мати відповідні значення
фізико-хімічних параметрів: в¢язкість, тепературу
застигання, температуру спалаху, електропровідність і ін. А також володіти
необхідними властивостями, серед яких виділяють: термостійкість,
морозостійкість, біостікість, стійкість до окиснення, водопоглинення (або
водовиштовхування), адгезію до металу і ін.
В залежності від надання консерваційній оливі тих, чи
інших властивостей до її складу можуть входити в певній кількості ті чи інші
компоненти.
В¢язкість
консерваційної оливи залежить від базового компоненту і може регулюватись
введенням спеціальних в¢язкісних
оливорозчинних додатків.
Серед промислових речовин, що
мають загущуючі властивості відомі полімери та кополімери етилену пропілену,
ізобутилену, стиролу метилметакрилату, бітум, віск, петролатум і ін. [13, 16, 182]
Температура спалаху
консерваційної оливи залежить від температури спалаху вихідних компонентів [183].
Температура застигання
консерваційної оливи, багато в чому, залежить від базової оливи. Із підвищенням
у складі оливи парафінових вуглеводнів її температура застигання підвищується [13].
Регулювання температури застигання консерваційної оливи можливе шляхом введення
спеціальних депресорних присадок (ефірів та їх полімерів, терпенів та ін.)[182].
В останні роки широко
використовується в промисловості метод насення консерваційної оливи в
електромагнітному полі [184]. Для наненсення
консерваційної оливи у електромагнітному полі остання повинна мати певні
значення електропровідності. В свою чергу, електропровідність консерваційних
олив залежить від вмісту сполук, що мають у своїй структурі групи з високим
значенням дипольного моменту.
При застосуванні консерваційної
оливи в умовах низьких температур, остання повинна мати низьке значення
температури застигання. Крім того для забезпечення високої захисної здатності
плівка такої консерваційної оливи повинна бути морозостійкою.
Морозостійкість консерваційної
оливи – як здатність зберігати цілісну захисну плівку під час, і після дії
низьких температур визначається хімічним складом оливи.
Консерваційна олива, що
застосовується в умовах низьких температур (в разі застигання) повинна
утворювати еластичні напівтверді плівки. Адже при утворенні крихких, за
низьких температур, плівок або таких, що містять пори, виникає можливість
корозійного враження поверхні металовиробу [19].
Термостабільність - стійкість до
руйнування захисної плівки консерваційної оливи на поверхні металу під дією
високих температур, в наслідок стікання або теплової десорбції інгібітору.
Термостабільність має значення при використанні консерваційної оливи в умов
підвищених температур. Дана властивість консерваційних олив може регулюватись
зміною в’язкості оливи або застосуванням ефективних інгібіторів корозії
хемосорбційного типу [19].
За нормальних умов консерваційні
оливи стійкі до дії кисню повітря. Але, підвищена температура, високе значення
питомої поверхні контакту з повітрям, а також наявність металевої поверхні
сприяють проходженню процесів окиснення плівки консерваційної олив, в
результаті чого, на поверхні металовиробів, можуть утворюватись корозійно
активні агенти (кислоти, вода та ін) або полімери які ускладнюють процес
розконсервації. Тому консерваційні оливи повинні мати певну стійкість до
окиснення.
Порівняно високу стійкість до
окиснення також повинні мати оливи, що застосовуються в умовах підвищених
температур з ефективною аерацією (на відкритих майданчиках і ін.).
Для поліпшення антиокисних
властивостей олив, в залежності від умов застосування, до їх складу додають
спеціальні антиокисні оливорозчинні додатки: іонол, борин, діалкілдітіофосфати,
діфеніламін і ін. [14-16, 185, 186]
Вологостійкість- властивість консерваційної оливи
утворювати на поверхні металу захисну плівку, що неруйнується під дією вологи.
Вологостійкість консерваційної оливи може бути покращена застосуванням
ефективних, стійких до гідролізу інгібіторів корозії.
Біостійкість- властивість консерваційних олив
утворювати на поверхні металу захисні плівки стійкі до ураження
мікроорганізмами. Питання біостійкості консерваційної оливи має місце за умов,
що сприяють розмноженню мікроорганізмів. На біостійкість консерваційної оливи
перш за все впливає її хімічний склад. Підвищити біостійкість консерваційної
оливи можна шляхом підбору біостійких компонентів [187-190] або введенням
біостатичних та біоцидних препаратів: альдегідів, амінів, органічних та
неорганічних боратів, тріазину, органометалічних сполук, ізотіазолідин-3-онів,
оксозолідину, похідних морфоліну, піридину, гуанідину та ін. [189-193].
Важливою
характеристикою консерваційної оливи є адгезія до металевої поверхні[19].
Адгезія до металевої поверхні– визначається як енергія відриву оливи від
металевої поверхні. Однак, чи корелюється значення адгезії оливи до металу з її
захисною здатністю є спірним питанням [194].
Таким
чином консерваційні оливи, окрім оливорозчинних інгібіторів корозії можуть
містити: загущуючі, протизносні, миючі, антипінні, адгезійні, біостатичні та
ін. додатки.
Захисна здатність та більшість функціональних властивостей
консерваційних олив комплексно залежать від усіх оливорозчинних додатків які входять
до її складу. Характер та рівень взаємного впливу додатків на властивості консерваційних олив визначається їх
хімічним складом. Для застосування нових інгібіторів корозії, створених на
основі похідних карбаміду, в розробці консерваційних олив, необхідно дослідити
та враховувати вплив інших компонентів оливи на її основні властивості.
3. ОБ¢ЄКТИ ТА
МЕТОДИ ДОСЛІДЖЕННЬ
3.1. Об¢єкти
досліджень.
Обєктами дослідження даної роботи були: товарні
оливорозчинні інгібітори корозії та консерваційні оливи вітчизняного і
зарубіжного виробництва, а також сировина для створення консерваційних олив, в
тому числі нафтові оливи та реагенти для розробки інгібіторів корозії.
Товарні
консерваційні оливи та оливорозчинні інгібітори корозії в даній роботі
виступали в якості обєктів порівняння. Серед консерваційних олив було обрано:
К-17 (ГОСТ 10877-76) ОКС (ТУ У23.2-13810574-004-2002 (ТОВ “Кальві”, Україна),
ЖКС-40 (ВАТ “АЗМОЛ”, Україна), Автокон-ЛС, (ЗАО "АВТОКОНИНВЕСТ",
Росия), Волгол-131 (ООО “ВПО “Волгохимнефть” м. Волгоград, Росия) Antikorit RP4107,
(Виробник компания “FUCHS”) Antikorit
6120/42Е, (Виробник компания “FUCHS”), Саstrol, safecoat 66, (Виробник
компания “Саstrol”), Shell Ensis Oil N
(Компания “Shell”). Характеристики перерахованих
консерваційних олив приводяться у таблицях 3.1, 3.2.
Таблиця 3.1
Характеристики зарубіжних консерваційних
олив.
Показник |
Значення показника |
Метод випробування |
Antikorit 6220/42 Е |
Antikorit RP4107А |
Rustilo 650 |
Саstrol safecoat
66 |
Shell
Ensis
Oil N |
Зовнішній
вигляд |
Оливиста рідина жовтого кольору |
Оливиста рідина жовтого кольору |
Оливиста рідина жовтого кольору |
Оливиста рідина жовтого кольору |
Оливиста
рідина |
Візуально |
В'язкість
кінематична, мм2/с: -при 50 °С |
15,92 |
16,0 |
32,5 |
5-8 |
17 |
ГОСТ
33 |
Лужне
число, мг КОН/г |
8 |
9,0 |
2,81 |
5 |
0,28 |
ГОСТ
11362 |
Кислотне
число, мг КОН/г |
0,33 |
0,3 |
0,56 |
0,7 |
1,12 |
ГОСТ
11362 |
Густина
при 20 °С, кг/м3 |
865 |
873 |
885 |
874 |
875 |
ГОСТ
3900 |
Температура
застигання, °С ,
не нижче |
-18 |
-18 |
— |
— |
-18 |
ГОСТ
20287 |
Температура спалаху, визначена у відкритому тиглі, оС |
154 |
152 |
215 |
147 |
207 |
ГОСТ
4333 |
Таблиця 3.2
Показник |
Значення показника |
Метод випробування |
К-17 |
ОКС-2 |
ЖКС-40 |
Автокон-ЛС |
Волгол-131 |
Зовнішній
вигляд |
В'язка
оливиста рідина
коричневого кольору |
Оливиста рідина коричневого кольору |
В'язка
оливиста рідина |
Рідина
жовтого кольору |
Рідина
жовтого кольору |
Візуально |
В'язкість
кінематична, мм2/с -при 50 °С |
18.2 |
21,2 |
43,5 |
20,5 |
20,5 |
ГОСТ
33 |
Лужне
число, мг КОН/г |
9,3 |
3,3 |
0,05 |
13,46 |
41,23 |
ГОСТ
11362 |
Кислотне
число, мг КОН/г |
1,7 |
10,6 |
1,07 |
4,77 |
1,4 |
ГОСТ
11362 |
Густина
при 20 °С, кг/м3 |
884 |
920 |
890 |
875 |
908 |
ГОСТ
3900 |
Температура
застигання, °С , |
-28 |
-18 |
-20 |
-34 |
— |
ГОСТ
20287 |
Температура спалаху, визначена у відкритому тиглі, оС |
184 |
141 |
195 |
164 |
187 |
ГОСТ
4333 |
Характеристики консерваційних олив вітчизняних
виробників та виробників РФ.
Серед
оливорозчинних інгібіторів корозії, як об¢єкти порівняння
були обрані:
КП-2
(Пермский завод смазок и СОЖ) , Daskogard – 233, Daskogard – 60 (виробництво компанії Stuart),
Концентрат інгібіруючий ОКС (виробництво ТОВ Кальві, м. Львів), Телаз–ЛС ( ТОВ
«Автокон», м. Москва, Росія ), СИМ-1 (ТУ 38.1011039-85), В 15/41 (ТУ
6-14-866-77).
Одними
з найефективніших інгібіторами корозії, є похідні біциклогексиламіну. Тому в
якості порівняльного стандарту було взято, присадку МСДА–11 (ТУ 6-02-834-88),
– сіль СЖК (С10-12) і біциклогексиламіну, що на даний час знята з
виробництва через високу токсичність [181, 195-199].
Характеристики
оливорозчинних інгібіторів корозії приводяться у таблицях 3.3, 3.4.
Таблиця 3.3
Характеристики
оливорозчинних інгібіторів корозії.
Показник |
Значення показника |
Метод випробування |
КП-2 |
Dascogard- 60 |
Dascogard-233 |
Зовнішній
вигляд |
В’язка
речовина чорного кольору |
Пастоподібна
речовина жовтого кольору |
Пастоподібна
речовина жовтого кольору |
Візуально |
В'язкість
кінематична, при 50 °С , мм2/с |
16,0* |
12,8 |
111,6 |
ГОСТ 33-82 |
Лужне
число, мг КОН/г |
— |
2,81 |
— |
ГОСТ 11362-76 |
Кислотне
число, мг КОН/г |
65 |
0,56 |
— |
ГОСТ 11362-76
DIN 51558-2 |
Густина
при 20 °С, кг/м3 |
900 |
910 |
946 |
ГОСТ 3900-85
DIN 51757 |
Температура
застигання, °С , |
-10 |
5 |
— |
ГОСТ
20287 |
Вміст
води, % |
0,03 |
0,03 |
0,03 |
ГОСТ 2477-65 |
Температура спалаху, у відкритому тиглі, оС, |
151 |
119 |
167 |
ГОСТ 4333- 87
DIN ISO 2592 |
*В'язкість кінематична, при 100 °С
Таблиця 3.4
Характеристики
оливорозчинних інгібіторів корозії.
Показник |
Значення показника |
Метод випробування |
Телаз
–ЛС |
Концентрат інгібіруючи й ОКС |
МСДА-11 |
Зовнішній
вигляд |
Оливиста рідина |
Рідина коричневого кольору |
Мазе
подібна речовина
50%
р-н |
Візуально |
В'язкість
кінематична, при 50 °С, мм2/с |
— |
25-40 |
159 |
ГОСТ 33-82 |
Лужне
число, мг КОН/г |
55,2 |
— |
62,5 |
ГОСТ 11362-76 |
Кислотне
число, мг КОН/г |
21,5 |
10-30 |
67,2 |
ГОСТ 11362-76 |
Густина
при 20 °С, кг/м3 |
905 |
900-970 |
951 |
ГОСТ 3900-85 |
Температура
застигання, °С |
-18 |
— |
-10 |
ГОСТ
20287 |
Вміст
води, % |
0,5 |
0,03 |
0,03 |
ГОСТ 2477-65 |
Температура спалаху, у відкритому тиглі, оС, |
162 |
145 |
208 |
ГОСТ
4333- 87 |
Об’єктом дослідження обрано карбамід, який є одним з найбільш
доступних на Українському ринку реагентів.
Карбамід у великих кількостях виробляється на черкаському підприємстві ВАТ
“АЗОТ”, северодонецькому ЗАО “АЗОТ”, днепродзержинському
ОАО “ДнепрАзот”, одеському ООО “Одеський припортовий завод”, горлівському підприємстві ОАО “Стирол”.
Фізикохімічні
властивості хімічно чистого карбаміду наведені в таблиці 3.5.
Таблиця
3.5
Фізикохімічні
властивості хімічно чистого карбаміду.
№ |
Показник |
Значення показника |
1 |
Зовнішній вигляд |
безкольорові
кристали |
1 |
Температура плавлення, оС |
132,7 |
2 |
Молекулярна маса |
60,06 |
3 |
Густина, кг/м3 |
1330 |
4 |
Теплопровідність, Дж/(моль*К) |
93,198 |
5 |
Енергія утворення, кДж/моль |
– 197,3 |
6 |
Ентальпія згоряння, кДж/моль |
– 632,5 |
7 |
Розчинність у 100г води при 20оС,
г
при 60оС, г |
51,8
71,7 |
8 |
Розчинність у 100г метанолу при
20оС, г |
22 |
9 |
Розчинність у 100г етанолу при
20оС, г |
5,4 |
10 |
Розчинність у 100г ізопропанолу
при 20оС, г |
2,6 |
В
даній роботі для досліджень було взято карбамід марки Б, характеристики якого
відповідали ГОСТ 2081 (Таблиця 3.6).
Таблиця 3.6
Характеристики
карбаміду (марка Б), ГОСТ 2081
№ |
Показник |
Значення показника |
1 |
Масова
доля азоту, % |
46,2 |
1 |
Масова доля біурету, % |
0,9 |
2 |
Масова доля
вільного аміаку, % |
0,06 |
3 |
Масова доля води (метод Фишера) |
0,5 |
4 |
Густина, кг/м3 |
1330 |
В основі технологій одержання
інгібіторів корозії (ІК) на основі похідних карбаміду лежать реакції
амідування. В якості ацилюючого реагенту було обрано олеїнову та стеаринову
кислоти, що у великих кількостях виробляються вітчизняними
підприємствами з рослинних олій.
Для досліджень було
взято чисту олеїнову кислоту виробництва компанії Sagusa, ІЧ спетр якої наведено на рис 2, а якісні
характеристики наведені у Таблиці 3.5.
Рис. 2 ІЧ-спектр чистої олеїнової кислоти
Таблиця
3.5
Характеристики чистої олеїнової кислоти.
№ |
Показник |
Значення показника |
1 |
Кислотне число,
мгКОН/г |
198,2 |
2 |
Число омилення, мгКОН/г |
202 |
3 |
Йодне число, г І2/100
г |
98,6 |
4 |
Колір по
Ловібонду 5 1/4R
5 1/4Y |
3.5
30 |
5 |
Вміст води, % |
0,1 |
6 |
Вміст речовин, що
неомілюються, % |
0,82 |
У виробництві економічно
доцільним є використання технічної сировини.
Тому для досліджень також було
взято технічну олеїнову кислоту
ТУ 10-04-02-82-91марки Б (Таблиця
3.6), яка в залежності від сировини, з якої була отримана, може мати різний
хімічний склад Таблиця 3.7.
Таблиця 3.6
Характеристики технічної олеїнової кислоти, марки Б
№ |
Показник |
Значення показника |
1 |
Зовнішній вигляд |
легкозастигаюча маса світло жовтого або коричневого
кольору |
2 |
Запах |
Специфічний не подразнюючий |
3 |
Масова доля жирних кислот у безводному продукті, % |
99 |
4 |
Масова доля золи, % |
0,1 |
5 |
Кислотне число, мгКОН/г |
188,2 |
6 |
Число омилення, мгКОН/г |
202 |
7 |
Йодне число, г І2/100 г |
105 |
8 |
Вміст
води, % |
0,5-2 |
9 |
Вміст речовин, що неомілюються, % |
2,4 |
10 |
Температура застигання, о С |
14 |
Основним
домішком до технічної олеїнової кислоти, яку одержують з рослинної сировини, є
стеаринова кислота CH3(CH2)16COOH.
В
залежності від сировини, а також технології одержання олеїнової кислоти до її
складу може входити від 1 до 45 % стеарину. Враховуючи те, що фізикохмічні
властивості похідних олеїнової та стеаринової кислот є різними, вміст останньої
може впливати на основні властивості ОІК.
Тому,
для досліджень було взято стеаринову кислоту якісні характеристики якої
відповідають ГОСТ 9419-78 (Таблиця 3.8.)
Таблиця
3.8
Фізикохімічні показники стеаринової кислоти.
№ |
Показник |
Значення показника |
1 |
Масова
частка стеаринової к-ти, % |
98,2 |
2 |
Кислотне число, мгКОН/г |
198,0 |
3 |
Залишок після прокалювання, % |
0,12 |
4 |
Число омилення, мгКОН/г |
202 |
5 |
Температура плавлення, оС |
69,6 |
6 |
Вміст речовин, що неомілюються, % |
0,82 |
З метою отримання естерів, було
взято триетаноламін (TEA) кваліфікації «чистий» характеристики
якого відповідають ТУ 2423-061-05807977-2002 і наведені у таблиці 3.9.
Таблиця
3.9
Характеристики технічного триетаноламіну
№ |
Показник |
Значення показника |
1 |
Зовнішній вигляд |
Прозора рідина |
2 |
Точка кипіння оС |
310 |
3 |
Точка застигання оС |
- 21,2 |
4 |
Точка замання оС |
194,4 |
5 |
Специфічна густина, при 20 оС |
1,126 |
6 |
Тиск пари |
1:4,9 |
7 |
Розчинність у воді, (% ваг.) |
повна |
8 |
Показник заломлення |
1,4852 |
9 |
Вміст води, % |
0,2 |
|
Вміст етаноламінів, % |
10 |
моноетаноламіну |
0,5 |
11 |
диетаноламіну |
11 |
12 |
триетаноламіну |
85 |
Триетаноламін як
реагент, що був використаний в даній роботі містить 85% триетаноламіну, 11%
діетаноламіну та 0,5% моноетаноламіну. Характеристики етаноламінів наведено в
таблиці 3.10
Таблиця
3.10
Характеристики етаноламінів
Показник |
Значення показника |
моноетаноламін |
діетаноламін |
триетаноламін |
Мол. маса |
61,08 |
105,14 |
149,19 |
Т.пл., °С |
10,6 |
27,8 |
21,2 |
Т.кип., °С |
170-171 |
270 |
360 |
d4 20 |
1,0159 |
1,0966 |
1,1242 |
nD20 |
1,4541 |
1,4776 |
1,4852 |
η, мПа.с (25°С) |
19 |
580 |
601 |
Розчинність г.
у 100г .
гептана (25°С) |
0,6 |
0,1 |
0,2 |
Т.спалаху °С |
93 |
148,9 |
179 |
Т.займання |
450 |
- |
- |
ПДК6, мг/г |
1 |
5 |
5 |
В даній роботі для дослідження
були вибрані оливи індустріальні, дистилятні, селективної очистки
І-5А...І-50А (ГОСТ 20799-75) які одержують із малосірчистих і сірчистих нафт.
Фізикохімічні властивості та
вуглеводневий склад нафтових дистилятних базових олив приводятся в таблицях 3.8, 3.9.
Таблиця
3.8
Фізикохімічні
властивості та вуглеводневий склад базових олив індустріальної групи
Олива
Показники |
І-5А |
І-8А |
І-12А |
І-20А |
І-20А |
І-30А |
І-40А |
І-50А |
В'язкість, мм2/c, при 50 оС, |
4,19 |
7,21 |
12,6 |
22,24 |
20,4 |
31,5 |
42 |
47,8 |
Густина, кг/м3, при 20 оС, |
880 |
896 |
903 |
878 |
875 |
882 |
887 |
893 |
Показник заломлення, при 20 оС, |
1,491 |
1,493 |
1,501 |
1,486 |
1,48 |
1,487 |
1,49 |
1,506 |
Кислотне число, мгKOH/г |
0,031 |
0,028 |
0,045 |
0,033 |
0,02 |
0,042 |
0,04 |
0,032 |
Температура спалаху, визачена у відкритому тиглі, оС. |
142 |
154 |
176 |
202 |
196 |
200 |
215 |
228 |
Температура застигання, оС. |
-25 |
-22 |
-23 |
-18 |
-18 |
-18 |
-18 |
-20 |
Вміст сірки, % мас. |
0,04 |
0,018 |
0,012 |
0,015 |
0,01 |
0,04 |
0,06 |
0,08 |
Груповий вуглеводневий склад, % мас. |
Парафіно-нафтенові вуглеводні |
66,5 |
71,4 |
65,2 |
72,1 |
86,6 |
69,3 |
69,5 |
67,21 |
Ароматичні вуглеводні в тому числі, % |
І-групи |
13,1 |
9,7 |
8,9 |
9,9 |
9,5 |
13,4 |
14,5 |
16,1 |
ІІ-групи |
7,0 |
7,1 |
6,9 |
6,3 |
2,3 |
6,8 |
7,1 |
7,29 |
ІІІ-групи |
7,3 |
6,8 |
6,9 |
11,0 |
1,5 |
9,2 |
8,2 |
7,58 |
ІV-групи |
5,4 |
4,3 |
11,4 |
0 |
0 |
0,7 |
0 |
0 |
Смоли |
0,7 |
0,7 |
0,7 |
0,7 |
0,1 |
0,6 |
0,7 |
0,7 |
|
|
|
|
|
|
|
|
|
|
|
Також досліджувались олива ЄСО -
екстракт нафтовий (ТУ 38101714-84), (одержують фенольною очисткою дистилятних і
залишкових масляних фракцій), олива технологічна марки А, олива І-20
індустріальна, регенерована (РНПК) та оливи серії ОР (Львівського НПЗ),
фізикохімічні властивості яких наведені таблиці 3.9. Ці оливи мають високий
вміст ароматичних вуглеводнів і смол, що може вплинути на захисні властивості
захисних засобів на їх основі.
Таблиця
3.9
Фізикохімічні властивості базових
олив, серії ОР (Львівського НПЗ), регенерованої оливи І-20, ЕСО, технологічної
оливи марки А (РНПК).
Олива
Показники |
ОР-1 |
ОР-2 |
ОР-3 |
І-20
Регенероване |
ЕСО |
Технологічна олива марки А |
Зовнішній
вигляд |
В¢язка рідина чорного кольору |
Оливиста
рідина чорного кольору |
В¢язка рідина чорного кольору |
Темно червоний |
В¢язка рідина чорного кольору |
В¢язка рідина чорного кольору |
Запах |
Слабкий |
Слабкий |
Специфічний, |
Слабкий |
Специфічний,
неприемній |
Специфічний |
В'язкість, мм2/c, при 50 оС, |
11,5 |
24,5 |
243 |
19,5 |
124 |
20,5 |
Густина, кг/м3, при 20 оС, |
880 |
896 |
903 |
920 |
952 |
900 |
Показник заломлення, при 20 оС, |
1,42 |
1,7 |
1,63 |
1,49 |
1,511 |
1,48 |
Кислотне число, мгKOH/г |
0,05 |
0,06 |
0,08 |
0,095 |
0,1 |
0,08 |
Температура спалаху, визачена у відкритому тиглі, оС. |
165 |
195 |
250 |
205 |
224 |
180 |
Температура застигання, оС. |
-22 |
-18 |
-18 |
-18 |
- |
-19 |
Вміст сірки, % мас. |
0,5 |
0,55 |
0,6 |
0,1 |
2,7 |
- |
Груповий вуглеводневий склад, % мас. |
Парафіно-нафтенові вуглеводні |
73,3 |
70,8 |
51,9 |
61,8 |
14,2 |
70,8 |
Ароматичні вуглеводні в тому числі, % |
|
І-групи |
6,4 |
8,7
|
14,2 |
18,3 |
26,2 |
16,9 |
ІІ-групи |
12,3 |
11,3
|
8,7 |
13,9 |
12,2 |
2,6 |
ІІІ-групи |
6,3 |
0,7
|
14,2 |
4,3 |
17,3 |
8,2 |
ІV-групи |
- |
-
|
4,9 |
0,6 |
26,2 |
- |
Смоли |
1,5 |
1,0
|
5,5 |
1,1 |
3,9 |
1,5 |
|
|
|
|
|
|
|
|
|
Захисна ефективність
консерваційних олив залежить від наявності антагоністичних та сінергетичних
ефектів в суміші присадок з різними функціональними групами. Так, неаддитивно
підвищену захисну ефективність (синергетичний ефект) проявляють оливи, що
містять у своєму складі присадки що здатні по відношенню до металевої поверхні
проявляти акцепторні та донорні електронні ефекти [14-16]. Азотвмісні
інгібітори корозії (аміни, аміди, солі амінів і ін), сорбуючись на металах, як
правило проявляють електроноакцепторний ефект. До інгібіторів корозії, що
адсорбуються з донорним ефектом відносяться алкілнітросполуки, органічні
сульфати та сульфонали [14-16]..
В даній роботі для встановлення синергетичних
ефектів досліджували зольний оливорозчинний додаток сульфонатного типу: С-150 характеристики
якого наведено у таблиці 3.10.
Таблиця. 3.10
Фізикохімічні властивості оливорозчинного додатку
С-150
№ |
Найменування
показника |
Значення
показника |
Метод
випробування |
1 |
В'язкість, мм2/c, при 100 оС, |
65 |
ГОСТ
33 |
2 |
Загальна
лужність, мгКОН/г |
138 |
ГОСТ
11362 |
3 |
Масова частка сульфонату кальцію, % |
28 |
По
п. 5.2, 5.3 ТУ 38.101685- 84 |
4 |
Масова частка механічних домішок, % |
0,1 |
ГОСТ
3670 |
5 |
Масова частка води, % |
0,2 |
ГОСТ
2477-65 |
6 |
Температура спалаху, визачена у відкритому тиглі, оС. |
180 |
ГОСТ
4333 |
7 |
Ступінь
чистоти, мг на 100 г додатку |
5000 |
ГОСТ
12275 |
8 |
Зольність
сульфатна, % |
21 |
ГОСТ
12417 |
9 |
Розчинність
в оливі І-20А і М-11 (ГОСТ 20799 і ТУ 38101523-80) |
Повна |
По
п. 5.5 ТУ 38.101685 - 84 |
В якості матеріалів відносно яких
визначалась захисна здатність ЗТЗМ були обрані:
1)
штамповочні сталі звичайної якості 08пс, 08кп, (ГОСТ 380-94 Сталь
углеродистая обикновенного качества),
2)
літьйові сталі Ст10, Ст40,
3)
сірий чавун СЧ 18 (ГОСТ 1412-85 Чугун с пластинчатым графитом для
відливок).
4)
сталь підшипникова - Шх15 (ГОСТ 801-78 Сталь подшипниковая. Технические
условия).
Хімічний склад цих
матеріалів наведено у таблиці 3.11.
Таблиця
3.11
Хімічний склад матеріалів відносно яких визначалась
захисна здатність ЗТЗМ
Марка матеріалу |
Масовая доля елементів, % |
Вуглецю |
Марганецю |
Кремнію |
Хром |
Нікелю |
Міді |
Фосфору |
Сірки |
Не більше |
Ст08кп |
0,06-0,12 |
0,25-0,50 |
0,05 |
0,1 |
0,3 |
0,3 |
0,035 |
0,04 |
Cт08пc |
0,06-0,12 |
0,25-0,50 |
0,05-0,15 |
0,1 |
0,3 |
0,3 |
0,035 |
0,04 |
ШХ15 |
0,95 - 1 ,05 |
0,20 - 0,4 |
0,17-0,37 |
1,30-1,65 |
0,3 |
0,25 |
0,027 |
0 ,02 |
СЧ
18 |
3,3 - 3,5 |
0,7 - 1,0 |
1,4 - 2,4 |
- |
- |
- |
0,2 |
0,15 |
Ст10 |
0,07-0,14 |
0,35-0,65 |
0,17-0,370 |
0,15 |
0,3 |
0,3 |
0,035 |
0,04 |
Ст40 |
0,37-0,45 |
0,50-0,80 |
0,17-0,37 |
0,25 |
0,3 |
0,3 |
0,035 |
0,04 |
3.2. Методи досліджень
В роботі було використано стандартні та
нестандартні методи досліджень. Стандартні методи досліджень наведені в
таблиці 3.12
Таблиця 3.12
Стандартні методи дослідженнь
№ |
Назва
показника
|
Стандарт, назва методу |
1 |
Захисна
здатність
|
ГОСТ 9.054
Метод
ускоренных испытаний защитной способности |
2 |
Густина
|
ГОСТ 3900
Метод
определения плотности |
3 |
Кінематична
В'язкість
|
ГОСТ 33
Метод
определения кинематической вязкости |
4 |
Температура
спалаху, у відкритому тиглі
|
ГОСТ 4333
Метод
определения температуры вспышки и воспламенения в открытом тигле |
5 |
Зола
сульфатна
|
ГОСТ 12417
Метод
определения сульфатной золы |
6 |
Лужне
число
|
ГОСТ 11362
Число нейтрализации.
Метод потенциометрического титрования |
7 |
Кислотне
число
|
ГОСТ 11362
Число нейтрализации.
Метод потенциометрического титрования |
8 |
Температура
крапання
|
ГОСТ 6793
Метод
определения температуры каплепадения |
9 |
Йодне
число
|
ГОСТ 2070
Метод
определения йодных чисел и содержания непредельных углеводородов |
10 |
Число
омилення
|
ГОСТ 17362
Метод
определения числа омыления |
11 |
Вміст
води
|
ГОСТ 2477
Метод определения содержания воды |
Захисну здатність консерваційних
олив визначали за стандартною методиками згідно ГОСТ 9.054.
Метод №1 (при підвищеному
значенні відносної вологості і температури повітря без конденсації з
періодичною або постійною конденсацією вологи )
Висушені знежирювали в бензині та
спирті металеві пластинки обробляли консерваційним матеріалом при температурі
20-25 оС та підвішували в камері у вертикальному положенні.
Випробування проводили циклічно з конденсацією вологи через 7 годин. Через
встановлений час випробувань фіксували площу поверхні пластин, що була вражена
корозією.
Метод №2, (випробування захисної
здатності засобів тимчасового захисту металовиробів в умовах підвищених значень
відносної вологості та температури повітря при дії сирчистого ангідриду)
В ексикатор об’ємом 5 л. поміщали 400 мл води, в центрі розміщували фарфорову емність, що містила 5 мл концентрованої
сірчаної кислоти. Після розташування в ексикаторі підготованих зразків
металевих пластин, у сірчану кислоту поміщали сульфіт натрію з таким
розрахунком, щоб концентрація сірчистого ангідриду, який виділяється за
реакцією Na2SO3+ 2H2SO4 = 2NaHSO4 + SO2 + H2O , в об’ємі ексикатора складала
0,015-0,02%. Через встановлений час випробувань фіксували площу поверхні
пластин, що була вражена корозією.
Метод №3, (випробування захисної
здатності засобів тимчасового захисту металовиробів в умовах камери сольового
туману).
Суть методу №3 полягає у витримці
пластин з консерваційним матеріалом у атмосфері соляного туману при температурі
35 + 2 о С.
Камера сольового туману
представляє собою скляну циліндричну ємність на дні якої знаходиться 5 %- вий
розчин NaCl. На віддстані 8 см. над розчином розміщуєтся базова випробувальна полиця. У результаті багаторазових випробувань
було встановлено, що швидкість корозії пластин суттєво залежить від кута нахилу
кородуючої поверхні до горизонту. Тому, для підвищення сходимості результатів,
був сконструйований спеціальний каркас за допомогою якого, при проведенні
випробувань пластин, чітко фіксувався кут нахилу кородуючої поверхні, рівний 45о.
В розчин електроліту занурений барбатер – вигнутий скляний фільтр Шотта.
Ємність обладнується неметалічною кришкою. Барбатер, за допомогою гумового
патрубку, через передбачений у кришці отвір з¢єднано
з компресором.
Після розміщення у камері
зразків, остання розміщається у термостаті при робочій температурі 39+2 оС. Сольовий туман
створюється барбатуванням через фільтр повітря. Результати випробувань
знімались візуально за допомогою проградуйованої рамки.
Метод №4 (Визначення захисної
здатності оливи в умовах електроліту).
Випробування консерваційого
матеріалу нанесеного на металеві пластини витримкою у електроліті проводили за
допомогою спеціально виготовленої комірки рис.
Комірка для витримки пластин у
розчині електроліту була виготовлена таким чином, що об¢єм електроліту використовувався максимально ефективно. Це
в свою чергу давало змогу економно витрачати реактиви, що входять до складу
електроліту, дотримуючись при цьому ГОСТ 9.054-75.
Враховуючи вимоги ГОСТ 9.054-75,
матеріал, що контактує з електролітом не містить метал. Беручи до уваги потребу
відслідковувати корозійні процеси у часі, матеріалом фронтових стінок (1)
комірки слугувало прозоре органічне скло. Для зручності закріплення пластин з
нанесенним консерваційним матеріалом, комірка була обладнана двома несущими
рамками (2), що закріплювались у пазах стінок. Кожна несуща рамка має
оптимально розміщені пази для спеціальних зажимів (3). Затискачи, що
використовувались в даній конструкції були виконані з пластмаси, що також не
перечить вимогам ГОСТ 9.054-75. Таким чином при проведенні випробувань в
середовищі електроліту, за допомогою виготовленої комірки, металеві пластини не
обов¢язково повинні мати отвори
для підвішування. А відомо, що виготовлення отворів призводить до деформації
структури металу, утворення неоднорідностей і ін [14, 15]. Що в свою чергу
дестабілізує умови дослідженнь захисних властивостей інгібованих матеріалів і
впливає на сходимість результатів експерименту.
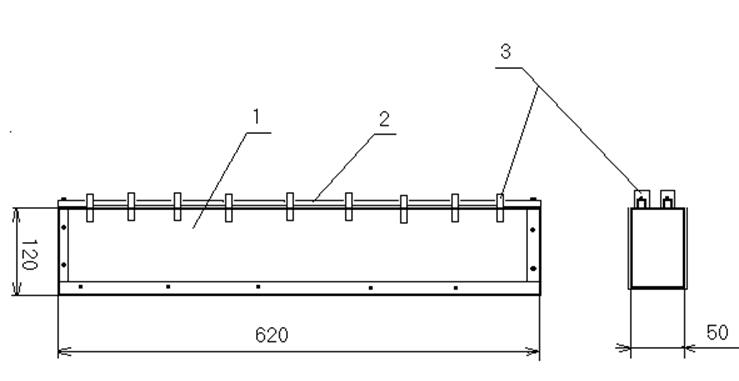
Схема
3.1. Комірка для випробувань консерваційних
засобів в умовах електроліту.
Визначення захисної здатності
консерваційних матеріалів, відбувалось наступним чином:
На основі дистильованої води
готували електроліт, рецептура якого приведена у таблиці 3.6.
Таблиця
3.6
Склад електроліту
Найменування солі |
Концентрація г/л |
Магній хлористий ГОСТ
4209-77 |
11 |
Кальцій хлористий ГОСТ
4161-77 |
1,2 |
Натрій сірчанокислий ГОСТ
4171-76 |
4,0 |
Натрій хлористий ГОСТ
4233-77 |
25,0 |
Готували 25%-вий розчин
вуглекислого натрію в дистильованій воді за допомогою якого встановлювали рН
електроліту в межі 8,0-8,2.
За допомогою лапки до штатива
прикріплювали несущу рамку комірки з закріпленими на ній зажимами.
Металеві пластинки зачищали наждачним
папером до шероховатості в межах 1,25-0,6 мкм. відповідно до ГОСТ 2789-73.
Після послідовного знежирювання бензином та спиртом пластинки висушували.
Не торкаючись руками
поверхні, маркером або за допомогою бірок, проводили маркування пластинок.
Знежирені маркеровані пластини вертикально закріплялись у пластмасових
затискачах на підготовленій несущій рамці.
Одну пластину, для порівняння,
при отриманні результатів, поміщали у ексікатор.
Кожну з закріплених пластин, при
температурі 20-25 оС, на 1 хв. занурювали у відповідний
консерваційний засіб, реєстр якого відповідав номеру пластини за робочим
журналом. Після нанесення консервуючого засобу пластинки витримували на повітрі
у вертикальному положенні на протязі 1 години. За цей час комірку заповнювали
приготованим електролітом.
Несуща рамка з прикріпленими
пластинами приєднувалась до комірки з електролітом (за допомогою пазів).
Фіксували час початку експерименту.
За результатами експерименту
визначали час до появи корозії, або з допомогою прозорого трафарету
встановлювали відсоток прокородувавшої площи поверхні пластин за встановлений
час перебування пластин у електроліті.
Якщо втрати маси металу в ході
експерименту суттєві (як наприклад для неінгібованих олив), то захисні
властивості покриттів уточнювали гравіметрично. Для цього на початку і після
випробувань пластинка зважувалась на аналітичних терезах з точністтю до 0,0002
грам. Корзійні втрати вимірювались у г/м2 і розраховувались за
формулою:
Де m1, m2 - маса пластинки
відповідно на початку та у кінці експерименту (гр) ;
L, N - лінійні розміри пластинки у см.;
В умовах деяких виробництв,
поверхню деталей перед консервацією не піддають спеціальному осушуванню, що
може призвести до появи корозії під шаром консерванту, у випадку якщо останній
не має здатності ефективно витісняти наявну на металевій поверхні вологу.
Виходячи з цього захисний засіб повинен володіти “швидким водовідштовхуючим
ефектом”, або властивістю витісняти з поверхні металу електроліт. [200 ]
Метод 5 (здатність оливи
виштовхувати бромводневу кислоту з поверхні металу )
За даним методом готували 200 см3 0,1%
розчину бром водневої кислоти. Знежирені та висушені пластинки Ст10 послідовно
занурювали в розчин кислоти (з витримкою не більше 1 с.) та 12 раз (на протязі
1 хв) у консерваційну оливу. Пластинки витримували на повітрі протягом 4 годин
після чого промівали толуолом та фіксували ступінь корозійного враження
поверхні.
Водовиштовхуюча дія
Для визначення водовиштовхуючої
здатності консерваційних олив користувались нестандартною методикою [200]:
На зачищений, знежирений диск із
Ст10 рівномірно наносили 1 мл. дистильованої води, в центр змоченої поверхні
вносили краплину консерваційної оливи, що досліджувалась. Заміряли діаметр (мм)
води, що була витіснена.
Визначення взаємодії
інгібітора з водою (гідролітична стабільність).
Схильність до гідролізу
амідоестерного інгібітору досліджували за наступною методикою:
До 90 грам дистильованої води
додавали 10 грам інгібітора, суміш ретельно перемішували та термостатували при
температурі 20 оС. Через встановлений час відбирали проби водної
витяжки для яких визначали значення рН. За зміною рН робили висновок щодо
схильності інгібітору до гідролізу.
Методика визначення адгезії
сил адгезії оливи до металевої поверхні
Адгезія до металу певним чином
корелюється з захисними властивостями консерваційних олив. Величину, що
пропорційна адгезії визначали методом центрифугування. Зачищені, промиті
бензином та спиртом пластини Ст08пс зважували на аналітичних вагах з точністтю
до 0,2 мг, та вносили в консерваційний засіб. Після чого оливі, давали зтекти з
пластин до стабілізації маси та знову зважували. Пластини центрифугували
протягом 10 хв. при швидкості 8000 об/хв та знову зважували. Різниця маси приведена
до площі нанесення пропорційна силі адгезії оливи до металу.
Характер взаємодії інгібітору з
металевою поверхнею, визначали шляхом встановлення ефекту післядії [14].
Методика дослідження взаємодії
інгібітора з металевою поверхнею.
Природу взаємодії інгібітора
МІК-8 з поверхнею металу (Ст08пс) визначення шляхом встановлювлення ефекту
післядії. На три, зачищені та знежирені пластини Ст08пс було нанесили
досліджуваний інгібітор. Паралельно, для порівняння, було підготовлено пластини
з нанесеним інгібітором КП-2, який гарантовано взаємодіє з поверхнею металу за
хемосорбційним механізмом і володіє ефектом післядії. Пластини було витримано
протягом 1 доби при кімнатній температурі після чого проводили змивання
інгібітора теплим (40оС) розчинником (суміш рівних масових
кількостей ізопропанолу та толуолу). Змивання проводили до відсутності залишку
на готинниковому скельці після випаровування порції розчинника. Оброблені таким
чином пластини піддавали корозійному впливу електроліта протягом 5 діб відповідно
до ГОСТ 9.054 (метод 4). В ході випробуваннь визначали площу пластин вражену
корозією.
3.3 Методика синтезу ІК
Технологія процесів естерифікації та амідування,
робить можливим отримання амідоестерних інгібіторів корозії insitu, в одному
технологічному процесі, шляхом послідовного проведення амідування
естерифікації.
Для синтезу інгібіторів корозії
використовували лабораторну установку, що складалася з скляного трех горлого
реактора (4), термометра (3), перемішуючого пристрою (1) з живленням через ЛаТР
(2) (для регулювання обертів).
Рис.
Схема приладу для проведення синтезів.
Де
1- електродвигун, 2- ЛаТР, 3 – термометр, 4 – скляний реактор, 5 – пісчана
(оливна) баня, 6 – електроплитка.
Дослідження кінетики процесів естерифікації,
амідування, а також контроль повноти проведення реакцій проводились шляхом визначення
значеннь кислотного числа реакційної маси або продукту реакції.
Визначення значень кислотних чисел проводили за
стандартною методикою ГОСТ 11362.
В зв¢язку з тим, що
реакції амідування – етерифікації проводяться при підвищених
температурах була розроблена проста конструкція зручного пробовідбірника, що
дозволяє відбирати “гарячі” проби рідкої
реакційної маси (Схема 3.2.) [201].
Пробовітбірник складається з двох
зігнутих скляних трубок (1), стандартного шприця (2), резинової термостійкої
пробки (3), що має два отвори під скляні трубки, знімного скляного стандартного
бюксу (4).
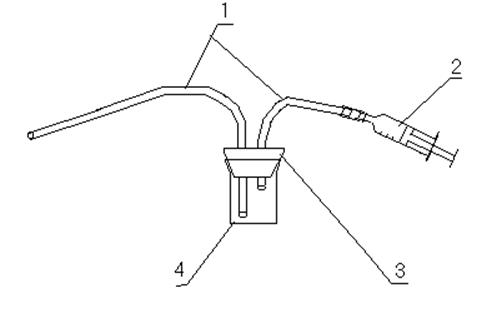
Схема 3.2. Пробовідбірник “гарячих” проб.
Де 1) скляні
трубки, 2) шприць стандартниого обєму, 3) резинова пробка з отворами, 4)
стандартний бюкс.
Для відбору проби, скляну трубку
пробовідбірника занурювали у реакційну масу і шприцем (2) створювали
розрідження повітря в бюксі (4) В наслідок різниці тисків, реакційна маса
потрапляє у бюкс (4). Бюкс від’єднували з пробовідбірника і закривали притертою
кришкою. Якщо є необхідність знати наважку проби, бюкс двічі зважують до і
після відбору.
З літературного огляду
встановлено, що рівень захисної ефективності консерваційних олив комплексно
залежить від властивостей: вологовитіснення та утворення на поверхні металу
стійкої, в умовах застосування, непроникної для корозійних чинників захисної
плівки.
СИНТЕЗ ОЛИВОРОЗЧИННОГО ІНГІБІТОРУ КОРОЗІЇ НА ОСНОВІ
КАРБАМІДУ.
4.1.
Дослідження взаємодії жирних кислот з карбамідом
Карбамід
та його похідні знайшли широке застосовання як добрива, ліки, смоли, вибухові
речовини, комплексоутворювачи тощо.
Продукти
амідування карбамідом деяких органічних речовин (алкіл малеіновий ангідрид, алкіл
сульфонати, алкіл нітросполуки) зарекомендували себе ефективними
багатофункціональними оливорозчинними додатками до олив та мастил [1,2 14-16, 153-168].
Іншою доступною сировиною на вітчизняному ринку є
насичені та ненасичені жирні кислоти рослинного походження, в тому числі
олеїнова кислота, яка у великих кількостях виробляється на декількох
підприємствах України.
Досліджували
продукти та кінетику процесу амідування олеїнової кислоти карбамідом.
Розчинення
карбаміду в чистій олеїновій к-ті, з утворенням олеату сечовини (3), (Схема
4.2.1) відбувається при температурі 120-125 оС, причому утворюється
комплексний зв’язок між карбоксилатним воднем кислоти та неподільною
електронною парою атому азоту молекули карбаміду [202].
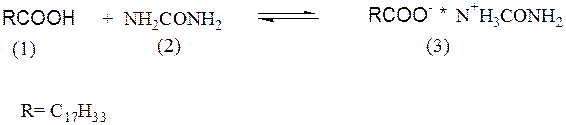
Схема 4.1.1
Відчутна швидкість конверсії олеїнової кислоти у результаті проходження
процесів амідування спостерігається при температурі 155 - 160 оС. (Рис 4.1.1, крива 1) Підвищення температури призводить
до прискорення швидкості конверсії (Рис 4.1.1, крива 2), однак при 200-210 оС
зменшується кінцева глибина перетворення олеїнової кислоти (Рис 4.1.1,
крива 3), що пояснюється активізацією процесів термолізу карбаміду (схема 4.1.2) [169, 202, 203]. Тому температура ведення процесу амідування не повинна перевищувати
200 оС.
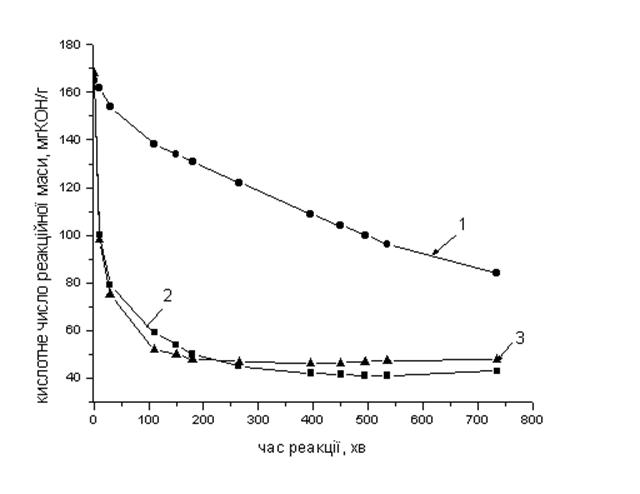
Рис 4.1.1 Зміна кислотного числа реакційної маси в
процесі амідування олеїнової кислоти карбамідом при температурі 1) 155-160 оС, 2)
180-190 оС, 3) 205-215 оС.
Хімізм амідування жирних кислот карбамідом, при температурі
вище 150 оС, є складним, що пов’язано з перебігом хімічних
перетвореннь карбаміду (Схема 4.1.2).
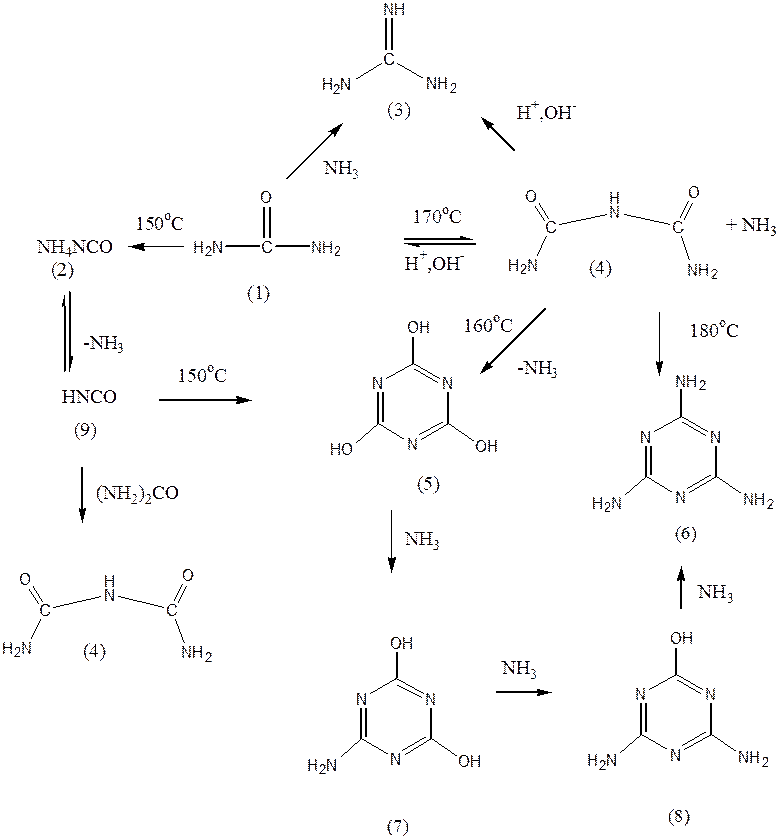
Де (1)- сечовина, (2)- ціанат амонію, (3) - гуанідин,
(4) - біурет (5) - ціанурова кислота, (6) - меламін, (7) - аммелін, (8) -
аммелід, (9) - ізоціанова к-та .
Схема 4.1.2, термоліз сечовини.
В процесі розкладу карбаміду можуть утворюватись такі
амідуючі агенти як: аміак, біурет (4), гуанідин (3), меламін (6), аммелін (7),
аммелід (8) (схема 4.1.2). Тому, під час реагування жирних кислот з карбамідом
(при температурах > 150 оС) можливе утворення як уреїдів (4) та
амідів (7) так і інших сполук (схема 4.1.3).
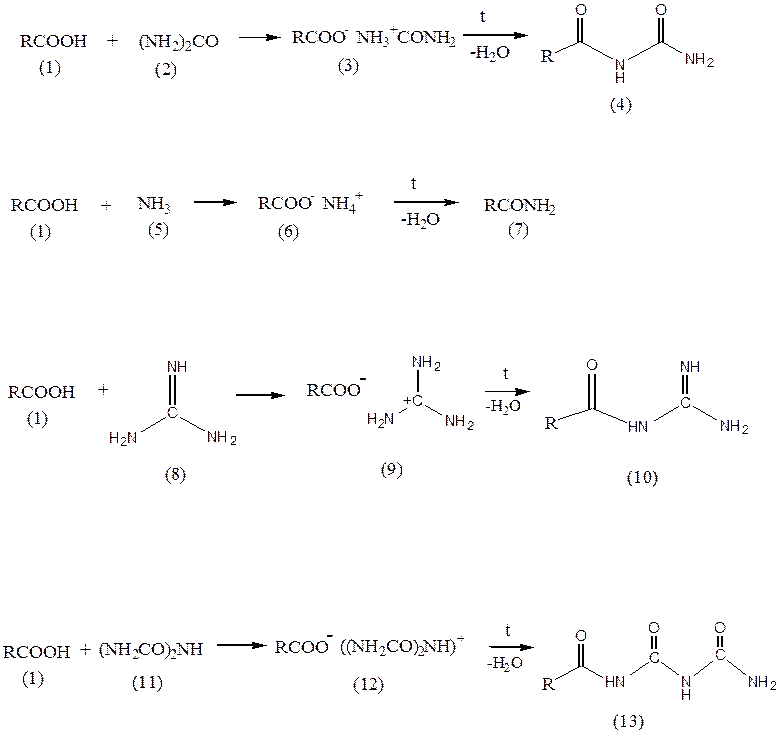
Де R=alkyl (С17Н35), alkenyl (С17Н33)
схема 4.1.3
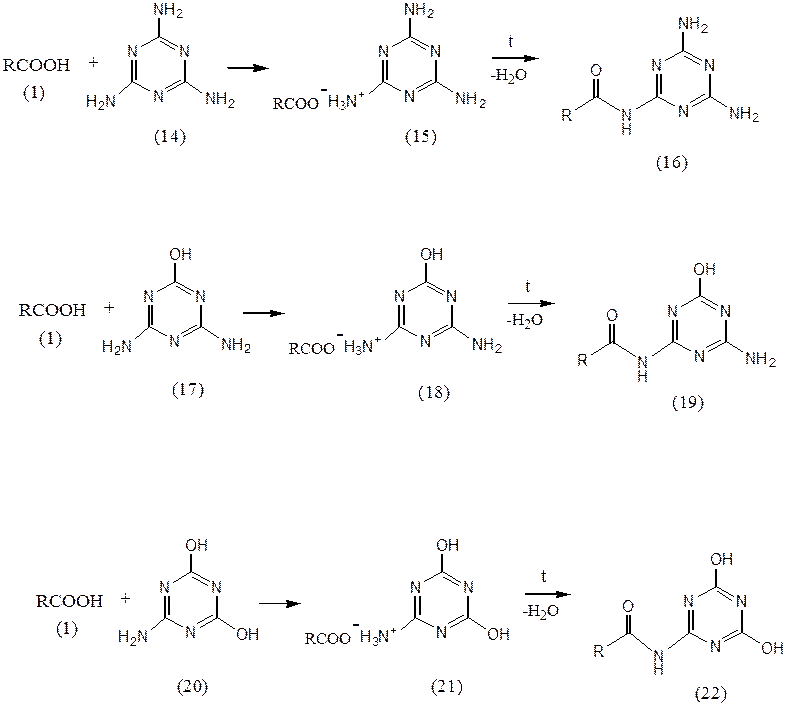
Де R=alkyl (С17Н35), alkenyl (С17Н33)
схема 4.1.3 (продовження)
Утворення
похідних меламіну, амеліну, і меламіду можливе лише у найменших кількостях, так
як остані синтезуються у жорстких умовах при високій концентрації карбаміду [202]. Утворення гуанідину, також є малоімовірним, адже
даний процес може відбуватися тільки при високій концентрації вільного аміаку.
Останній, в умовах синтезу відразу після виділення реагуватиме з кислотою.
Біурет утворюється у порівняно м’ягших умовах (t=152-172 oC). [202, 203].
Однак процес амідування жирних кислот біуретом може ускладнюватись
через його низьку амідуючу здатність, що зумовлено електронним індукційним
ефектом двох карбонільних груп. Крім того, при температурі вищій 160 оС
біурет, перетворюється на ціанурову кислоту та аміак [169]. Більш
імовірними продуктами процесу амідування олеїнової кислоти карбамідом є прості
аміди, адже сечовина здатна розкладатись з поступовим виділенням аміаку та
цінової кислоти, (яка в умовах процесу) вже при температурі 90-100 оС, [204, 205] причому хід цього процесу прискорюється у присутності кислот [206].
Таким
чином, основними продуктами прямої взаємодії жирних кислот та карбаміду при
160- 180 оС є уреїди і аміди жирних кислот, а також ціанурова кислота (ціанова к-та в умовах процесу полімеризується у ціанурову к-ту) [202]. Причочому
втрати карбаміду в наслідок термічних перетвореннь призводять до необхідності
введення в реакцію його надлишку [207].
Реагування
карбаміду (1,4 моль) та олеїнової кислоти (1 моль) при температурі 180-185оС
відбувається спокійно, без вспінювання. В
ході реакції (при застосуванні хімічно чистої олеїнової к-ти) спостерігається
поступове потемніння реакційної маси.
Оптимальне
значення кислотного числа для деяких оливорозчинних додатків отриманих шляхом
ацилювання може становити 30-20 мгКОН/г [152, 208].
Тривалість процесу амідування жирних кислот карбамідом при температурі 175-185 оС, до значення кислотного числа 40 мгКОН/г
перевищує 8 годин (Рис. 4.1.1).
Суттєва тривалість та досить жорсткі умови проведення, роблять даний
процес енергозатратним та таким, що невідповідає сучасному стану більшості
виробничих баз.
Скорочення тривалості технологічних процесів можливе при застосуванні
каталізаторів.
Відомим каталізатором процесів амідування є оксид алюмінію [172]. Однак, у випадку
взаємодії олеїнової кислоти з карбамідом ефективність оксиду алюмінію є
низькою.
Відомо,
що у присутності вуглекислого газу швидкість розкладу карбаміду є вищою [209, 210]
Крім того
відомо, що карбамід з деякими неорганічними речовинами здатен утворювати
комплексні сполуки [202]. Причому існує вірогідність, що
ефективність таких сполук у реакціях амідування є вищою, порівняно з чистим
карбамідом.
З метою встановлення нових каталізаторів для процесу амідування жирних
кислот карбамідом досліджували солі вугільної кислоти.
В якості
каталітичних добавок досліджувались: гідроксид кальцію, карбонат натрію,
бікарбонат натрію, бікарбонат аммонію, карбонат калію, карбонат кальцію, кислий
фосфат кальцію. Каталітична ефективність обраних сполук встановлювалсь відносно
оксиду алюмінію.
Дослідження
проводили наступним чином:
В реакційну ємність обладнану автоматичним регулюванням температури та
перемішуючим пристроем завантажували 28,2 гр. (0,1 моль) олеїнової кислоти та
10 гр (0,14 моль карбаміду) після чого суміш гомогенізували при температурі 125 оС та додавали розраховану кількість карбонату металу, температуру
підіймали до 175-180 оС. В ході реакції, з фіксованням часу
відбирали пробу та визначали значення кислотного числа відповідно до ГОСТ 11362-76.
В результаті дослідженнь
встановлено, що карбонати лужних металів та амонію не впливають на швидкість
конверсії олеїнової кислоти. Однак продукти, що одержуються у присутності цих
солей мають менші значення кислотних чисел, що можна пояснити їх нейтралізуючою
дією (Рис 4.1.2-4.1.10).
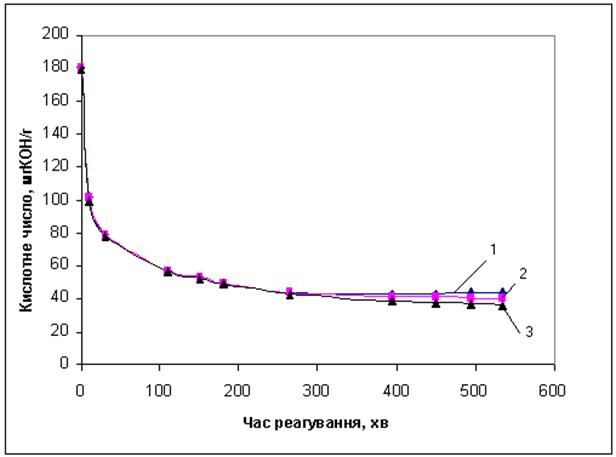
Рис. 4.1.2 Зміна кислотного числа реакційної маси в процесі
амідування
Олеїнової кислоти карбамідом 1- без добавок, та у
присутності бікарбонату амонію 2- 0,5%, 3- 1%.
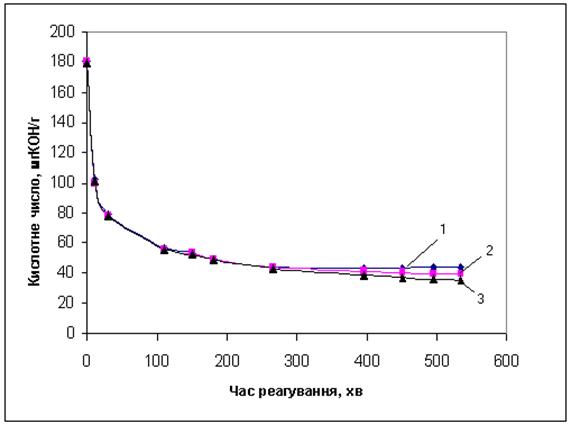
Рис. 4.1.3 Зміна
кислотного числа реакційної маси в процесі амідування олеїнової кислоти
карбамідом 1- без добавок, та у присутності бікарбонату натрію 2- 0,5%, 3- 1%.
Рис. 4.1.4 Зміна
кислотного числа реакційної маси в процесі амідування олеїнової кислоти
карбамідом 1- без добавок, та у присутності карбонату натрію 2- 0,5%, 3- 1%.
Рис. 4.1.5 Зміна
кислотного числа реакційної маси в процесі амідування олеїнової кислоти
карбамідом 1- без добавок, та у присутності карбонату калію 2- 0,5%, 3- 1%.
Рис. 4.1.6 Зміна
кислотного числа реакційної маси в процесі амідування олеїнової кислоти
карбамідом 1- без добавок, та у присутності оксиду алюмінію 2- 0,5%, 3- 1%.
Рис. 4.1.7 Зміна
кислотного числа реакційної маси в процесі амідування олеїнової кислоти
карбамідом 1- без добавок, та у присутності карбонату кальцію 2- 0,5%, 3- 1%.
Рис. 4.1.8 Зміна
кислотного числа реакційної маси в процесі амідування олеїнової кислоти
карбамідом 1- без добавок, та у присутності гідроксиду кальцію 2- 0,5%, 3- 1%.
У
присутності 0,5-1% карбонату кальцію швидкість конверсії олеїнової кислоти
значно підвищується (Рис 4.1.7). Причому ефективність дії карбонату
кальцію (Рис 4.1.7) є значно вищою ніж оксиду алюмінію – відомого
каталізтора процесу амідування (Рис. 4.1.6).
Так у присутності 1% карбонату кальцію значення кислотного числа реакційної
маси 40 мг КОН/г досягається на 90 хв процесу, а у присутності 1% оксиду
алюмінію на 210 хв процесу (Рис).
Рис. 4.1.9 Зміна кислотного числа реакційної
маси в процесі амідування.
Олеїнової кислоти карбамідом 1- без добавок, та у
присутності 1%мас. 2 – бікарбонату амонію, 3- оксиду алюмінію, 4- карбонату
кальцію.
Процес
амідування карбонових кислот проходить за схемою 1,. Константа швидкості
процесу амідування залежить від нуклеофільності амідуючого агенту, що в свою
чергу визначається просторовою делокалізованністтю неподільної електронної пари
атому азоту.
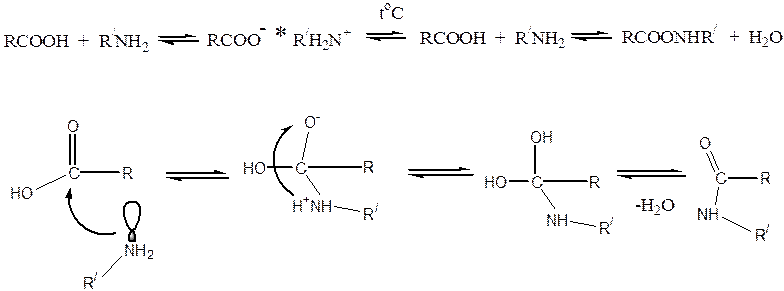
R, R/ = алкіл,
алкеніл
Схема
1
Нуклеофільність
молекули карбаміду (порівняно з молекулою аміаку) є низькою за рахунок
електронегативного ефекту карбонільної групи. Тому, взаємодія карбаміду та
олеїнової кислоти з утворенням уреїдів характеризується низькими значеннями
константи швидкості.
Однак, при
температурах вищих 150 оС сечовина послідовно перетворюється на
аміак, ізоціанат амонію, біурет, ціанурову к-ту і ін. сполуки (схема) Деякі з
цих речовин в умовах перебігу процесу також реагують з карбоновою кислотою.
Тому, процес взаємодії карбаміду та жирних кислот є складним, а його швидкість
є аддитивною функцією від швидкостей кожної з реакцій, частки яких визначаються
швидкісттю та напрямком розкладу карбаміду. Очевидно, що напрямок та швидкість
розкладу карбаміду визначають хімічний склад та властивості продуктів
амідування жирних кислот.
Встановлено,
що присутність карбонатів лужних металів при амідуванні олеїнової к-ти
карбамідом може впливати не тільки на швидкість конверсії кислоти, а й на
властивості одержуваних продуктів та нахисну здатність їх оливних систем Таблиця
(5, 6).
Таблиця 5
Властивості продуктів амідування , що були одержані у
присутності каталізаторів
Каталізатор |
Час проходження реакції, хв |
Зовнішній вигляд продукту |
Кислотне число, мгКОН/г |
Температура плавлення оС |
1% карбонат натрію |
530 |
Коричнева речовина |
35,2 |
62 |
1% бікарбонат натрію |
530 |
Коричнева речовина |
35 |
60 |
1% карбонат
калію |
530 |
Коричнева речовина |
36,1 |
61 |
1% карбонат
амонію |
530 |
Коричнева речовина |
35,2 |
58 |
1% оксид
алюмінію |
450 |
Коричнева речовина |
33 |
62 |
1% гідроксид
кальцію |
160 |
Коричнева речовина |
32 |
65 |
1% карбонат кальцію |
160 |
Коричнева речовина |
32,5 |
61 |
Без добавки |
530 |
Чорна мазеподібна речовина |
43,6 |
55 |
Таблиця 4.1.
Властивості
8%-их розчинів амідів у оливі І-20А
Аміди олеїнової к-ти синтезовані з додаванням |
Захисна здатність |
Стабільність |
Площа пластин Ст08пс, вражена корозією, % |
Час, до випадіння осаду, діб |
Після випробуваннь у камері сольового туману (5
циклів)
|
Після занурення у електроліт (14 діб)
|
1% карбонату натрію |
4
|
8
|
4 |
1% бікарбонату натрію |
5
|
6
|
1 |
1% карбонату
калію |
4
|
7
|
2 |
1% карбонату
амонію |
18
|
6
|
1 |
1% оксиду
алюмінію |
6
|
4
|
2 |
1% гідроксиду
кальцію |
1
|
5
|
7 |
1% карбонату кальцію |
2
|
4
|
10 |
Без добавки |
14
|
12
|
1 |
Виходячи з
того, що проведення взаємодії олеїнової кислоти у присутності карбонатів змінює
деякі властивості продуктів амідування можна прийти до висновку, що до зміни їх
хімічного складу.
Про
відмінності в хімічному складі свідчать ІЧ-спектри продуктів амідування
олеїнової к-ти карбамідом (які мають приблизно однакові значення КЧ). Так на
ІЧ-спектрі продукту одержаному в присутності 1% карбонату кальцію в області
спостерігається сателіт який імовірно відповідає сигналу валентних коливань
зв’язків N-H в молекулі
простого аміду олеїнової к-ти (рис. 1) [211]. Даний сигнал в меншій мірі
проявляється на ІЧ-спектрі продуктів амідування амідування олеїнової кислоти карбамідом, одержаних без додавання каталізаторів
(рис 2).
Рис.1 ІЧ-спектр продуктів амідування олеїнової кислоти
карбамідом у присутності 1% карбонату кальцію.
Рис.2 ІЧ-спектр продуктів амідування олеїнової кислоти
карбамідом одержаних без додавання каталізаторів.
З наведених
даних встановлено, що найефективнішими каталізаторами процесу амідування
олеїнової к-ти карбамідом виступають карбонат і гідроксид кальцію. Присутність
цих речовин також впливає на властивості одержуваних продуктів.
Можливою
взаємодією карбонату кальцію з субстратом, що може призвести до падіння
значення кислотного числа реакційної маси, є реагування з утворенням мил. Схема
2
Де R= C17H33
Схема
2
Однак зміна
кислотного числа у присутності 1% карбонату кальцію є більшою ніж розрахункова,
а припущення відносно утворення мил не пояснює в повній мірі ефекту від
введення карбонату кальцію.
Очевидним
актом взаємодії карбонату кальцію з субстроатом є адсорбція на його поверхні
молекул карбаміду та олеїнової к-ти, що полегшує взаємодію цих компонентів та
покращує водовіднімання.
Досить
імовірною може бути взаємодія між карбонатом кальцію та карбамідом з виділенням
аміаку - ефективного амідуючого агенту, який потім вступає у реакцію з
кислотою. Карбонат кальцію, поглинаючи вуглекислоту, перетворюються на
гідрокарбонат [212 ] який,
в умовах реакції виділяє вуглекислоту та перетворюється у карбонат [213] (Схема 3). Про взаємодію карбаміду з
карбонатом кальцію також свідчить підвищення рН при додаванні останнього до
гарячого водного розчину карбаміду.
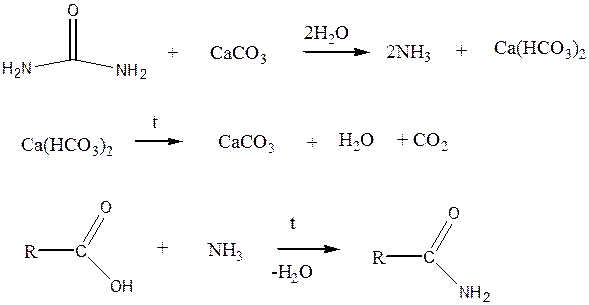
Де R= C17H33
Схема
3
При
додаванні до реакційної маси 0,5-1% гідроксиду кальцію останній може реагувати
як з олеїновою кислотою (Схема) так і з карбамідом [214]
(Схема)
Де R= C17H33
Схема
4.2.5
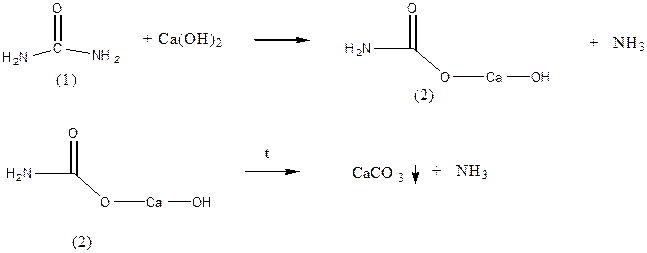
Схема
4.2.6, де (1) карбамід, (2) гідроксо карбамат кальцію.
В
результаті реакції нейтралізації утворюється олеат кальцію (3) (див. схему 4.2.5).
Кінцевим продуктом реагування гідроксиду кальцію з карбамідом є аміак і
гідроксокарбамат кальцію. Останній, при підвищеній температурі (вищій 60 оС)[214] розкладається на аміак та карбонат кальцію
схемою 4.2.6. В свою чергу, виділення карбонату кальцію пояснює встановлений
каталітичний ефект.
Очевидно,
при реагуванні карбаміду з жирними кислотами у присутності неорганічних
добавок, в тій чи іншій мірі, в залежності від їх хімічних властивостей,
одночасно мають місце усі перераховані процеси кожен з яких впливає як на
швидкість реагування так і на хімічний склад продуктів та їх властивості.
Таким чином
досліджено процес взаємодії олеїнової к-ти та карбаміду. Встановлено, що у
присутності 0,5 – 1% карбонату кальцію швидкість конверсії олеїнової к-ти
підвищується у 1,4 – 1,8 раз.
Враховуючи низьку
стабільність оливних розчинів більшості продуктів амідування олеїнової к-ти
карбамідом, останні можуть бути використані в якості оливорозчинних додатків
тільки при попередньому дослідженні сумісності з відповідними оливами.
Суттєвим
недоліком продуктів взаємодії карбаміду та олеїнової кислоти є високе значення
температури плавлення (55-65 оС), та низька стабільність оливних
концентратів, що ускладнює приготування та застосування відповідних
консерваційних засобів.
4.2. Розробка інгібіторів корозії на основі похідних
карбаміду
Вагомими
недоліками амідів є висока температура їх плавлення, та низька стабільність
оливних розчинів, що ускладнює їх дозування та обмежує застосування в складі
оливних композицій.
В
світовій практиці в якості ОІК широкого застосування набули амідоестерні
суміші, які в порівнянні з естерами та амідами мають низку переваг.
Також
естери триетаноламіну можуть слугувати ефективними розчинниками амідів при
отриманні рідких інгібіторів корозії на їх основі.
Похідні
триетаноламіну та жирних кислот, зокрема естери отримують реакцією
етерифікації, або термолізом відповідних солей. (Схема 3,4). [145,146]
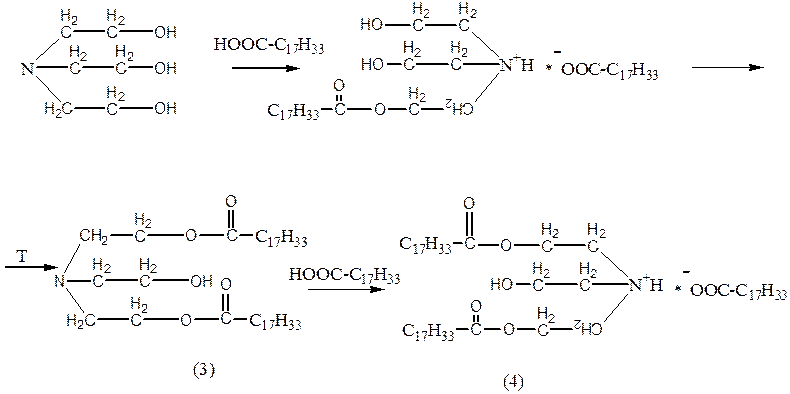 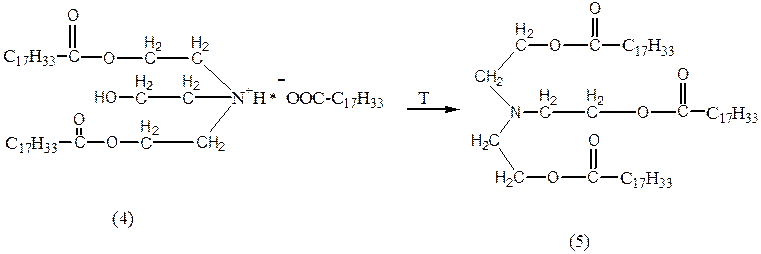
Схема 4.2.1
Серед
естерів триетаноламіну та олеїнової кислоти найвищою захисною ефективністтю,
відносно Ст08пс володіє моноестер та його сіль з олеїновою кислотою. Однак,
діестер триетаноламіну володіє кращою водовитісняючою дією [147-151].
Триестер триетаноламіну завдяки меншій спорідненості до
води володіє кращими вологовідштовхуючими властивостями, що важливо при
формуванні вторинних, гідрофобних, адсорбційних прошарків захисних плівок [14-16].
Тому, максимальну захисну здатність буде проявляти
інгібітор корозії, який містить суміш продуктів взаємодії триетаноламіну та
олеїнової кислоти. Це, в свою чергу, виключає необхідність направленого синтезу
одного з естерів під час отримання амідоестерних сумішей і встановлює мольні
співвідношення для синтезу похідних ТЕА і жирної кислоти ТЕА у межах: ТЕА :
олеїнова к-та = ( 1 : 1,8 – 2,5 ).
Для встановлення параметрів технології одержання ОІК
необхідно дослідити вплив стадійності проведення реакцій, та співвідношеннь
реагентів на основні властивості оливо розчинних інгібіторів корозії.
Встановлення оптимальної стадійності проводили шляхом
оцінки властивостей інгібіторів корозії отриманих у процесах з різною
послідовністтю проведення стадій при однакових мольних співвідношеннях вихідних
реагентів (ТЕА : карбамід : олеїнова к-та = 1 : 1 : 3).
1) Процес за схемою №1 (Рис 4.4.1) амідування
етерифікація проводили наступним шляхом:
У розрахованій кількості олеїнової кислоти розчиняли
карбамід, суміш витримували при температурі 180 оС протягом 4,5
годин. Охолоджували до температури 160 оС та при перемішуванні
додавали розраховану кількість триетаноламіну, реакційну масу витримували при
температурі 140 оС. (Рис)
2) Процес за схемою №2 (Рис 4.4.1 ) естерифікація
амідування проводили наступним шляхом.
У розраховану кількість олеїнової кислоти при
температурі 85 оС послідовно вводили карбамід та триетаноламін,
суміш витримували при температурі 140 оС протягом 2 годин.
Температуру підіймали до 180 оС при якій реакційну масу витримували
протягом 4,5 годин. В ході реакції відбирали проби та досліджували захисну
ефективність їх 8%-их розчинів у оливі І-20А.
3) Процес за схемою №3 (Рис 4.4.1 ) естерифікація
амідування (з розчиненням карбаміду в триетаноламіні) проводили наступним
шляхом.
До розрахованої кількості олеїнової кислоти розігрітої
до 90 оС при перемішуванні додавали розчин карбаміду в
триетаноламіні, реакційну масу витримували при температурі 135-140 оС
протягом 2 годин, температуру підіймали до 180 оС і витримували
протягом 4,5 годин. В ході реакції відбирали проби та досліджували захисну
ефективність їх 8%-их розчинів у оливі І-20А.
Одержання інгібітору за схемою №1 (амідування
естерифікація)
Одержання інгібітору за схемою №2 (естерифікація
амідування)
Одержання інгібітору за схемою №3 (естерифікація
амідування, з попередньою гомогенізацією карбаміду)
Рис. 4.4.1 (Схеми одержання ОІК на основі похідних
карбаміду)
На рис. 4.4.1 та у таблиці наведено властивості
інгібіторів корозії отриманих в результаті розглянутих процесів.
Рис.
4.4.1 Захина здатність розчинів (8% в оливі І-20А ) інгібіторів корозії отриманих за схемою амідування естерифікації в залежності від
кислотного числа, (визначена в умовах камери сольового туману, за 24
години)
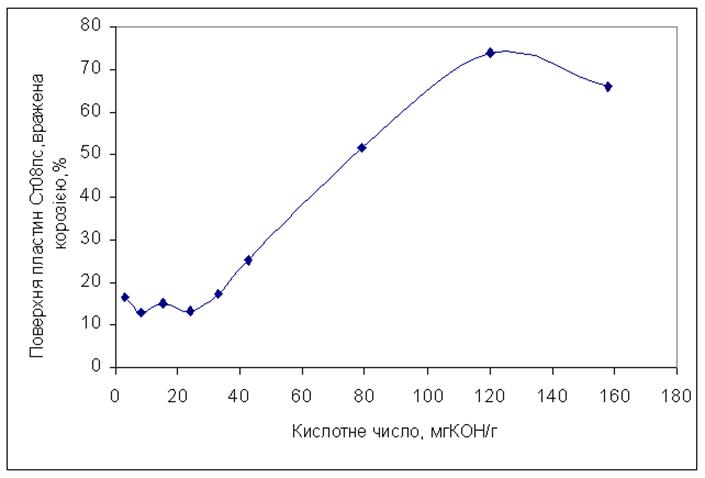
Рис.
4.4.1 Захина здатність розчинів (8% в оливі І-20А ) інгібіторів корозії
отриманих за схемою естерифікація амідування в залежності
від кислотного числа, (визначена в умовах камери сольового туману, за 24
години)
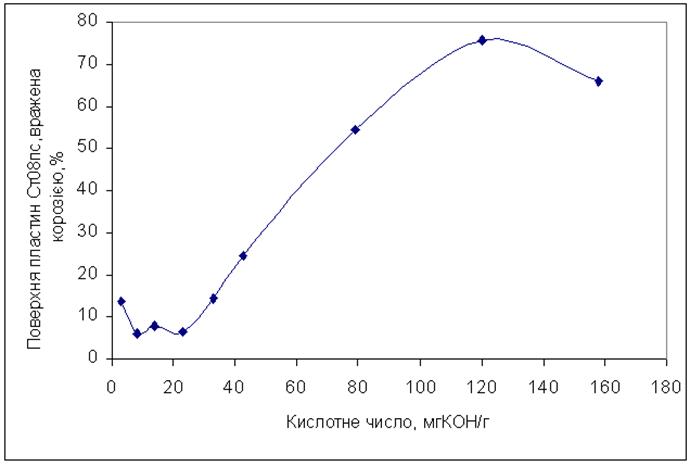
Рис.
4.4.1 Захина здатність розчинів (8% в оливі І-20А ) інгібіторів корозії
отриманих за схемою естерифікація амідування (з розчиненням карбаміду в
триетаноламіні ) в залежності від кислотного числа, (визначена в умовах камери
сольового туману, за 24 години)
В процесі, який прходить за схемою №1 – амідування –
етерифікація, отримуються оливорозчинні інгібітори корозії, максимальна захисна
здатність яких проявляється при значеннях кислотного числа в межах 7-28 мгКОН/г.
Однак вони мають низьку стабільність у часі, а для їх оливних розчинів
характерне виділення деякої кількості осаду, що повязано з низькою агрегаційною
стабільністтю ОІК.
В процесі №2 (рис. 4.4.1) з послідовним проведенням естерифікації та
амідування отримують стабільні за нормальних умов речовини, що без залишку
розчиняються в оливах з утворенням стабільних розчинів. Інгібітори одержані за
цією схемою, найвищу захисну здатність проявляють при значеннях кислотного
числа в межах 10-22 мгКОН/г.
Інгібітори корозії одержані в процесах естерифікації –
амідування (з попереднім розчиненням карбаміду в ТЕА) (схема №2, рис. 4.4.1 )
стабільні та проявляють дещо вищу захисну здатність в оливних розчинах в
порівнянні з ОІК, які було одержано за схемою №2 (рис. 4.4.1 ),
при тих же концентраціях.
Таким чином оптимальною схемою отримання амідоестерних
інгібіторів корозії є: “естерифікація – амідування з попередньою гомогенізацією
амідуючого та алкулуючого агентів. В результаті даного процесу одержують
стабільні, ефективні інгібітори корозії, що добре розчиняються в оливах і є
стабільними в часі.
Дана схема була обрана для подальших досліджень.
Проводили ряд синтезів з різним вихідним
співвідношенням реагентів, для встановлення оптимальних співвідношень амідів та
естерів в оливорозчинному інгібіторі корозії. Табл .
Табл . Співвідношення реагентів у синтезах
амідоефірних інгібіторів корозії
Реагент |
№1 |
№2 |
№3 |
№4 |
№5
|
№6
|
Мол. |
% |
мол. |
% |
мол. |
% |
мол. |
% |
мол. |
% |
мол. |
% |
Олеїнова
к-та |
2,2 |
79,5 |
2,5 |
79,5 |
3 |
80,1 |
3,5 |
80,3 |
5 |
81 |
7 |
81,3 |
триетаноламін |
1 |
19 |
1 |
3,5 |
1 |
14,1 |
1 |
12,2 |
1 |
8,5 |
1 |
6,2 |
карбамід |
0,2 |
1,5 |
0,5 |
17 |
1 |
5,8 |
1,5 |
7,5 |
3 |
10,5 |
5 |
12,5 |
Молярне
співвідношення карбамід/ триетаноламін |
0,2 |
0,5 |
1 |
1,5 |
3
|
5
|
Хід реакцій контролювався за зміною значення кислотного
числа реакційної маси. (Рис)
Схема Зміна кислотного числа реакційної маси, у ході реакцій
амідування етерифікації, при молярному співвідношенні карбамід триетаноламін:
1) N= 5; 2) N= 3; 3) N= 1,5; 4) N=1; 5) N=0,5; 6)
N=0,2.
Встановлено,
що швидкість конверсії олеїнової к-ти в процесі її амідування карбамідом є
нижчою ніж в процесі етерифікації, в зв’язку з чим підвищення концентрації
карбаміду в початковій реакційній масі призводить до уповільнення загальної
швидкості конверсії олеїнової кислоти. Так при вмісті карбаміду в початковій
реакційній суміші – 1,5% значення кислотного числа 30 мгКОН/г досягається на
180 хвилині, а при вмісті карбаміду 5,8 % на 320 хвилині процесу.
З метою встановлення
відповідності значення кислотного числа захисній здатності амідоестерних
сумішей, для проб реакційної маси із встановленими значеннями кислотних чисел,
визначали захисну здатність 8%-вих розчинів у оливі І-20А.
Захисна здатність визначалась
відповідно до ГОСТ 9.054 (метод 3- при зануренні у електроліт, методом 4- в
умовах камери сольового туману).
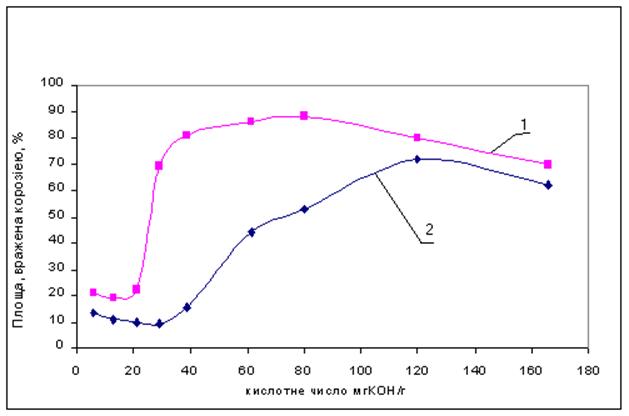
Рис. Залежність
захисних властивостей від кислотного числа амідоефірної суміші синтезованої з
молярним співвідношенням - мочевина / триетаноламін N=
0,2 при випробуванні 1) у електроліті, 2) у камері сольового туману
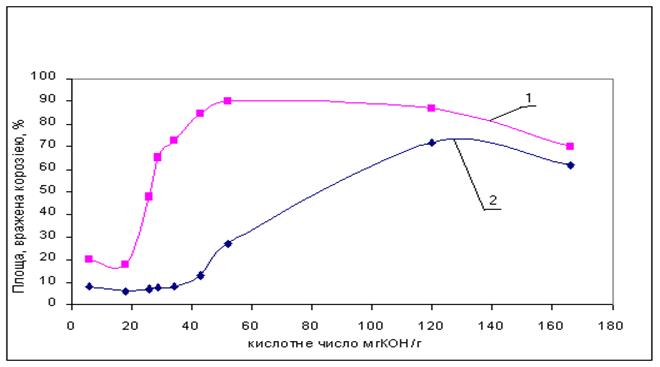
Рис. Залежність
захисних властивостей від кислотного числа амідоефірної суміші синтезованої з
молярним співвідношенням - мочевина / триетаноламін N=
0,5 при випробуванні 1) у електроліті, 2) у камері сольового туману
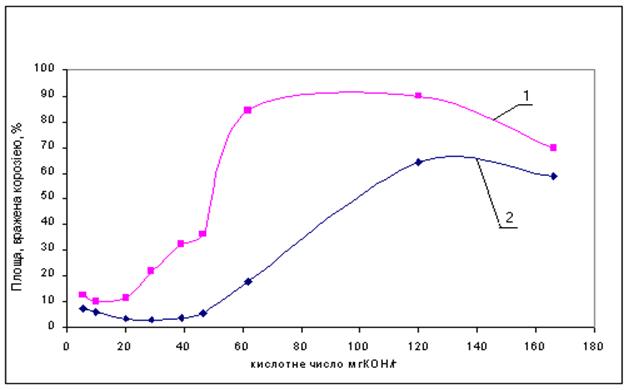
Рис Залежність
захисних властивостей від кислотного числа амідоефірної суміші синтезованої з
молярним співвідношенням - мочевина / триетаноламін N=
1 при випробуванні 1) у електроліті, 2) у камері сольового туману.
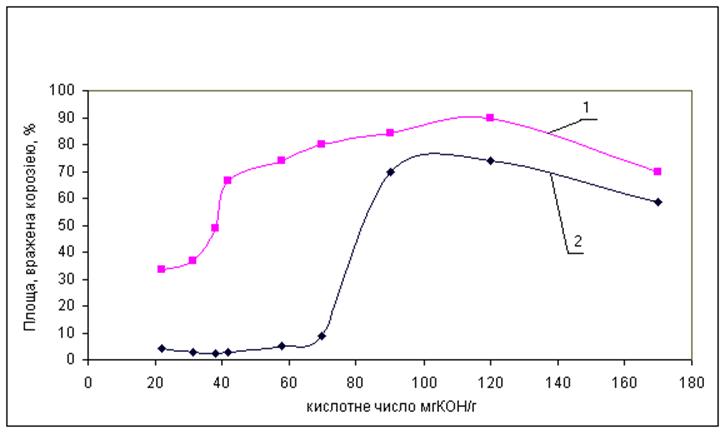
Рис Залежність
захисних властивостей від кислотного числа амідоефірної суміші синтезованої з
молярним співвідношенням - мочевина / триетаноламін N=
1,5 при випробуванні 1) у електроліті, 2) у камері сольового туману
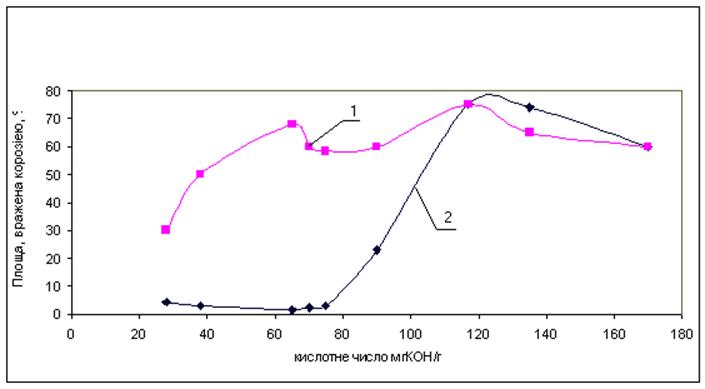
Рис Залежність
захисних властивостей від кислотного числа амідоефірної суміші синтезованої з
молярним співвідношенням - мочевина / триетаноламін N=
3 при випробуванні 1) у електроліті, 2) у камері сольового туману
Встановлено,
що захисні властивості амідоестерних сумішей на основі олеїнової кислоти
карбаміду та триетаноламіну знаходяться у неоднозначній залежності від
кислотного числа.
При
випробуваннях у камері сольвого туману та зануренні у електроліт із зменшенням
кислотного числа від 168 до 80 мгКОН/г захисна властивість продуктів реакції
зменшується. На початку реакції етерифікації з мил утворюються відповідні
естери. Як відомо мила триетаноламіну в суміші з відповідними жирними кислотами
також є інгібіторами корозії, причому їх ГЛБ є значно вищим за ГЛБ естерів, а
розчинність у оливі меншою. Це у свою чергу, сприяє адсорбції на металі з
утворенням напівтвердих плівок [14-16]. Збільшення естерного компоненту, очевидно, призводить до конкуруючої
адсорбції мил, кислоти, естерів та триетаноламіну, що негативно впливає на
захисні властивості інгібітору. Подальше зменшення кислотного числа призводить
до різкого підвищення захисних властивостей продуктів реакції.
В
умовах постійного занурення у електроліт, вищі захисні властивості проявляють
продукти які містять більшу кількість вільної кислоти (мають вище кислотне
число), що корелюється з літературним даними [Синя книга].
Оптимум
захисних властивостей амідоестерних сумішей в умовах електроліту
спостерігаеться вже при кислотному числі від 20 до 40 мгКОН/г. В той же час,
для умов камери сольового туману оптимальними є більш низькі кислотні числа.
Таблиця 17.
Таблиця 17
Оптимальні значення кислотних чисел та захисна здатність
амідоестерних ОІК.
Метод
Випробування |
Значення мольного співідношення карбамід/ триетаноламін |
0,2 : 1 |
0,5 : 1 |
1 : 1 |
1,5 : 1 |
3 : 1 |
Кислотне число
амідоефірних сумішей мгКОН/г |
В умовах електроліту |
20-35 |
18-35 |
20-40 |
30-40 |
50-70 |
У камері сольового туману |
14-20 |
10-19 |
10-20 |
22-25 |
25-30 |
Захисна здатність 8% р-нів ОІК в І-20А, поверхня
пластин Ст08пс вражена корозіє, % |
Після випробуваннь в умовах електроліту, (2 тиждні ) |
7-10 |
3-6 |
0-4 |
2-7 |
|
Після випробуваннь у камері сольового туману, (1 доба) |
16-20 |
14-18 |
5-10 |
18- 30 |
20-35 |
Таким
чином за результатами досліджень встановлено, що найвищу захисну ефективність у
оливі І -20А, мають амідоестерні суміші синтезовані із значенням мольного
співвідношення карбамід : триетаноламін = 0,5 :1,0 – 1 : 1. Оливо розчинний
інгібітор корозії, що одержувався встановленим шляхом при мольному (масовому)
співвідношенні компонентів : олеїнова к-та 3 (80,1%), триетаноламін 1 (14,1%),
карбамід 1 (5,8%) був позначений як МІК-8.
Для
встановлення хімічного складу синтезованого інгібітора, на основі, окремо
отриманих, продукту амідування олеїнової к-ти карбамідом і диефіру
триетаноламіну було приготовано модельні композиції ОІК із встановленими
значенями кислотних чисел та визначено їх захисну здатність у порівнянні з
синтезованим ОІК (з аналогічним співвідношенням вихідних речовин) ( Таблиця ).
Встановлено,
що синтезовані ОІК та модельні ОІК значно відрізняються за своїми основними
властивостями. Так, враження поверхні пластин Ст08пс, в умовах камери
сольового туману, при захисті 8% розчинами синтезованих ОІК із значенням
мольного співвідношення карбамід : ТЕА = 1:1, 1.5:1, 2:1 відповідно становить
9%, 11%, 14% , а для модельних ОІК: 15%, 18%, 35%.
Таблиця
Порівняння
синтезованих і модельних інгібіторів корозії.
Параметри модельних інгібіторів
|
Параметри синтетичних інгібіторів |
мольне відношення
реагентів
ТЕА : сечовина |
Кислотне
число, мгКОН/г |
Захисні властивості відносно Ст08пс, прокородована
поверхня, % |
мольне відношення
реагентів
ТЕА : карбамід |
Кислотне число, мгКОН/г |
Захисні властивості відносно Ст08пс, прокородована
поверхня, % |
після випробуваннь у камері сольвого туману (24
години) |
після випробуваннь в електроліті
(2 тиждні) |
після випробуваннь у камері сольвого туману (24
години)
|
після випробуваннь в електроліті
(2 тиждні)
|
0,2 |
10 |
19 |
7 |
0,2 |
12 |
18
|
7,5
|
1 |
17 |
15 |
5,5 |
1 |
15,5 |
9
|
1,5
|
1,5 |
21 |
18 |
4 |
1,5 |
22 |
11
|
2
|
2 |
23 |
35 |
5 |
2 |
24 |
14
|
2
|
Крім того, модельні ОІК одержані з мольним
співвідношенням карбамід : ТЕА = 1 : 1– 2, на відміну від синтезованих ОІК з
часом у оливних розчинах утворють осад. Тобто продукти одержані за схемою №3
(Рис) мають кращі захисні властивості ніж модельні суміші, що очевидно
пов’язано із синергетичним ефектом який проявляється при наявності в
амідоестерній суміші проміжних або інших сполук.
Відмінність у властивостях між синтезованими і
модельними ОІК можна пояснити їх різним хімічнимим складом, про що свідчать
дані ІЧ-спектроскопії (Рис).
Аналізуючи ІЧ-спектри можна пересвідчитись, що спектр
модельного ОІК (отриманого змішуванням амідів та триетаноламін диолеату 1:2)
(рис 1.) майже ідентичний спектру ОІК синтезованого шляхом послідовно
проведених процесів амідування та естерифікації (Рис. 2. ), в той час як
ІЧ-спектр ОІК синтезованого в результаті послідовно проведенних процесів
естерифікації – амідування має деякі відмінності ( Рис. 3.)
Рис.
1. Спектр амідоестерного ІК отриманого шляхом змішування 2 мас. одиниць
триетаноламін диолеату та 1 мас. одиниці продукту амідування олеїнової к-ти
карбамідом.
Рис.2. Спектр продукту отриманого
шляхом поступового реагування олеїнової к-ти (3 молі) з карбамідом (1 моль) та
триетаноламіном (1 моль).
Рис. Спектр продукту, що був отриманий шляхом поступового
реагування олеїнової к-ти з триетаноламіном та карбамідом.
Так
ІЧ-спектр ОІК, синтезованого в результаті послідовно проведенних процесів
естерифікації – амідування, має три сигнали в області 1700 см-1, що
належать валентним коливанням карбонільного зв’язку не менше ніж трьох
функціональних групп. Крім того помітні відмінності між сигналами, що
знаходяться у області 700-1500см –1 “відбитків пальців”.
Виходячи з хімічних властивостей карбаміду та
аміноспиртів можна припустити, що у складі синтезованих інгбіторів можуть бути
присутні продукти послідовної взаємодії триетаноламіну, карбаміду та жирної
кислоти.
Для встановлення причин, що призводять до відмінностей
в хімічному складі синтезованих за схемою №3 (Рис) від модельних амідоестерних
сумішей, проводили взаємодію карбаміду з:
-
триетаноламіном і наступною
конденсацією одержаного адукту з олеїновою кислотою.
-
триетаноламін моно олеатом.
Встановлено, що реакція між карбамідом та
триетаноламіном при мольному співвідношенні 1:1 відбуваеться з виділенням
аміаку (про що свідчить характерний запах) вже при температурі 85 оС.
Зміни на ІЧ спектрі суміші ТЕА і карбаміду, зняті до
нагрівання (рис. 1) і після завершення виділення газу (рис. 2) також свідчать
про перебіг реакції. Причому, імовірно, реагування ТЕА і карбаміду проходить по
карбонільній групі карбаміду та гідроксильним групам триетаноламіну, про що
свідчить відносне зменшення інтенсивності їх сигналу (1700см -1) та
(3600 – 3200см -1) .
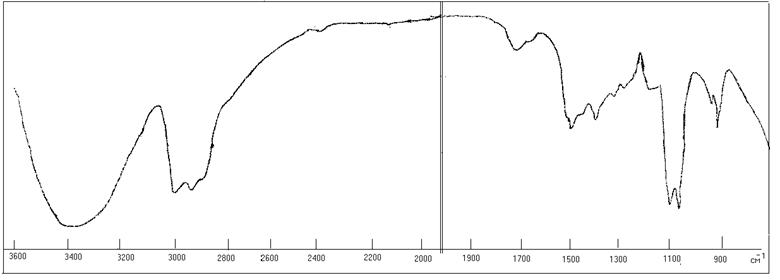
Рис.1 ІЧ спектр ТЕА.
Рис.2 ІЧ спектр
суміші ТЕА і карбаміду знятий до нагрівання.
Рис.3 ІЧ спектр
реакційної суміші після реагування ТЕА і карбаміду.
Нагрівання ТЕА і карбаміду супроводжується возгонкою
білої кристалічної речовини, яка сублімується на стінках дефлігматору. Після
реакції в реакторі утворюється прозора червона в¢язка рідина
з неприємним запахом і значенням лужного числа в межах 265 - 278 мгКОН/г.
Рис.4 хроматографічний
спектр реакційної суміші після реагування ТЕА і карбаміду.
В результаті хроматографічних дослідженнь встановлено,
що адукт взаємодії карбаміду та триетаноламіну являє собою суміш речовин,
основною з яких є (або утворюється в результаті розкладу) триетаноламін
(65-70%).
Також встановлено, що в адукті взаємодії технічного
триетаноламіну та карбаміду відсутні діетаноламін та моноетаноламін про що
свідчить різке зменьшення інтенсивності сигналів на 1,12 та 2,39 хвилині (Рис
4) у порівнянні з хроматографічним спектром початкового триетаноламіну (Рис 5).
Зменшення вмісту моноетаноламіну та діетаноламіну в адукті взаємодії карбаміду
та триетаноламіну імовірно можна пояснити їх реагуванням з карбамідом.
Для підтвердження даного припущення досліджували
взаємодію хімічно чистого діетаноламіну (tпл = 28 оС)
та карбаміду. При підігріванні карбаміду та триетаноламіну в молярному
співвідношенні 1 : 1, до температури 90 оС спостерігається одночасне
виділення аміаку та возгонка білої кристалічної речовини, що володіє неприємним
запахом, має лужну реакцію. Після завершення реакції (завершення кипіння t =
140 oC) в
реакторі залишається червона рідина (7-10 % від початкової реакційної маси) яка
,імовірно, являє собою осмолений ДЕА.
Адукт взаємодії ТЕА і карбаміду має здатність
реагувати з жирними кислотами при температурі 130-140 оС, про що
свідчить падіння кислотного числа в результаті нагрівання його суміші з
олеїновою кислотою. Встановлено, що 16-18 вагових частин адукту взаємодії
карбаміду з ТЕА здатні прореагувати з 45 ваговими частинами хімічно чистої
олеїнової кислоти. Причому швидкість конверсії кислоти в даному процесі є
значно вищою ніж у процесі амідування олеїнової к-ти карбамідом ( ІЧ спектр
даного продукту наведено на рис. 4.)
Отриманий таким чином продукт був позначений як
зразок №1.
Рис.
5 ІЧ
спектр продукту послідовної взаємодії триетаноламіну з карбамідом та олеїновою
кислотою
( продукт №1)
Перемішування при температурі 130-140 оС
карбаміду в середовищі неповних ефірів триетаноламіну також призводить до
хімічних перетворень, що відбуваються з виділенням аміаку.
Так при нагріванні (140-150 оС),
триетаноламін моно олеату (1 моль) та карбаміду (1 моль), до моменту
припинення виділення аміаку отримували густу одорідну рідину темно червоного
кольору, ІЧ спектр якої наведено на рис.6. Даний продукт (№2) на відміну від
(№1) має слабкий специфічний неподразнюючий запах.
Рис.6 ІЧ спектр
продукту реакції карбаміду з триетаноламін моноолеатом (продукт №2).
Реагування триетаноламін ди-олеату (1 моль) та карбаміду
(1 моль), до моменту припинення виділення аміаку (за температури 140-150 оС)
порівняно із процесом отримання (№2) проходить менш інтенсивно (менша
інтенсивність виділення аміаку). Причому отримуваний продукт (№3) представляє
густу рідину темно червоного кольору, що містить тверді домішки чорного
кольору.
Захисну здатність оливних розчинів
синтезованих продуктів досліджували за методом-3 (в камері сольового туману)
ГОСТ 9.054. В ході досліджень оцінювали площу
металів, що була вражена корозією, через 24 години випробувань. Результати
випробувань наведено у таблиці. Дослідженнями встановлено, що за захисною
здатністтю, відносно чорних металів (Ст08пс,
Ст10, СЧ 18), продукти №1 та №2,
перевершують триетаноламін моноолат та синтезований амідоестерний інгібітор
корозії приблизно в 1,7 та 4 рази відповідно. Так при випробуванні 4% оливних
розчинів корозійне враження Ст08пс склало для триетаноламін моноолеату 24%,
амідоестерного інгібітору корозії 25%, інгібітору №1- 7%, інгібітору №2 – 4%.
Такий рівень захисної здатності продуктів спостерігається і при випробуванні на
Ст10, Ст40, СЧ 18 див. табл.1
Таблиця
1
Захисні
властивості продуктів конденсації карбаміду з ТЕА та його похідними.
Продукт,
концентрація в оливі І-20А, % мас. |
Результати
випробувань, у камері сольового туману, протягом 24 годин, відносно
|
Ст08пс
|
Ст10
|
Ст40
|
СЧ 18 |
площа
вражена корозією, %
|
Олеат
триетаноламіну |
|
2 |
45
|
33
|
22
|
56 |
4 |
24
|
18
|
12
|
35 |
8 |
6
|
5
|
2
|
7 |
Амідо
естерний ОІК (Зразок) |
|
2 |
52
|
35
|
20
|
56 |
4 |
25
|
22
|
14
|
26 |
8 |
7
|
4
|
0
|
10 |
Зразок
№1 |
|
2 |
28
|
24
|
19
|
24 |
4 |
7
|
6
|
6
|
10 |
8 |
0
|
0
|
2
|
1 |
Зразок
№2 |
|
2 |
18
|
11
|
12
|
20 |
4 |
4
|
3
|
6
|
5 |
8 |
0
|
1
|
0
|
1 |
Таким
чином, встановивши високі захисні властивості продуктів взаємодії карбаміду
триетаноламіну та олеїнової к-ти (Зразок №1) і моноолеату триетаноламіну з
карбамідом (Зразок №2) можна припустити їх наявність в амідоефірних
оливорозчинних інгібіторах корозії, які за захисними властивостями перевершують
модельні амідоестерні інгібітори корозії.
Так
наприклад ОІК, що був приготований шляхом змішування 30% амідів олеїнової
кислоти, 58% диолеату триетаноламіну, 2% олеїнової кислоти та 10 % зразку №1 за
захисними властивостями відповідав ОІК (КЧ = 15,5 мгКОН/г) синтезованому (з
реагентів взятих у співвідношенні: 80,1 % олеїнової кислоти; 14,1%
триетаноламіну; 5,8% карбаміду) по схемі №3 (Рис 4.4.1).
Таким
чином, в рамках створення нових ОІК, досліджено процес взаємодії
триетаноламіну, карбаміду та олеїнової кислоти.
Встановлено,
що хімічний склад та захисна здатність ОІК, одержаних з обраної сировини,
залежить як від співвідношеннь та послідовності завантаження реагуючих речовин
так і від температурного режиму ведення процесу.
ОІК
з оптимальним хімічним складом, що відповідає стабільності та високій захисній
здатності його оливних розчинів, одержується шляхом послідовної естерифікації
амідування олеїнової (3-3,5 моль) кислоти розчином карбаміду (1 моль) в триетаноламіні
(1 моль) до значення кислотного числа 10-20 мгКОН/г.
В
даному випадку, окрім амідів та естерів олеїнової кислоти утворюються продукти
взаємодії карбаміду з триетаноламіном та олеїновою кислотою і
триетаноламін-олеатів з карбамідом, що позитивно впливає на захисну здатність
інгібітору.
4.3 Дослідження впливу хімічного
складу жирної кислоти на властивості амідоестерних ОІК
Основним
домішком до технічної олеїнової кислоти, яку одержують з рослинної сировини, є
стеаринова кислота.
В
залежності від сировини, а також технології одержання олеїнової кислоти до її
складу може входити від 1 до 45 % стеарину. Враховуючи те, що фізикохмічні
властивості похідних олеїнової та стеаринової кислот є різними, вміст останньої
може вплинути на основні властивості ОІК, що були одержані з відповідної
сировини [215]. Ряд
позитивних якостей стеаринової кислоти дає змогу одержувати на її основі досить
ефективні ОІК [177].
Тому,
вбачається доцільність у дослідженні впливу стеаринової кислоти на властивості
відповідних ОІК та їх оливних розчинів.
Температури
плавлення похідних стеаринової кислоти є вищими за температури плавлення
похідних олеїнової кислоти. Для дистеарату триетаноламіну Тпл= 53 оС,
а при амідуванні стеаринової кислоти (1моль) карбамідом (1,3 моль) утворюється
речовина, що плавиться в межах 64 - 68 оС. Відмінності у хімічній
будові та фізикохімічних властивостях похідних стеаринової і олеїнової кислоти
можуть вплинути на захисну здатність і стабільність оливних розчинів синтезованих
інгібіторів корозії. [176, 177, 215].
При
стоянні оливних розчинів амідоестерних ІК приготованих на основі олеїнової
к-ти, яка містить стеарин спостерігається виділення осаду, що неодмінно
призводить до зменшення її концентрації в об’ємі оливного розчину. Осадження
похідних стеаринової кислоти на поверхні металу, під час консервації призводить
до підвищення ефективності захиної плівки оливи.
Для
комплексного дослідження впливу стеаринової кислоти на агрегаційну стабільність
та захисну здатність оливних розчинів амідоестерних інгібіторів корозії
проводили ряд синтезів ОІК з використанням суміші жирних кислоти (олеїнової та
стеаринової) з різним вмістом стеарину та визначали захисної здатність їх 8%
оливних розчинів ,відносно Ст08пс, відразу після приготування та після
відстоювання (протягом 4 діб).
Синтези
(при співвідношеннях реагентів жирна к-та 80%, Триетаноламін 14%, карбамід 6%
) проводили за схемою естерифікація - амідування до значення КЧ реакційної
маси в межах 15- 21 мгКОН/г.
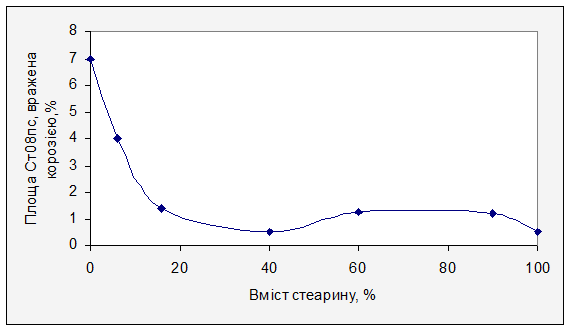
Рис 1. Вплив вмісту
стеарину в загальному жирнокислотному складі на захисну здатність 8%-розчинів
ОІК (В умовах постійного занурення у електроліт протягом 15 діб.) нанесених на
пластини Ст08пс через 30 хв після приготування.
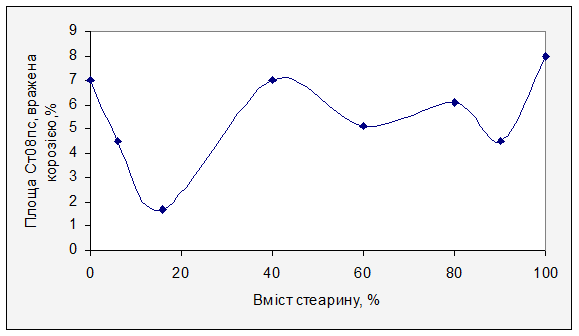
Рис 1. Вплив вмісту стеарину в загальному
жирнокислотному складі на захисну здатність 8%-розчинів ОІК (В умовах
постійного занурення у електроліт протягом 15 діб.) нанесених на пластини
Ст08пс через 3 доби після приготування.
За
змінами у захисній здатності оливних розчинів одержаних інгібіторів можна
зробити висновки про вплив жирнокислотного складу на їх стабільність та
захисну здатність.
Збільшення
вмісту похідних стеаринової кислоти в ОІК до 15%, призводить до підвищення їх захисної
здатності . При вмісті похідних стеарину > 18% зростає схильність міцел
інгібітору до агрегації, спостерігається більш інтенсивна седементація , яка
призводить до падіння захисної здатності інгібіторів (Рис. 2).
Виходячи з результатів досліджень, для виробництва
амідоестерного інгібітору корозії рекомендується застосовувати олеїнову кислоту
із вмістом стеарину до 10-15%.
ДОСЛІДЖЕННЯ ПОВЕРХНЕВИХ ПРОЦЕСІВ З УЧАСТТЮ ІНГІБІТОРА
НА ОСНОВІ ПОХІДНИХ КАРБАМІДУ – МІК-8
6.1
Дослідження взаємодії інгібітора МІК– 8, одержаного на основі похідних
карбаміду, з металевою поверхнею
Відомо, що інгібітори корозії є
поверхнево активними речовинами. Їх дія базується на основі зміни енергетичного
стану та хімічного складу при поверхневого об’єму металу. Тому досліджували
вплив МІК-8, інгібітору створеного на основі похідних карбаміду, на стан
металевої поверхні металу.
Природу взаємодії інгібітора
МІК-8 з поверхнею металу (Ст08пс) визначення шляхом встановлювлення ефекту
післядії.
Таблиця
Прояв
ефекту післядії МІК-8 відносно Ст08пс
Спосіб
підготовки, та номер
пластини |
Поверхня Ст08пс вражена
корозією після випробуваннь в умовах електроліту, % |
1
доба |
2
доба |
3
доба |
4
доба |
5
доба |
Обробка інгібітором МІК-8,
видалення інгібітора розчинником |
1 |
0 |
2 |
6 |
7 |
7,5 |
2 |
0 |
1 |
4 |
10 |
12 |
3 |
0,5 |
2,5 |
5 |
7 |
8,5 |
Промивка розчинником (без нанесення додатків) |
8 |
4 |
15 |
28 |
43 |
56 |
9 |
4 |
16 |
24 |
38 |
53 |
Випробуваннями встановлено, що
пластини Ст08пс, які були попередньо оброблені інгібітором МІК-8 менш підвласні
корозійній дії електроліту ніж пластини які небули оброблені інгібітором. Середній
ступінь корозійного враження пластин Ст08пс, що були оброблених інгібітором
МІК-8, після 5 діб випробувань у електроліті, становить 9,3%, а для пластин,
що не були оброблені додатками –54,5 %.
За результатами випробуваннь
можна зробити висновок, що оливорозчинний інгібітор коррозії МІК-8, створений
на основі похідних карбаміду, відносно Ст08пс володіє ефектом післядії, тобто
містить такі компоненти які по відношенню до поверхні чорних металів проявляють
хемосорбційну активність.
Для більш ретельного вивчення плівки МІК-8 на поверхні Ст08пс було
застосовано методи електронного зондування. Електронними
методами досліджували три точки на пластинах Ст08пс:
-
Точка №1 на чистій поверхні Ст08пс.
-
Точка №2 на поверхні Ст08пс, що була оброблена інгібітором МІК-8, розчинником
та випробувана у електроліті.
-
Точка №3 у ділянці зародження корозійного враження поверхні пластини Ст08пс,
що була оброблена інгібітором МІК-8, розчинником та випробувана у
електроліті
Електронні
спектри знімались у вигляді диференційних залежностей dN/dE=f(E).
З
вивчення Оже області електронних спектрів встановлено, відмінності у хімічному
складі приповерхнового об’єму в обраних точках дослідження. Так у точках №2,№3
(приповерхневий об’єм пластин, що були оброблені МІК-8) порівняно з точкою 1
(чиста поверхня Ст08пс) міститься значно менша кількість заліза (майже повна
відсутність сигналів 800-860 еВ) та кисню (сигнал при 440-480 еВ) (Мал. 5,6,7).
Крім того сигнал кисню (440-480 еВ) у точці №1, відповідає неорганічно
зв’язаному кисню, а для точок №2, №3 характер даного сигналу відповідає кисню,
що зв’язаний у органічну сполуку. На електронних Оже спектрах досить чітким є
сигнал вуглецю, причому для точки №1 форма даного сигналу відповідає sp3
гібридизованим атомам вуглецю, який імовірно знаходиться у вигляді карбідну, а
для точок №2, №3 ,також, спостерігається sp2
гібридизований вуглець, який зв’язаний з трьома сусідніми атомами, що
притаманно органічній сполуці. Приповерхневий об’єм Ст08пс, що була оброблена
МІК-8, з наступним випробуванням у електроліті (точки №2, №3) також містить
атоми азоту (сигнал 380-400 еВ) та сірки (сигнал 155-170 еВ). Крім того, точка
3 (на ділянці з започаткуванням корозії) на відміну від точки 2 містить деяку
кількість атомів хлору, наявність яких імовірно посприяла розвитку корозійного
процесу.
Виходячи
з відмінностей у хімічному складі приповерхневого об’єму пластин Ст08пс, можна
прийти до висновку, що інгібітор корозії МІК-8 на металевій поверхні, утворює
досить щільний хемосорбційний шар. Однак присутність інгібітору МІК-8 не
попереджує адсорбцію у приверхневому об’єму металу корозійно активних агентів
середовища.
Проти
корозійна дія інгібітора МІК-8 не обмежується ізоляційним ефектом, а також має
електронну складову.
На
диференціальному загальних електронних спектрах у ділянці виходу істинно
вторинних електронів спостерігається максимум. З положення максимуму на
електронному спектрі визначено роботу виходу електрона для кожної з точок, що
досліджувались. Так, у точках №1, №2, №3 значення роботи виходу відповідно
рівне 4.3, 5.0, 5.3 еВ.
Беручи
до уваги значення роботи виходу електрону із Ст08пс у точках №1, №2, №3 можна
констатувати, що при адсорбції МІК-8 на металевій поверхні робота виходу
електрона підвищується. Підвищення роботи виходу електрона з металу характерне
для інгібіторів електроноакцепторним типом дії.
Для точки №3 проводили дослідження зміни концентрації встановлених
елементів від глибини занурення у приповерхневий об’єм. Встановлено, що із
заглибленням у приповерхневий об’єм металу концентрація концентрація корозійних
агентів (сірки, хлору) та азоту зменшується, а концентрація заліза
підвищується. Залежність інтенсивності сигналу кисню від глибини занурення у
при поверхневий об’єм має максимум на глибині 100А, що очевидно пояснюється
підвищенням концентрації кисню у складі гідрофільних груп, які максимально
споріднені до поверхні металу. Концентрація вуглецю від глибини занурення у при
поверхневий об’єм також зменшується причому дана залежність характеризується
наявністю перелому на глибині 100А. За характером зміни концентрації вуглецю та
кисню від глибини занурення у приповерхневий об’єм можна встановити, що в
умовах випробувань, на поверхні Ст08пс, зформувався хемадсорбціний шар
інгібітора МІК-8 з приблизною товщиною - 100А.
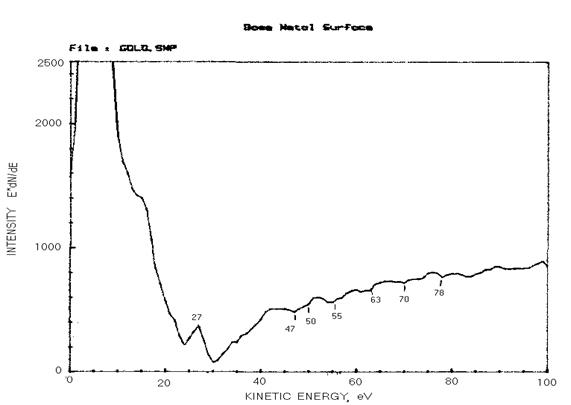
Рис. Загальний електронний
спектр, знятий для поверхні Ст08пс.
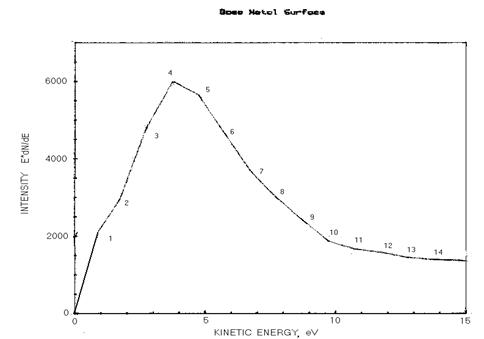
Рис. Загальний електронный спектр вторинних
електронів знятий для поверхні Ст08пс. (ділянка максимального виходу
електронів)
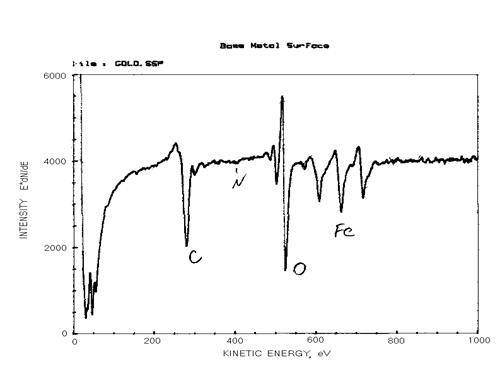
Рис. Загальний вигляд характеристичних
сигналів на Оже спектрі поверхні пластини Ст08пс, яка не була оброблена
інгібітором корозії.
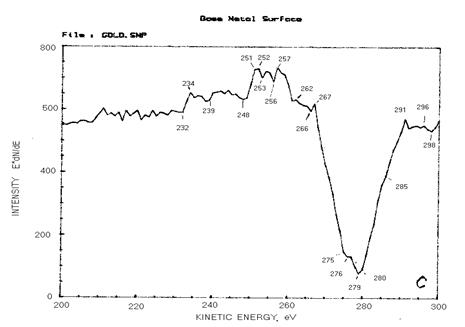
Рис. Характеристичний
сигнал вуглецю на Оже спектрі поверхні пластини Ст08пс.
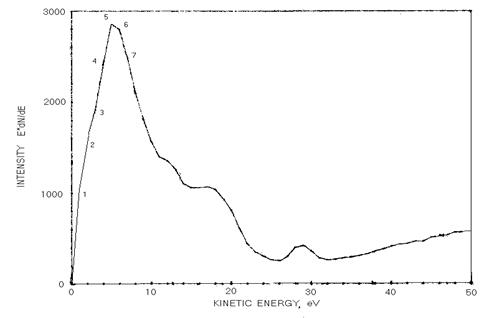
Рис.
Загальний електронный спектр вторинних електронів знятий для поверхні
Ст08пс, що містить інгібітор корозії МІК-8. (ділянка максимального виходу
електронів)
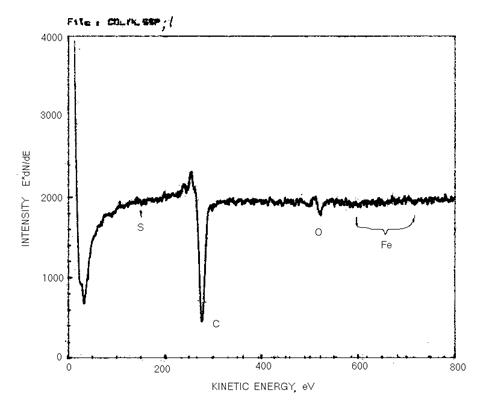
Рис. Загальний вигляд характеристичних
сигналів на Оже спектрі поверхні пластини Ст08пс, яка була оброблена
інгібітором корозії, (після випробування у електроліті).
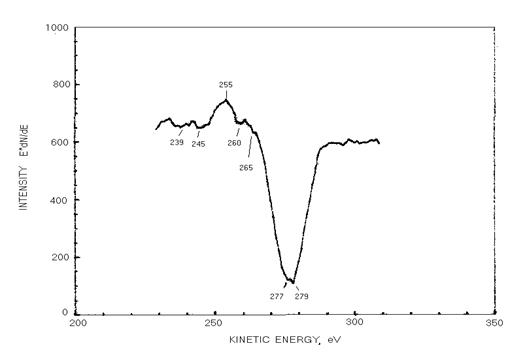
Рис. Характеристичний сигнал вуглецю на
Оже спектрі поверхні пластини Ст08пс.
, яка була оброблена інгібітором корозії МІК-8, (після
випробування у електроліті).
Рис. Характеристичний
сигнал кисню на Оже спектрі поверхні пластини Ст08пс.
, яка була оброблена
інгібітором корозії МІК-8, (після випробування у електроліті).
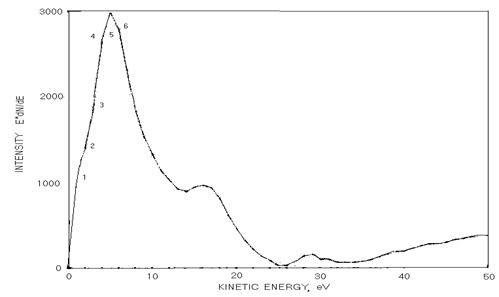
Рис.
Загальний електронный спектр
вторинних електронів знятий для поверхні Ст08пс, що була оброблена
інгібітором корозії МІК-8. (ділянка максимального виходу електронів) (точка
зародження корозії)
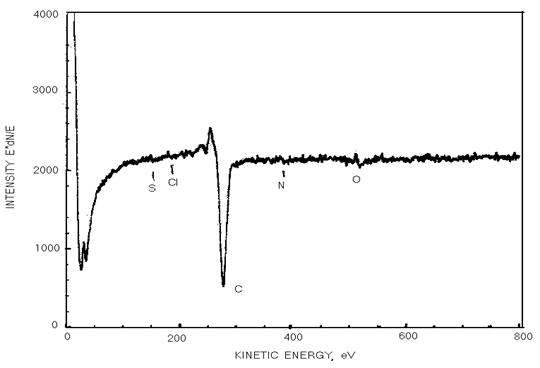
Рис. Загальний вигляд характеристичних
сигналів на Оже спектрі поверхні пластини Ст08пс, яка була оброблена
інгібітором корозії, (після випробування у електроліті) (точка зародження
корозії).
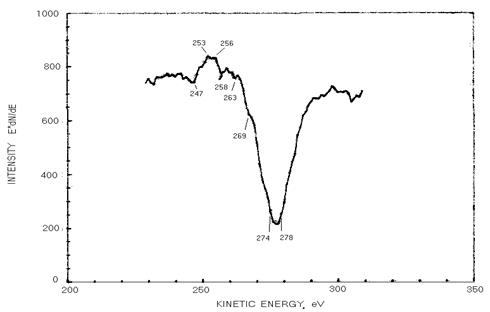
Рис. Характеристичний сигнал вуглецю на
Оже спектрі поверхні пластини Ст08пс.
, яка була оброблена інгібітором корозії МІК-8, (після
випробування у електроліті)
(точка зародження корозії).
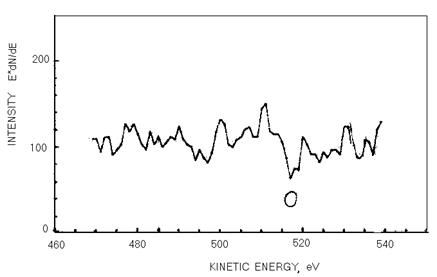
Рис. Характеристичний сигнал кисню на
Оже спектрі поверхні пластини Ст08пс,
яка була оброблена інгібітором корозії МІК-8, (після
випробування у електроліті),
(точка зародження
корозійного).
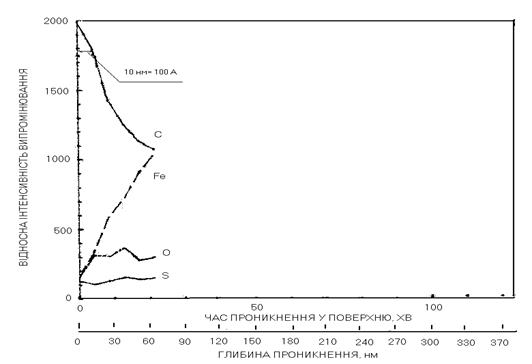
Рис . Зміна інтенсивності випромінювання елементів поверхні
Ст08пс від глибини проникнення, у об’єм металу (роспилювання поверхневого шару Ar+)
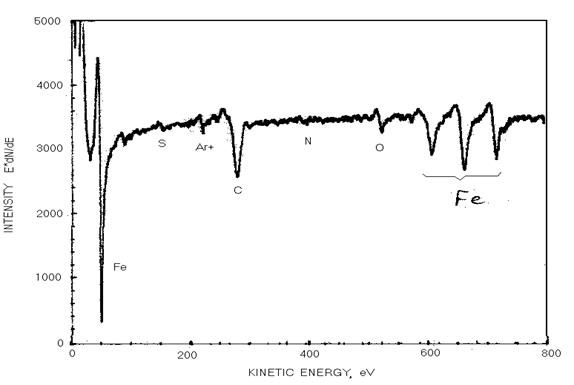
Рис. Загальний вигляд характеристичних
сигналів на Оже спектрі поверхні пластини Ст08пс, що
оброблялась інгібітором МІК-8 та знаходилась у електроліті, після спилення
верхнего прошарку товщиною 60 нм.
6.2
Дослідження гідролітичних властивостей інгібітора МІК-8.
Схильність інгібітору МІК-8, до
гідролізу досліджували за зміною рН водної витяжки. Зміна значення рН водної
витяжки від часу стояння емульсії вода - інгібітор МІК-8 зображена на рис. 1.
Рис.1. Зміна значення рН водної витяжки інгібітора
МІК-8
з плином часу.
Встановлено, що при взаємодії
інгібітора з водою значення рН останньої, за перші 5 діб, підвищується з 6,8 до
7,8. Починаючи з 10 доби і протягом наступного часу спостерігається зменьшення
значення рН водної витяжки інгібітора МІК-8 з 7,8 до 7,3.
Підвищення значення рН води при
її контакті з інгібітором МІК-8 можна пояснити наявністтю в інгібіторі
аміноспиртів, що не вступили в реакцію, а також гідролізом складових
інгібітору, зокрема естерів триетаноламіну (1), (див. схема 5).
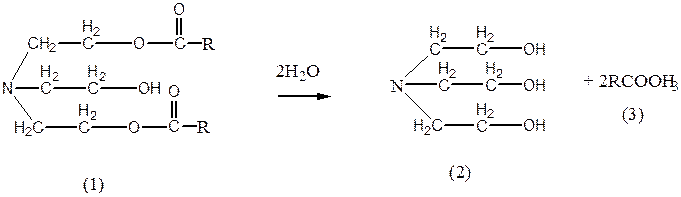
Де R=алкіл, алкеніл
Схема
. 5
Зменшення
значення рН середовища, очевидно пов’язано з поглинанням вуглекислого газу з
атмосфери.
Реація між естерами інгібітора
МІК-8 та водою, з утворенням ефективного водорозчинного інгібітору корозії
чорних металів - триетаноламіну (2) (схема 5)[216-219], очевидно лежать
в основі механізму дії МІК-8 у насичених водою середовищах. При нанесенні
консерваційних олив, що містять інгібітор МІК-8, на вологі металовироби, окрім
витіснення та поглинання вологи з металевої поверхні, за рахунок виділеного
триетаноламіну, відбувається нейтралізація вологи яка знаходиться в
недоступних, для ефективної взаємодії з оливою, порах в при поверхневому об’ємі
металу (див рис.)
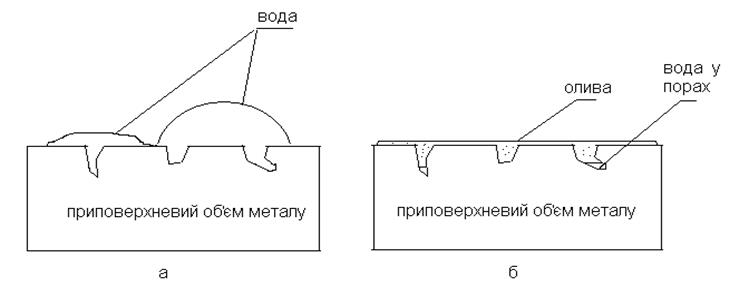
Рис.
5 Стан вологої металевої поверхні
а- до нанесення консерваційної
оливи
б- після нанесення
консерваційної оливи
6.3
Дослідження систем мінеральна олива – інгібітор корозії МІК-8.
6.3.1
Дослідження захисної здатності нафтових олив
Для встановлення
закономірностей впливу базової оливи на захисну здатність консерваційних олив,
проводили дослідження захисної здатності доступних нафтових олив.
Нафтопереробним
комплексом виробляється досить широкий асортимент різноманітних базових олив,
що являють собою очищені дистилятні оливи або суміш дистилятних та залишкових
олив. До цієї групи базових олив можна також віднести регенеровані різними
способами оливи. Окрім відомих індустріальних олив, за ГОСТ 20799-88 в Україні
Львівським ДНПЗ випускаються дистилятні оливи серії ОР (ОР-1, ОР-2, ОР-3).
В основному для нафтових олив нормуються фізико-хімічні параметри (в’язкість,
колір, температура спалаху, температура застигання, кислотне число,
стабільність проти окиснення та ін.).
Крім того, оливи однієї марки, вироблені з різних нафт та
із застосуванням різних методів очищення (АВТ-перегонка, селективне очищення,
депарафінізація, контактне очищення [5, 220]), також відрізняються хімічним
складом.
Суттєва
відмінність у вуглеводневому складі може впливати як на функціональні так і на
захисні властивості олив.
Випробування
олив проводились за методиками ГОСТ 9.054-75. (за постійного занурення до
електроліту, дії соляного туману, та у камері підвищеної вологості)
У
таблиці 1 наведено результати випробувань захисної здатності олив
індустріальної групи відносно пластин із сталі 08Пс
Таблиця 1. Результати випробувань олив
індустріальної групи
№ |
ОЛИВА |
Кінематична в′язкість оливи при 22 оС мм2/с |
Результати випробувань
|
|
Випробування у електроліті. |
Камера вологості (5 діб, 46 оС), вражена поверхня, % |
Камера сольового туману (2 доби),
вражена поверхня, % |
Відсоток поверхні, що вражена
корозією через 60 годин, % |
Змінення маси пластини г/см2
після видалення іржі через120 годин. |
Ступінь захисту металу |
1 |
Контрольна пластина |
100 |
7,89 |
- |
100 |
100 |
2 |
І-5А |
20
|
90 |
5,26 |
33,3 |
25 |
95 |
3 |
І-8А |
30,6
|
75 |
4,5 |
43 |
15 |
94 |
4 |
І-12А |
53
|
76 |
4,9 |
39,2 |
13 |
95 |
5 |
І-20А |
80
|
60 |
4,7 |
38,2 |
18 |
92 |
6 |
І-30А |
130,2
|
32 |
4,5 |
42 |
5 |
98 |
7 |
І-40А |
197
|
38 |
4,4 |
44 |
55 |
93 |
8 |
І-50 |
286,7
|
30 |
4,1 |
48 |
60 |
89 |
|
|
|
|
|
|
|
|
|
Згідно з
даними наведеними в табл. 1, з підвищенням в′язкості в ряду олив І-5А,
І-12А, І-20А, І-30А, І-40А, І-50А має місце тенденція до покращення захисних
властивостей, що можна пояснити зростанням когезії і зміцненням захисної плівки
оливи, причому для різних умов випробувань змінення ступеня захисту оливи із
зміненням в’язкості є різною. Так, результати випробувань захищених оливами
пластин у камері сольового туману свідчать, що олива з найбільшою в′язкістю
І-50А має значно вищий захисний ефект в порівнянні з оливами нижчої в’язкості.
Таку різницю між захисною дією олив можна пояснити тим, що в умовах випробувань
тільки олива І-50А створює більш менш суцільну захисну плівку. Судячи з даних
випробувань у камері вологості, залежність ефективності захисту від в’язкості
олив має оптимум (олива І-30А), що можна пояснити утворенням оптимального
балансу енергій когезії адгезії в системі олива-метал-водяний конденсат. За
методом випробування в електроліті спостерігається чітка кореляція між
в’язкістю та ступенем захисту .
Досліджено також вплив вуглеводневого складу на
захисні властивості олив. Для досліджень були взяті оливи серії ОР, що містять
у своєму складі значну кількість бензольних, нафталінових, три- та
тетрациклічних ароматичних сполук. Так, в оливах ОР вміст цих сполук досягає 40% [221, 222].
Результати випробувань захисних властивостей олив з
підвищеним вмістом ароматичних сполук наведено у таблиці 3.
Таблиця
3
Результати випробувань олив з підвищеним
вмістом ароматичних сполук.
№ |
ОЛИВА |
Сумарний вміст конденсо- ваних
ароматичних сполук,%. |
Кінемати-чна в′язкість
оливи при 22 ˚С, мм2/с |
Результати випробувань
|
Випробування у електроліті. |
Камера вологості (5 діб, 46 оС), вражена поверхня, % |
Камера сольового туману (2 доби),
вражена поверхня,% |
Відсоток враженої поверхні за 60
годин,% |
Змінення маси пластини після видалення іржі. г/м2 |
1 |
Контрольна пластина |
- |
- |
7,89 |
100 |
100 |
2 |
І-20А |
6,4 |
80 |
60 |
4,9 |
18 |
92 |
3 |
Техн.А |
10,8 |
58 |
48 |
4,9 |
12 |
12 |
4 |
ОР-1 |
18,6 |
39,3 |
71 |
5,08 |
5 |
14 |
5 |
І-20 рег. РНХП |
18,8 |
62 |
14 |
2,66 |
15 |
25 |
6 |
ОР-3 |
27,8 |
952 |
1,5 |
0,15 |
30 |
4 |
7 |
ЄСО |
55,7 |
448 |
4 |
1,08 |
25 |
19 |
За даними випробувань у камері вологості найкращі захисні
властивості виявились у оливи ОР-1, незважаючи на порівняно невисоку
в′язкість та низький вміст ароматичних речовин. А високов′язкі
оливи з підвищеним рівнем ароматичних сполук виявили низький рівень захисту. У
камері сольового туману, при дослідженні олив з підвищеним умістом конденсованих
ароматичних сполук найкращі захисні властивості виявились у оливи ОР-3, а
найгірші - регенерованої оливи І-20 РНХП.
У
випадку випробування електролітом спостерігається підвищення захисних
властивостей оливи із збільшенням сумарного вмісту конденсованих ароматичних
сполук. Так захисні властивості
олив ОР-3, ЕСО, ОР-1 приблизно співвідносяться між собою як 1,0 : 0,73 : 0,41.
Вплив
конденсованих ароматичних речовин на захисні властивості оливи можна пояснити
їх адсорбцією на поверхні металу [223]. Але судячи з даних експериментів,
достатньо тривка плівка утворюється тільки у середовищі електроліту. Цей ефект
можна пояснити тими відомими фактами, що структуровані особливим чином
конденсовані ароматичні системи набувають споріднених до металів властивостей, наприклад,
електропровідність [224]. Відомим є той факт, що деякі органічні
напівпровідники, нанесені на поверхню металу, є ефективними інгібіторами
корозії. Також з літературних джерел відомо, що адсорбовані на металі речовини
структуризуються і набувають відмінних від попереднього (не адсорбованого)
стану фізичних властивостей [15] . Для структурованих кристалів ароматичних
речовин відомо, що провідність в них виникає або підвищується у випадку
наявності забруднень або речовин—ініціаторів провідності. Так, у літературі
[224] показано значне підвищення електропровідності кристалів антрацену у
присутності розчинів NaCl, NaI+I2.
Виходячи
з літературних даних, можна припустити, що динамічно адсорбовані на поверхні
металу молекули конденсованої ароматичної речовини (наприклад, антрацену) у
полі металу структуризуються, утворюючи напівпровідні структури. Останні, маючи
спряжені подвійні зв′язки, взаємодіють з електронами металу за донорно
акцепторним, або електронним механізмом, що в свою чергу, зумовлює гальмування
електрохімічних корозійних процесів. Причому захисний ефект олив з високим
вмістом конденсованих ароматичних речовин під час випробування в електроліті
може деякою мірою підсилюватись самим складом електроліту, зокрема, наявністю у
його складі NaCl.
Для більш детального вивчення впливу концентрації
ароматичних речовин у оливі на її захисні властивості були створені модельні
композиції сумішей олив із різним сумарним вмістом ароматичних вуглеводнів.
На
рис. 3 наведено залежність захисних властивостей модельних композицій від
сумарного вмісту конденсованих ароматичних сполук при випробуванні в
електроліті.
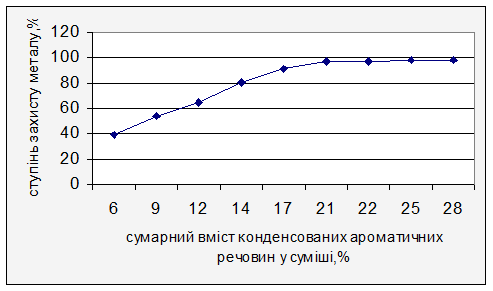
Рис.3. Залежність
ступеня захисту поверхні металу в електроліті від сумарного
вмісту конденсованих
ароматичних речовин у оливі.
З
рис 3. видно, що залежність ступеня захисту олив від концентрації ароматичних
речовин має асимптотичний характер. Так, у проміжку сумарного вмісту
конденсованих ароматичних речовин 3-12% ступінь захисту рівномірно
підвищується. При вмісті ароматичних речовин понад 14% захисні властивості
підвищуються менш помітно. Такий характер залежності можна пояснити збільшенням
концентрації адсорбованих, на поверхні металу, активних речовин із збільшенням
їх частки у суміші до утворення плівки адсорбату.
Судячи
з даних випробувань, процеси, що відбуваються під час захисту металів
багатокомпонентними вуглеводневими сумішами з різною в′язкістю
вуглеводнів, є досить складними, а сумарний ефект захисту є результатом
комплексної дії різних факторів.
Проведені
дослідження впливу характеристик нафтових олив на їх захисні властивості щодо
сталі показали, що захисний ефект олив залежить від їх фізико-хімічних
властивостей та вуглеводневого складу.
Таким
чином при розробленні нових консерваційних олив необхідно враховувати
вуглеводневий склад та фізико-хімічні властивості базових олив.
6.3.2 Дослідження впливу вуглеводневого складу базової
оливи на захисну здатність консерваційних, що містять МІК-8
Досліджували
вплив вуглеводневого складу базових олив на захисну здатність консерваційних
олив створених на основі інгібітора МІК-8.
На
основі олив І-20А, І-12А, ОР-1, ОР-3 готувались модельні композиції, що мали
приблизно однакові значення кінематичної вякості але різний вміст конденсованих
ароматичних сполук та інгібітору корозії МІК-8. Для одержаних композицій,
відносно Ст08пс в умоах камери сольового туману, визначали захисну здатність. Вплив
інгібітору МІК-8 на захисну здатність композицій з різним вмістом конденсованих
ароматичних сполук наведено на рис 1.
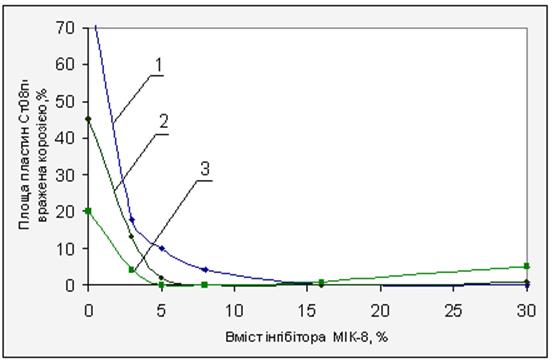
Рис 1. Вплив інгібітору
МІК-8 на захисну здатність оливах що містять
1-
3% конденсованих ароматичних сполук (І-20А);
2-
10% конденсованих ароматичних сполук;
3-
20% конденсованих ароматичних сполук.
Встановлено, що із підвищенням
сумарного вмісту конденсованих ароматичних сполук (до 10%) захисна здатність консерваційних
олив, при вмісті інгібітора корозії МІК-8 2-17%, зростає (Рис. 1., крива 1,2).
Подальше підвищення вмісту ароматичних сполук або інгібітору корозії не
призводить до суттєвого підвищення, або може призвести до падіння захисної
здатності консерваційних олив.
6.3.3 Дослідження фізикохімічних параметрів базової
оливи на захисну здатність консерваційних, що містять МІК-8
Важливим
фізикохімічним параметром консерваційних олив є в’язкість. Цей параметр може
суттєво вплинути на технологічні аспекти застосування, а також на захисну
здатність консерваційної оливи.
З погляду економії
матеріальних та енергетичних ресурсів на стадіях консервації та розконсервації
металовиробів бажане застосовування олив з мінімальною в’язкістю, що
пояснюється зручністтю нанесення (особливо у випадку деталей із складною
конфігурацією) меншою витратою та легшим змиванням.
Вязкість
оливи також впливає і на захисну здатність консерваційної оливи. Відомо, що
плівки які утворюються на металевій поверхні, в більшості випадків мають
складну “сендвічну” будову. В основі захисної плівки лежить первинний
адсорбційний шар інгібітора на якому, в залежності від складу консерваційної
оливи розміщуються вторинні прошарки захисної плівки, поступово підвищуючи її
гідрофобність. Надійність такої плівки (а тому і захисна ефективність
консерваційної оливи) залежить як від цілісності первинного адсорбційного
прошарку, так і від міцності вторинних шарів, які залежать від вязкості олив.
В той же час , для швидкого утворення адсорбційного прошарку інгібітору на
металевій поверхні, молекули останнього повинні володіти достатньою дифузією у
оливному середовищі, що також лімітується в¢язкістю
оливи.
Тому, з
погляду забезпечення максимальної захисної ефективності, оптимальне значення
в’язкості консерваційної оливи може змінюватись в широких межах і залежить від
природи металу, хімічної будови та властивостей інгібітору корозії, технології
консервувації, а також умов зберігання та перевезення металовиробів [5, 14-16].
В більшості
випадків результуюча в’язкість консерваційних олив визначається базовими
компонентами, в якості яких часто виступають індустріальні оливи.
При
дослідженні впливу в’язкості базової оливи на захисну ефективність інгібітору
МІК-8 було взято індустріальні оливи різної в’язкості (ГОСТ 20799-88).
Дослідженнями встановленно, що
при переході від індустріальних олив з низькою в’язкістю І-5А, І-8А (Рис 2,
крива 1, 2, 3) до більш в’язких І-12А, І-50А (Рис 2, крива 3, 4), захисні
властивості композицій, що містять інгібітор МІК-8. Так, при концентрації МІК-8
10% в оливі І – 5А ступінь враження поверхні пластин Ст08пс через 24 год.
становить 27% , в оливі І- 8А - 15%, в оливі І-12А -6%, І-40А - 2%.
Рис 2. Захисна здатність інгібітору МІК-8 у оливах 1) І –5А;
2) І – 8А; 3) І – 12А; 4) І-40А, І- 50А (визначена відносно Ст08пс в умовах
камери сольового туману, за 24 год.)
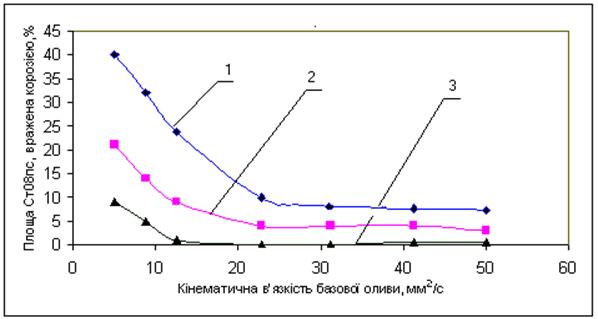
Рис 5. Залежність захисної здатності оливних розчинів інгібітору МІК-8 1) 3%, 2) 8% 3)
15% від в’язкості базового компоненту, визначена відносно Ст08пс в умовах
сольового туману, за 24 год.
При дослідженні захисної
здатності розчинів інгібітора МІК-8 в індустріальних оливах різної в’язкості з
постійною концентрацією інгібітора, встановлено, що із підвищенням в’язкості
базової оливи, захисна здатність розчину підвищується до певного постійного
значення. Причому, із збільшенням вмісту інгібітору, значення кінематичної
в’язкості, починаючи з якої захисна здатність приймає приблизно постійне
значення, зменшується див. рис.5.
6.3.4
Вплив інгібітору МІК-8 на швидкість корозії
Концентрація МІК-8
в оливі І-20 впливає на кінетику корозійного враження пластин Ст08пс, що, в
умовах випробуваннь, були захищені оливами відповідного складу. Так, при
використанні 3% композицій швидкість корозії Ст08пс (як в умовах електроліту
так і в умовах камери сольового туману) є значною, і супроводжується
зародженням декількох центрів корозії, що свідчить про несформованність
захисного шару в цьому випадку Рис 3,4, крива 1. З підвищенням концентрації
інгібітора в оливі І-20А до 8% швидкість корозії значно зменьшується, а на
пластинах Ст08пс спостерігається, як правило кількість центрів корозії не
нарощується Рис 3,4 крива 2. При захисті Ст08пс 15% розчином МІК-8 у оливі
І-20А, в умовах випробуваннь спостерігалась низька корозійна активність, а
причому після зародження корозивного центру, корозія майже припинялась Рис 3,4
крива 3.
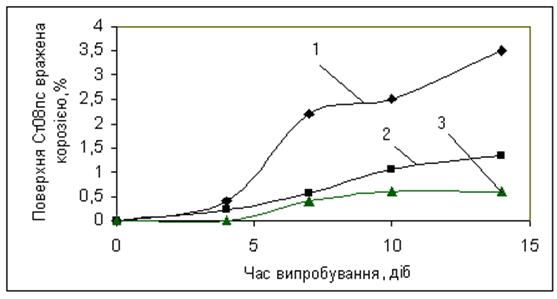
Рис
3. Кінетика
корозійного враження пластин Ст08пс, що
захищені оливою І-20А із вмістом інгібітору МИК-8: 1) 3% , 2) 8%, 3) 16%. (При
випробуваннях у електроліті)
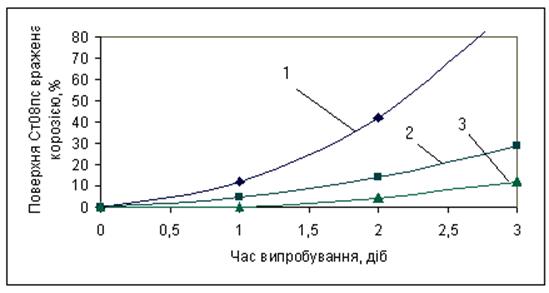
Рис
4. Кінетика корозійного враження
пластин Ст08пс, що захищені оливою І-20А із вмістом інгібітору МІК-8: 1) 3%, 2)
10%, 3) 20%. (При випробуваннях в умовах сольового туману)
Таким чином, для олив
на основі нового інгібітора МІК-8 встановлено залежність ступіня враження
поверхні Ст08пс, від концентрації інгібітора, за різний проміжок часу
випробувань, що є основою при розробці консерваційних із заданим ступенем
захисту.
6.3.5
Дослідження впливу температури на оливні системи інгібітора МІК-8.
При застосуванні консерваційних
олив, для захисту металовиробів, що зберігаються в умовах підвищених температур
важливою властивісттю є теплостійкість покриття. З підвищенням температури
зменшується когезійно- адгезійна взаємодія в оливному покритті, що може
призвести до сповзання шарів оливної плівки та відповідно зменшення захисної
здатності. Вивчали вплив концентрації інгібітора корозії на термічну
стабільність плівки оливи, що містить інгібітор МІК-8.
Дослідження проводили шляхом
визначення захисної здатності, в умовах камери сольового туману відносно
пластин Ст08пс, розчинів з різною концентрацією інгібітора МІК-8 у оливі І-20А
після теплової обробки (Рис. , Крива 2). Теплову обробку проводили шляхом
витримування пластин Ст08пс з нанесеним покриттям в сушильній шафі при
температурі 70 оС протягом 35 годин. Паралельно визначали захисну
здатність розчинів інгібітора МІК-8 у оливі І-20А відносно Ст08пс, що не
проходили теплову обробку (Рис. , Крива 1).
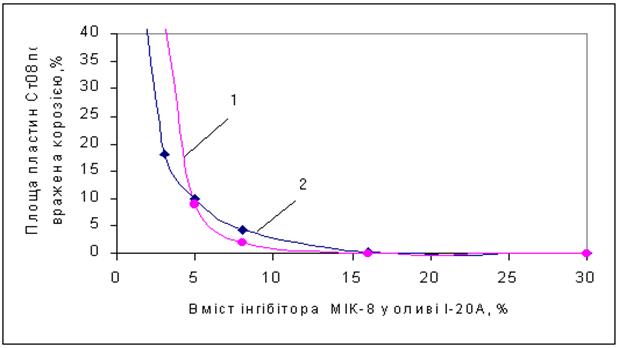
Рис.
Вплив концентрації інгібітора МІК-8 на захисну здатність оливи І-20А при різних
температурах. 1) при температурі 70 oC; 2) при температурі 36 oC.
Як свідчать результати термічна
стійкість покриттів на основі МІК-8 залежить від концентрації останнього. Так
при використанні оливних розчинів з концентрацією інгібітору < 6% ступінь
корозійного враження пластин Ст08пс, що випробовувались при 70оС є
вищим ніж пластин, які випробовувались при 35 оС. При використанні
оливних розчинів з концентрацією інгібітору 8-15% навпаки, пластини Ст08пс,
які випробовувались при 70оС були порівняно менше вражені корозією.
Такі результати, очевидно, пов’язані з тим, що відносно низькій концентрації
інгібітора в плівці оливи останній, при сповзанні оливної плівки, не встигає
хемасорбуватись на всій металевій поверхні при цьому утворюється порівняно
тонкий пористий захисний шар. У випадку достатньої концентрації інгібітора в
оливній плівці, не дивлячись на сповзання оливи, під дією підвищеної
температури, з вищою швидкістю (порівняно з пластина нами, що не піддавались
термічній обробці) утворюється більш суцільний хемосорбцій шар.
6.4 Дослідження взаємного впливу інгібітора МІК-8 та
оливорозчинних додатків на основні властивості консерваційних олив.
6.4.1 Дослідження впливу загущуючи додатків на
основні властивості консерваційних олив, що містять інгібітор корозії МІК-8
Консерваційні
оливи, окрім оливорозчинних інгібіторів корозії можуть містити: загущуючі,
протизносні, миючі, антипінні, адгезійні, біостатичні та ін. додатки. Характер та рівень взаємного впливу додатків на властивості
консерваційних олив визначається їх хімічним складом. Для застосування нових
інгібіторів корозії, створених на основі похідних карбаміду, в розробці
консерваційних олив, необхідно дослідити та враховувати вплив інших компонентів
оливи на її основні властивості.
Інгібітор МІК-8, маючи значення
кінематичної в’язкості в межах 60-74 мм2/с (при 50оС)
підвищує в’язкість індустріальних олив які мають менше значення в’язкості рис.
6.
Рис.6 Вплив вмісту інгібітора на значення кінематичної
вязкості
індустріальних олив 1) І- 40А, 2) І- 20А, 3) І- 8А.
Досліджувався вплив деяких
загущуючих додатків на захисні властивості композицій індустріальних нафтових
олив І – 5 А, І – 20А з інгібітором корозії МІК-8 (4%).
Встановлено, що характер впливу
загусника на захисну здатність композицій визначається його фізикохімічними
властивостями та хімічною будовою.
Зміна захисної здатності
консерваційних олив від концентрації поліізобутилену (ПІБ) (Мrср=300-400
а.о.м.) характеризується наявністю оптимуму, положення якого визначається
вязкістю та хімічним складом базової оливи. У випадку загущення композицій на
основі І-20А оптимальний вміст ПІБ складає 4-5%, а при додаванні ПІБ до оливи
на основі І-5А максимуму захисної здатності композицій відповідає концентрація
ПІБ 12-16%. Аналогічний характер впливу спостерігався і у випадку застосування
в якості загусника синтетичного каучуку, сополімерів етилену пропілену тощо.
Підвищення
вмісту полімерних загущуючих додатків, хімічна структура яких містить полярні
функціональні групи (наприклад поліметилметакрилат ПМА-Д, рис.4), призводить до
прямопропорційного підвищення захисної здатності олив на основі І-5А (враження
поверхні корозією зменшується на 60 %) та І-20А (враження поверхні корозією
зменшується на 7 %). Причому ефективна робоча концентрація таких загусників
складає 3-4 %, подальше підвищення їх концентрації призводить до втрати
текучості композицій.
Різний характер впливу, відмінних
за хімічним складом, полімерних загущаючих додатків, очевидно можна пояснити
різною їх спорідненістю до металевої поверхні, а також властивістю
структурувати обємні та поверхневі прошарки захисної плівки консерваційної
оливи. Так із введенням ПІБ (в кількості до 5%) підвищується ступінь
структурування вторинних прошарків захисних плівок, що призводить до покращення
захисної здатності композицій. З подальшим введенням ПІБ підвищується
структурованість об(єму оливи, в якому затримується деяка кількість молекул
інгібітору, що призводить до зменьшення концентрації молекул ІК на поверхні
металу.
Наявність в хімічній структурі
загусника полярних функціональних груп, очевидно наділяє його молекули
властивісттю структурувати не тільки вторинні, а й первинні прошарки захисної
оливної плівки, що підвищує її міцність і покращує захисну здатність в цілому.
Вуглеводневі загущуючі
додатки (бітум, петролатум) також покращують захисну здатність композицій (в
більшій мірі на основі оливи І-5А, в меньшій мірі на основі І-20А). Однак дані
додатки мають обмежену розчинність в оливах чим обмежується їх максимальна
робоча концентрація до 5% у композиціях. Механізм дії вуглеводневих загущуючих
додатків очевидно зводиться до осідання на металевій поверхні, при наближенні
їх вмісту в оливі до межі насичення та створення додаткового гідрофобного
екрануючого прошарку (Рис. 5 крива 1, 2).
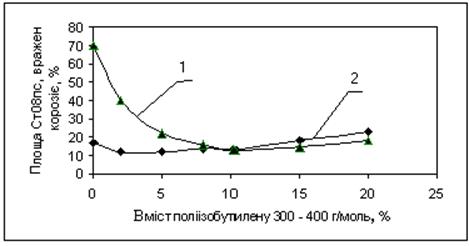
Рис. 3. Залежність захисних властивостей консерваційної оливи, приготованої на основі
базової оливи 1) І-5А, 2) І-20А, і 4% МІК-8 від вмісту ПІБ (при випробуванні у
камері сольового туману відносно Ст08пс, 24 год.)
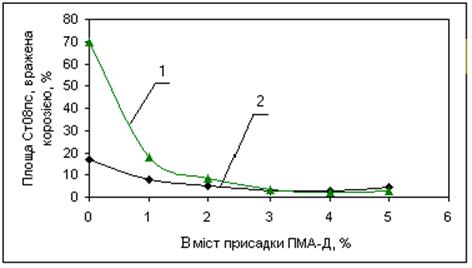
Рис.
4. Залежність захисних властивостей консерваційної
оливи приготованої на основі базової оливи 1) І-5А, 2) І-20А, і 4% МІК-8 від
вмісту додатку ПМА-Д. (при випробуванні у камері сольового туману відносно
Ст08пс, 24 год.)
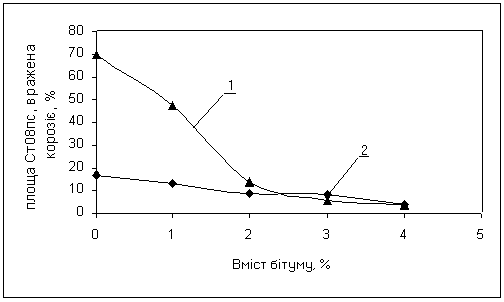
Рис. 5. Залежність захисних властивостей консерваційної оливи, приготованої на основі
базової оливи 1) І-5А, 2) І-20А, і
4% МІК-8 від вмісту бітуму.
(при
випробуванні у камері сольового туману відносно Ст08пс, 24 год.)
6.4.2 Дослідження впливу сульфонатних додатків на
властивості консерваційних олив, що містять інгібітор корозії МІК-8
Як показує
аналіз патентної літератури до складу консерваційних олив окрім інгібіторів
корозії входять додатки різної функціональної дії, зокрема високолужні
сульфонатні додатки, які сприяють підвищенню захисної здатності консерваційних
олив у наслідок прояву синергетичних ефектів з інгібіторами корозії. Попередньо встановлено, що МІК-8 є інгібітором
корозії електроноакцепторної дії. З літературних джерел відомо, що
електроноакцепторні інгібітори корозї проявляють сінергізм захисної здатності з
оливорозчинними додатками сульфонатного типу [14- 16].
Проводили дослідження впливу сульфонату кальцію на
захисну здатність ОІК МІК-8 у складі композицій на основі оливи І-20А.
Виходячи з того, що
естери триетаноламіну та олеїнової кислоти (як інгібітори корозії
електроноакцепторної дії) проявляють сінергізм захисної здатності з
високолужними сульфонатними додатками, для порівняння досліджували захисну
здатність композицій на основі суміші діолеату триетаноламіну та додатку С-150.
Встановлення
синергетичних ефектів проводили шляхом визначення захисної здатності 8%-их
розчинів суміші додатків МІК-8 і С-150 та діолеату триетаноламіну і С-150.
Розчини
додатків готувались шляхом перемішування визначеної кількості додатків та оливи
І-20А при температурі 65-70 оС протягом 30-35 хв.
Захисну
здатність оливних розчинів оцінювали відносно Ст08пс відповідно до ГОСТ 9.054
методом 3- у камері сольового туману, методом 4- в умовах постійного занурення
у електроліт.
Встановлено,
що відносно Ст08пс, макисмум захисних властивостей для композицій на основі
С-150, при випробуваннях у камері сольового туману знаходиться при вагових
співвідношеннях діеолеат ТЕА : С-150 = 2 : 8 – 3 : 7 ; МІК - 8 : С-150 = 8 : 2
– 7 : 3 (мал 4. 1, мал 4. 3). При випробуванні в умовах постійного занурення у
електроліт макисмум захисних властивостей проявляється при значенні масового
співвідношення діолеат ТЕА : С-150 = 7 : 3 – 6 : 4 ; МІК 8 : С-150 = 8 : 2 – 7
: 3.
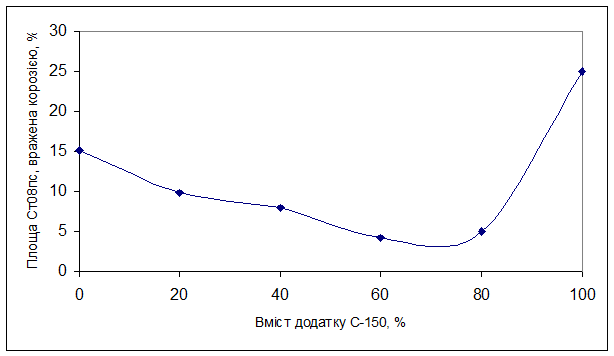
Мал. Випробування захисних властивостей оливних композицій діолеату ТЕА і присадки
С-150, в умовах камери сольового туману.
Залежність захисних властивостей 8%-их розчинів суміші
додатків в І-20А від вмісту присадки
С-150 в суміші.
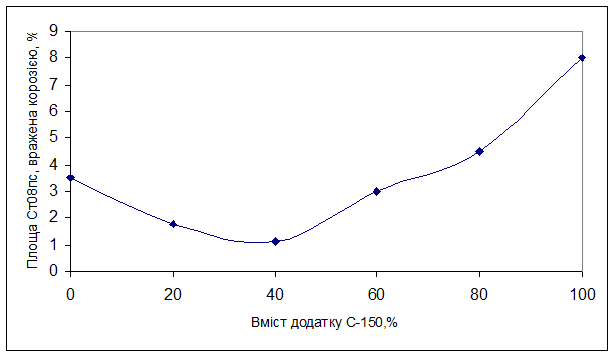
Мал. Випробування захисних властивостей оливних композицій діолеату ТЕА і присадки
С-150, в умовах постійного занурення у електроліт.
Залежність захисних властивостей 8%-их розчинів суміші
додатків в І-20А від вмісту присадки
С-150 в суміші.
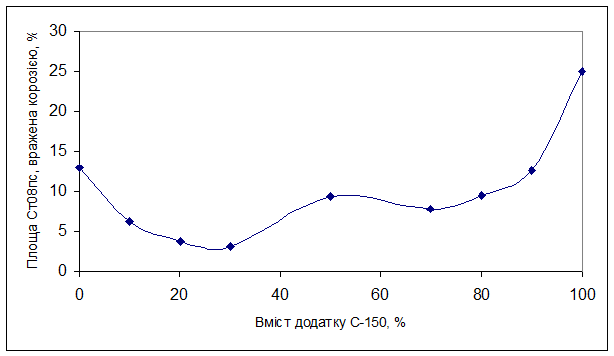
Мал. Випробування захисних властивостей оливних
композицій інгібітору МІК-8 з додатком С-150 в умовах камери сольового туману.
Залежність захисних властивостей 8%-их розчинів суміші
додатків в І-20А від вмісту присадки
С-150 в суміші.
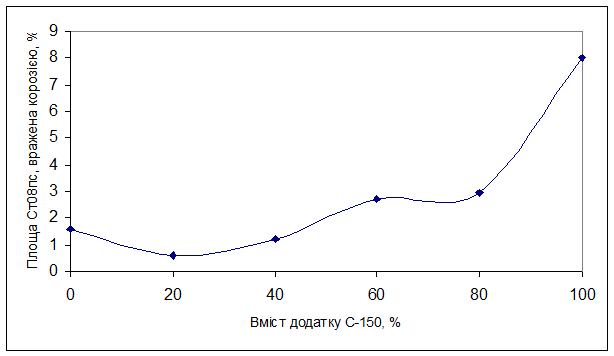
Мал. Випробування захисних властивостей оливних
композицій інгібітору МІК-8 і присадки С-150 в умовах постійного занурення у
електроліт.
Залежність захисних властивостей 8%-их розчинів суміші
додатків в І-20А від вмісту присадки
С-150 в суміші.
З результатів
випробуваннь встановлено, що поєднання 20-30% високолужного сульфонатного
додатку С-150 та 80-70% амідоестерного інгібітору корозії МІК-8 призводить до
неаддитивного покращення захисної здатності відповідних оливних композицій –
сінергізму. Причому в умовах електроліту максимальний сінергетичний ефект
проявляється при вмісті сульфонатного додатку С-150 25-30% від загальної маси
додатків, а при випробуваннях в умовах камери сольвого туману 15-25%.
Виходячи з досліджень інгібітор
МІК-8 утворює на поверхні чорних металів хемадсорбційні захисні плівки товщиною
до 100 А, підвищуючи при цьому роботу виходу електрона. За типом електронної
взаємодії з металевою поверхнею МІК-8 відноситься до електроноакцепторних
інгібіторів корозії.
Значення оптимальної
концентрації інгібітора МІК-8 у консерваційних оливах знаходиться у межах 8-15%
Значення оптимальної
кінематичної в’язкості базової оливи, для приготування консерваційних олив на
основі інгібітора МІК-8, знаходиться в межах 16-25 мм2/с (при 50 оС).
Додавання загущуючих додатків
(у кількості 2-3%), а також додатків сульфонатного типу (у кількості 20-25% від
маси інгібітора МІК-8) призводить до підвищення захисної здатності олив, що
містять МІК-8.
Окрім зазначених додатків, для
покращення стабільності проти окиснення консерваційні оливи, створені на на
основі МІК-8, можуть містити антиокисні додатки: іонол, агідол, ЦД-7, ДФ-11 і
ін, у кількості 0,1-0,5% в залежності від умов застосування оливи [185, 186].
РОЗРОБКА КОНСЕРВАЦІЙНИХ ОЛИВ НА ОСНОВІ ІНГІБІТОРУ
КОРОЗІЇ МІК-8
Для
консервування виробів з чорних металів (Ст08пс, Ст08пн, Ст08кп, Ст10, Ст20,
Ст40 і ін.) та їх зберігання в складських умовах індустріальної зони на термін
до 1-2 років, із застосуванням нового ОІК МІК-8, враховуючи результати
проведених досліджень, було розроблено оливу МАГ-11 та МАГ-15. (Таблиця ).
Таблиця
Рецептури консерваційних олив на
основі оливорозчинного інгібітора корозії МІК - 8
|
Найменування
компонету |
Нормативно-технічна документація компоненту |
Найменування оливи |
МАГ-11 |
МАГ-15мз |
Вміст додатку в
оливі, % |
1 |
МІК-8 |
|
8 |
8 – 15 |
2 |
С-150 |
|
– |
2 – 5 |
3 |
Петролатум |
|
– |
0 – 2 |
4 |
ПІБ (Мrср =300-400) |
|
2,0 |
– |
5 |
Агидол, Агидол-2 |
|
0,1 |
0,2 |
|
Компонент базової оливи |
|
Базова олива до
100% |
1 |
І-12А |
|
50 –100 |
– |
2 |
І-20 А |
|
50– 100 |
100 |
3 |
ПМС-200 А |
|
0,05 |
0,05 |
Таблиця
Характеристики
консерваційних олив МАГ-11
№ |
Показник |
Значення
показника |
Метод випробування
|
1 |
В’язкість
кінематична при 50оС, мм2/с |
18 – 20 |
ГОСТ 33 |
2 |
Зола
сульфатна, % |
0,15 – 0,2 |
ГОСТ 12417 |
3 |
Кислотне
число, мгКОН/г |
1,2 – 2,2 |
ГОСТ 11362 |
4 |
Температура
спалаху, оС, не більше |
180 |
ГОСТ 4333 |
5 |
Густина,
кг/м3 , в межах |
880 – 920 |
ГОСТ 3900 |
6 |
Захисна
здатність, оливи визначена
- в умовах з підвищеним значенням відносної вологості
і температури повітря – 40оС, 20 циклів, поверхня Ст10, вражена
корозією, %
- в умовах з підвищеним значенням
відносної вологості і температури повітря – 40 оС, при дії
сірчистого ангідриду, 24 години, поверхня Ст10, вражена корозією, %
- в умовах камери сольвого туману,
% відносно Ст10
Ст40
СЧ 18
Ст08пс
Ст08пн
ШХ-15
- в умовах постійного занурення у
електроліт, 200 годин, %
відносно Ст 10
Ст08пс
СЧ 18
- при дії
бромистоводневої кислоти, відносно Ст10,
вражена
поверхня, % |
0 – 1
0 – 3
0 – 3
0
1 – 3
0 – 1
4 – 8
2 – 5
0 – 2
1 – 2
1 – 4
0 – 2 |
ГОСТ 9.054
метод 1
метод 2
метод 3
метод 4
метод 5 |
Таблиця
Характеристики
консерваційної оливи МАГ-15мз
№ |
Показник |
Значення
показника |
Метод
випробування |
1 |
В’язкість
кінематична при 50оС мм2/с |
22 – 26 |
ГОСТ 33 |
2 |
Зола
сульфатна, % |
0,2 – 0,3 |
ГОСТ 12417 |
3 |
Кислотне
число мгКОН/г |
1,8 – 2,6 |
ГОСТ 11362 |
4 |
Температура
спалаху, оС, не більше |
180 |
ГОСТ 4333 |
5 |
Густина,
кг/м3 , в межах |
880 – 920 |
ГОСТ 3900 |
6 |
Захисна
здатність, оливи визначена
- в умовах з підвищеним значенням відносної вологості
і температури повітря – 40оС, 20 циклів, поверхня Ст10, вражена корозією, %
- в умовах з підвищеним значенням
відносної вологості і температури повітря – 40 оС, при дії сірчистого
ангідриду, 24 години, поверхня Ст10, вражена корозією, %
- в умовах камери сольвого туману,
поверхня вражена корозією, % ,
Ст10
Ст40
СЧ 18
Ст08пс
Ст08пн
ШХ-15
- в умовах постійного занурення у
електроліт, 200 годин, %
відносно Ст 10
Ст08пс
СЧ 18
- при дії
бромистоводневої кислоти, відносно, поверхня Ст10 вражена корозією,
% |
0
0 – 1
0
0
0 – 2
0
0 – 2
0 – 1
0
0
0
0 – 2 |
ГОСТ 9.054
метод 1
метод 2
метод 3
метод 4
метод 5 |
5.ТЕХНОЛОГІЯ ОДЕРЖАННЯ ОЛИВОРОЗЧИННОГО АМІДОЕСТЕРНОГО
ІНГІБІТОРУ КОРОЗІЇ МІК-8.
Як
вже встановлено, при одержанні оливорозчинного інгібітору корозії МІК-8,
основними процесами є естерифікація та амідування. Попередньо було визначено
оптимальні співвідношення реагентів, стадійність а також оптимальні значення
кислотних чисел амідо – естерного інгібітору корозії, які характеризують
хімічний склад останнього та встановлюють метод контролю технологічного
процесу.
Вибрано
каталізатори, що підвищують швидкість процесу амідування та зменшують
тривалість технологічного процесу.
Виходячи
з попередніх дослідженнь, було встановлено основні технологічні параметри і
орієнтовний час технологічного циклу одержання інгібітора МІК-8.
Розроблено
технологічну схему виробництва МІК-8(рис. 5.1).
Технологічний
процес включає наступні стадії:
1.
Підготовка сировини
2.
Одержання амідуючого агенту
3.
Одержання амідоестерного
оливорозчинного інгібітору коррозії МІК-8
1.Підготовка сировини
Стадія
включає контроль параметрів якості сировини на відповідність нормативно
технічній документації. Розігрів в’язких компонентів.
2. Одержання амідуючого агенту
Одержання
амідуючого агенту проводиться шляхом змішування карбаміду з триетаноламіном
при нагріванні до 80 оС з подальшою гомогенізацією суміші.
4.
Одержання амідоестерного
оливорозчинного інгібітору коррозії МІК-8
Одержання МІК-8 полягає в хімпроцесі між карбамідом жирними кислотами
(олеїновою та стеариновою) і триетаноламіном.
ОПИС ТЕХНОЛОГІЧНОГО ПРОЦЕСУ
Технологія
виробництва інгібітора МІК-8 є наступною:
Одержання
інгібітора корозії МІК-8 проводять наступним чином:
В
реакторі (1) з мішалкою та підігрівом проводять гомогенізацію карбаміду
та триетаноламіну.
В
реактор (2) з мірника (5) завантажують розраховану кількість
олеїнової кислоти і при перемішуванні підігрівають її до 50-70 оС.
Потім завантажують розрахункову кількість стеаринової кислоти. Перемішують
вміст реактора до однорідності. Після цього в реактор (2) з реактора (1)
поступово додають амідуючий агент ( триетанолкарбамідну суміш). Температуру
реакційної маси піднімають до 135-145 оС та витримують її протягом
2-3 год до досягнення значення кислотного числа 40-55 мгКОН/г). Після чого, при
перемішуванні, додають 1-2% каталізатору (карбонату кальцію). Піднімають
температуру до 175-185 оС та ведуть процес до досягнення кислотного
числа реакційної маси 15-19 мгКОН/г.
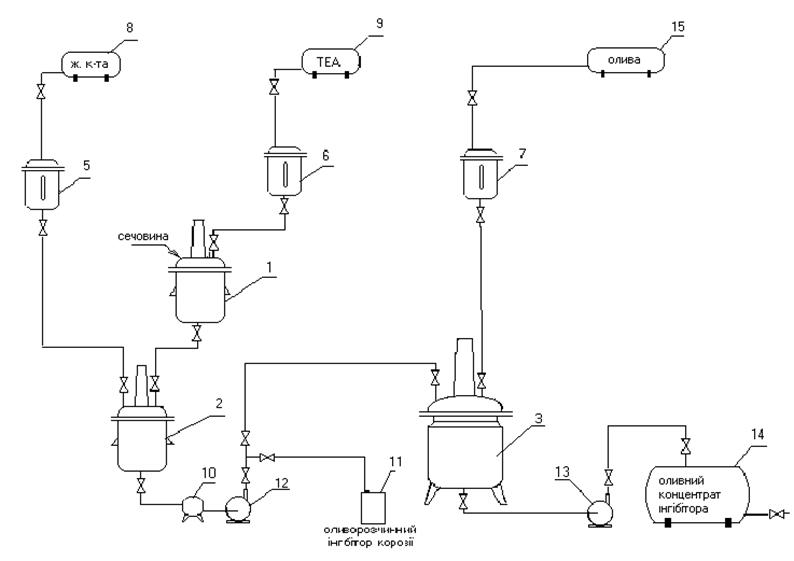
Рис. 5.1. Технологічна схема
одержання амідоестерного оливорозчинного інгібітору корозії МІК – 8. Де 5, 6,
7 – мірник для дозування відповідно триетаноламініну, олеїнової
кислоти, оливи І-20А. 1, 2, 3 – реактори відповідно для: гомогенізації
карбаміду і триетаноламіну, проведення хімічного процесу, 3 - для
приготування концентрату МІК-8 в оливі І-20 12, 13 - насоси: для
перекачування інгібітора корозії МІК-8, - для перекачування оливного
концентрату . 8, 9, 15 Збірники відповідно для зберігання: олеїнової
кислоти, триетаноламіну, індустріальної оливи І-20А,
В
результаті проведеного процесу отримують оливорозчинну рідину темно коричневого
кольору фізикохімічні властивості якої наведено у таблиці. 1
Таблиця
1
Фізикохімічні
властивості амідоестерного ОІК МІК-8
№ |
Параметр |
Значення |
|
1 |
Зовнішній вигляд |
Пастаподібна речовина або
рідина, чорного кольору |
|
2 |
Розчинність
у оливі |
Необмежено |
3 |
Розчинність
у спиртотолуольній суміші. |
Необмежено |
4 |
Температура
спалаху визначена у відкритому тиглі, оС |
>195 |
ГОСТ 4333 |
5 |
Густина,
при 20 оС, кг/м3 |
880-920 |
ГОСТ 3900 |
6 |
Вязкість
кінематична, при 50 оС, мм2/с. (ГОСТ 33) |
60-80* |
ГОСТ 33 |
7 |
Зольність
сульфатна, % |
0,5-1,6 |
ГОСТ 12417 |
8 |
Кислотне
число, мгКОН/г |
7-19 |
ГОСТ 11362 |
9 |
Число
омилення |
150-165 |
ГОСТ 21749 |
Захисна здатність 10% розчину в оливі І-20А,
відносно Ст10 |
9 |
В
умовах постійного занурення у електроліт, 200 годин |
Витримує |
ГОСТ 9.054 (метод 4) |
10 |
В
умовах камери сольового туману, 24 години |
Витримує |
ГОСТ 9.054 (метод 3) |
11 |
В
умовах підвищеної відносної вологості та підвищеної температури, 200 годин. |
Витримує |
ГОСТ 9.054 (метод 1) |
Відповідно
до технології, в таблиці 2 складено матеріальний баланс одержання 1т.
інгібітора МІК-8 (Таблиця 2).
Таблиця
2
Матеріальний баланс отримання 1 тони
оливорозчинного амідоестерного інгібітору корозії. (МІК-8)
Завантажено |
Отримано
|
№ |
Найменування |
% |
Кількість, кг |
№ |
Найменування |
% |
Кількість, кг |
1 |
Олеїнова к-та, тех.
|
84 |
921 |
1 |
Інгібітор корозії |
91,0 |
1000 |
2 |
Триетаноламін
|
10,6 |
120 |
2 |
Випарена вода |
8,0 |
86,5 |
3 |
карбамід
|
5 |
52,3 |
3 |
Втрати |
1,0 |
11,1 |
4 |
Гідроксид кальцію
|
0,4 |
4,3 |
|
|
|
|
6 |
Усього
|
100 |
1097,6 |
|
|
100 |
1097,6 |
ПОРІВНЯННЯ
ОЛИВОРОЗЧИННИХ ІНГІБІТОРІВ КОРОЗІЇ ТА КОНСЕРВАЦІЙНИХ ОЛИВ
7.1 Встановлення рівня
захисної здатності нового інгібітора корозії МІК-8 у порівнянні з товарними.
На даний час на теренах України та країн СНГ присутні
оливорозчинні інгібітори корозії як вітчизняного так і закордонного виробництв,
що відрізняються фізикохімічними параметрами та захисною ефективністю.
З метою встановлення оптимальних робочих концентрацій
у консерваційних оливах, та порівняння захисної ефективності в УкрНДІНП
"МАСМА" проводився комплекс робіт по дослідженню товарних та нових
оливорозчинних інгібіторів корозії. Випробування захисної здатності оливних розчинів
ІК проводили за ГОСТ 9.054, методом: 3 — в камері сольового туману, 4 – при
постійному зануренні у електроліт. В ході досліджень оцінювали площу Ст08пс та
СЧ 18, що була вражена корозією.
Результати
досліджень представлені у таблиці 1 та на Рис.1
Таблиця 1.
Випробування захисних властивостей оливорозчинних інгібіторів
корозії.
Інгібітор
корозії, концентрація
в оливі І-20А, %. |
Відсоток враженої поверхні за час
випробувань, % |
Після випробувань
у камері сольового туману |
Після випробувань
в електроліті, 15 діб |
Ст08пс |
Чавун СЧ 18 |
Ст08пс |
Чавун СЧ 18 |
КП–2 |
|
|
|
|
3 |
80 |
95 |
25 |
32 |
8 |
65 |
95 |
9 |
12 |
16 |
0 |
56 |
2 |
4 |
30 |
2 |
12 |
1 |
4 |
Dascogard– 60 |
|
|
|
|
3 |
5 |
75 |
2,75 |
3 |
8 |
0 |
15 |
2 |
3 |
16 |
0 |
10 |
0,5 |
0,5 |
30 |
0 |
5 |
0,35 |
0,5 |
Dascogard–233 |
|
|
|
|
3 |
8 |
85 |
2 |
2,5 |
8 |
3 |
20 |
1 |
1,2 |
16 |
0,5 |
12 |
0,7 |
1 |
30 |
0,1 |
8 |
0,7 |
1 |
МСДА–1 |
|
|
|
|
0,5 |
2 |
2 |
3,5 |
4 |
1 |
0 |
0 |
3 |
4 |
2 |
0 |
0 |
2 |
2,5 |
4 |
3 |
1 |
0,5 |
0,8 |
Телаз –ЛС |
|
|
|
|
3 |
72 |
65 |
15 |
12 |
8 |
55 |
52 |
8 |
10 |
16 |
32 |
25 |
2 |
4 |
30 |
7 |
8 |
2 |
2 |
МІК–8 |
|
|
|
|
3 |
15 |
12 |
6 |
7 |
8 |
3 |
2 |
0,6 |
3 |
16 |
0 |
0 |
0,3 |
0,5 |
30 |
0 |
0 |
0,3 |
1 |
І–20А |
85 |
87 |
100 |
100 |
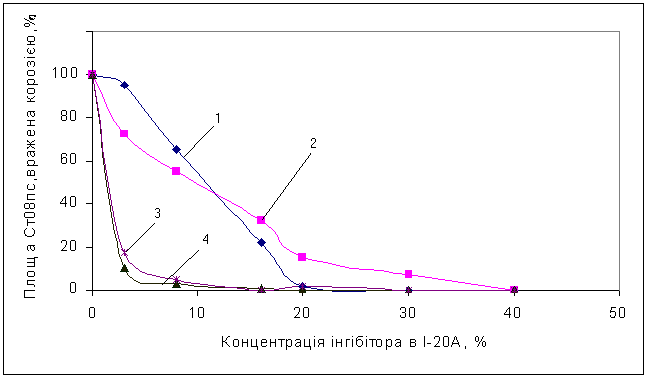
Рис 1. Залежність захисної ефективності оливи І-20А від
вмісту інгібіторів
1) КП-2 ; 2)Телаз –ЛС; 3) МІК-8; 4) Dascogard-233
За даними випробувань (Рис 1) встановлено, що захисні
властивості оливи І-20А з додаванням інгібітору МІК-8 знаходяться на рівні
композицій на основі інгібітору Dascogard-233. Мінімальна концентрація, що забезпечує захист
Ст08пс та СЧ 18, для інгібіторів МІК-8, Dascogard-233 складає 6 % (Рис 1,
крива 3, 4). Застосування 6%-их розчинів інгібіторів КП-2 та Телаз –ЛС,
за тих же умов, призводить до враження корозією 76% і 58 % поверхні Ст08пс
відповідно (Рис 1, крива 1, 2). Концентрація, при якій забезпечується досить
висока захисна здатність оливи І–20А, для інгібіторів КП-2 та ТЕЛАЗ-ЛС складає
18 - 25% (Рис 1, крива 3, 4). Тобто мінімальна ефективна концентрація у оливі
для інгбіторів МІК-8 і Dascogard-233 у 1,5 - 2 рази менша ніж для інгібіторів КП-2
та ТЕЛАЗ-ЛС.
7.2 Встановлення рівня
захисної здатності нових консерваційних олив, створених на основі інгібітора
корозії МІК-8, у порівнянні з товарними.
Окрім інгібітороів корозії, більшість зарубіжних
компаній, на ринку країн СНД представляють консерваційні оливи серед яких
відомі: Antikorit RP4107, Antikorit
6220/42 Е , (виробництва фірми Fuchs),
Саstrol safecoat 66 , Rustilo
650 (компания Castrol ), Shell Ensis Oil N (компания Shell), Автокон-ЛС ( ООО
«Автокон», м. Москва ), ОКС-2 (фірма Кальві, м. Львів), ЖКС-40 (ВАТ АЗМОЛ, м.
Бердянськ), К-17 (фірма “Триботехника”).
З метою встановлення ефективності захисту від корозії
виробів з чорного металу при транспортуванні та зберіганні, були проведені
порівняльні випробування нових та відомих консерваційних олив вітчизняного та
зарубіжного виробництва. За результатами випробувань (табл. 3) встановлено, що
консерваційні оливи мають різну захисну ефективність. Так за одну добу
випробувань у камері сольового туману, поверхня пластинок Ст08пс і СЧ 18, що
були захищені оливами Antikorit 6120/42Е, Волгол-131,
МАГ-11, МАГ-15 в середньому прокородувала на 1% і 4% відповідно. При захисті оливами Shell Ensis Oil N та ОКС-2 вражена корозією площа
становила відповідно для пластинок Ст08пс: 51% і 62%, СЧ 18: 82% і 80%, що
свідчить про низькі захисні властивості даних продуктів.
Оливи МАГ-11, МАГ-15 Автокон-ЛС, та ЖКС- 40, Волгол-131 за
властивістю захищати пластинки Ст08пс і СЧ 18 від агресивної дії електроліту
знаходяться на рівні зарубіжних олив Antikorit
6120/42Е, Antikorit RP4107, Rustilo 650 та Саstrol, safecoat 66.
Таблиця 3.
Результати випробувань захисних властивостей
консерваційних олив.
Консерваційна
олива |
Поверхня вражена корозією, за
час випробування, % |
Після випробувань у камері
сольового туману. |
Після
випробувань у електроліті. |
Ст08пс |
Чавуні СЧ 18 |
Ст08пс |
Чавуні СЧ 18 |
Antikorit 6120/42Е |
1 |
4 |
2 |
3 |
Antikorit RP4107 |
1 |
3 |
1,8 |
2,5 |
Shell Ensis Oil
N |
51 |
82 |
6 |
10 |
Саstrol, safecoat 66 |
18 |
30 |
3 |
7 |
Rustilo 650 |
6 |
8 |
2 |
6 |
Автокон-ЛС |
16 |
10 |
2,2 |
4 |
Волгол-131 |
1 |
4 |
1,6 |
5 |
К-17 |
15 |
22 |
6 |
9 |
ЖКС-40 |
75 |
50 |
4,2 |
13 |
МАГ-11 |
1,5 |
3 |
1,5 |
2,5 |
МАГ-15мз |
0,2 |
1,2 |
0,5 |
0,5 |
ОКС-2 |
65 |
80 |
7,5 |
19 |
І-20А |
85 |
100 |
100 |
100 |
З
результатів випробувань захисних властивостей встановлено, що нові
оливорозчинні інгбітори корозії серії МІК, а також консерваційні оливи на їх
основі ( МАГ-11, МАГ-15мз ) за здатністтю захищати вироби з чорних металів від
корозії, непоступаються, а в деяких випадках перевершують відомі засоби
тимчасового захисту металовиробів.
Враховуючи
позитивні результати заводських випробуваннь (в умовах “Київського
мотоциклетного заводу”) (Додаток 1), консерваційну оливу МАГ-11 можна
рекомендувати для застосування при зберіганні виробів з СЧ 50, Ст3, Ст 10, Ст40
у складських умовах протягом 1 року.
ВИСНОВКИ
1) Встановлно особливості синтезу інгібіторів корозії на основі
похідних карбаміду.
2) Розроблено оливорозчинний інгібітор корозії на основі похідних
карбаміду МІК-8
3) Досліджено вплив рецептурно-технологічних факторів на основні
властивості оливорозчинного інгібітору корозії МІК-8
4) Встановлені закономірності впливу вуглеводневого складу та
характеристик базових олив на захисні властивості консерваційних олив які
містять новий оливорозчинний інгібітор корозії МІК-8.
2) Дослідити взаємний
вплив ІК та оливорозчинних додатків різної функціональної дії на основні
властивості консерваційних олив.
3) Розроблено рецептуру
консерваційної оливи на основі нового оливорозчинного інгібітору корозії.
4) У порівнянні з
відомими товарними аналогами зарубіжного і вітчизняного виробництва встановлено
високий рівень захисної здатності нових засобів тимчасового захисту металовиробів.
|
|